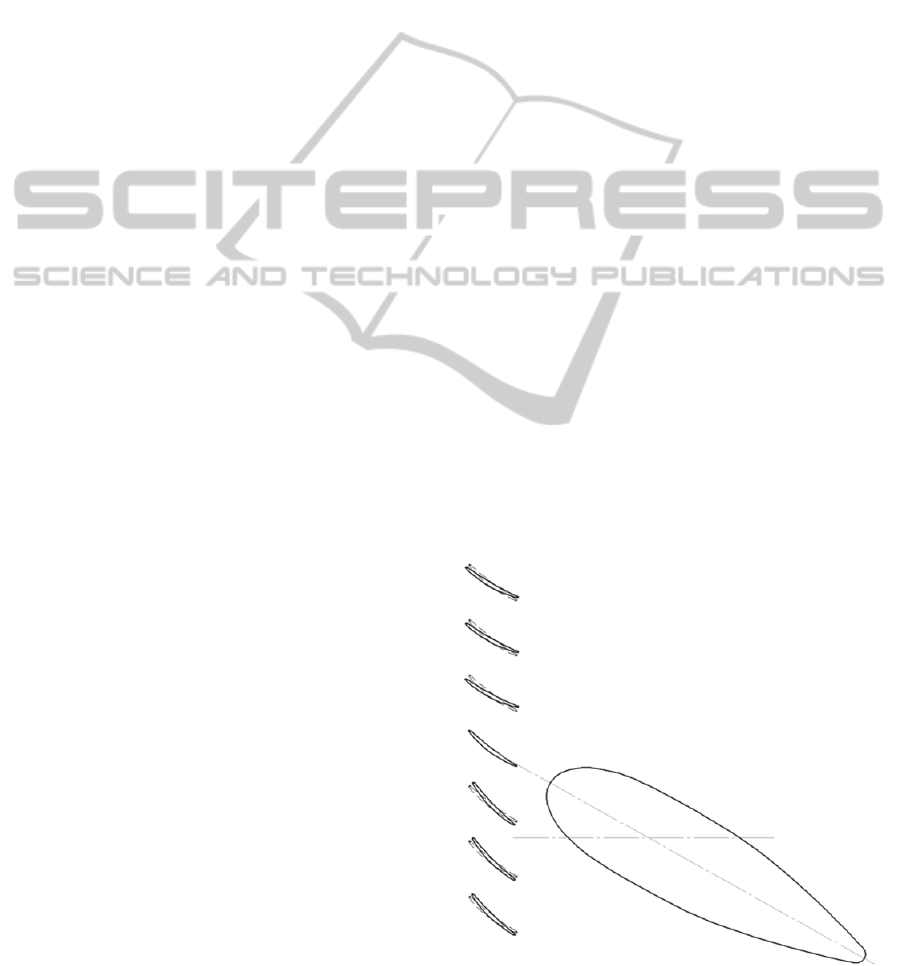
3 THE MEASURES FOR BLADES
ALTERNATING STRESSES
MITIGATION
The following areas were selected as measures to
reduce the resonant stresses level:
the usage of the blades with special Shvarov’s
profile at last rotor wheel;
the usage of the guide vane in front of the
middle support, with the blades set having
different stagger angles and with
circumferentially alternating blade pitch.
Also, special attention was paid to the fact that
the number of blades with stagger angles different
from the standard should be as low as possible.
Parameterization of the full circle compressor
model was carried out for the introduction GV5
different stagger angles and circumferentially
alternating blade pitch.
At the first stage of creating a parametric model
the support racks and blades of GV5 were divided
into groups. For this purpose the development
drawing of the blade row in the circumferential
direction was carried out. The assumption that for
several blade groups will be given the same stagger
angle and blade pitch parameters was made for IPC
GV5 blades. When introducing the different stagger
angles the key factor was the minimum number of
changeable blades as the manufacturing a large
number of blades with different geometry greatly
increase the production costs. The quantity of the
variable blades in group was specified by the
number in brackets (Table 1).
Then, the maximum blade stagger angle within
the joint groups was determined. The stagger angle
was not changed for the GV5 blades located in the
racks plane of symmetry, the first and last blades in
the group. Changing of the stagger angles within the
groups were performed linearly. Blades arranged on
opposite sides of the racks plane of symmetry were
rotated in opposite directions relative to the initial
position (Figure 4). Moreover the blades located
closer to the front were rotated by a larger angle. If
the blade was rotated on closing (increase of the
stagger angle) before the angle value there is a sign
"+" if on opening (decrease of the stagger angle) -
sign "-".
The number of removable blades was not
restricted when blade pitch were changed. Parameter
of alternating blade pitch was set within 0.35...0.35
of the base pitch. The sign "-" means that in the
region between the blades the pitch is decreased,
while "+" - the pitch is increased. The number
indicates the maximum blade pitch increase
(decrease) in the group in relative values from the
nominal pitch with evenly spaced blades. Position of
extreme blades in groups was not changed when
introducing the circumferentially alternating blade
pitch. The law of pitch changing was also linear.
Thus, the universal parametric model which allows
to the introduction different stagger angles and
circumferentially alternating blade pitch at the IPC
fifth stage was created.
4 OPTIMIZATION
CALCULATIONS OF THE
DYNAMIC STRESSES IN THE
IPC FIFTH ROTOR BLADE
Calculations of dynamic stress for 11 variants of the
IPC fifth stage were performed using a parametric
model (Shklovets, Popov, Kolmakova, 2013). Blade
with a special Shvarov’s profile was used as the fifth
stage rotor blade in all the variants. The variants
differed from each in values of different stagger
angles and alternating blade pitch parameters of IPC
GV5. At the same time the first variant corresponded
to the base GV5.
The calculation results of the dynamic stresses
which arise at a resonance with the strongest 12th
harmonic, parameters of each variant as well as the
total number of GV variable blades of IPC fifth
stage are shown in Table 1.
Figure 4: Rotation scheme of guide vane blades.
MethodstoReducetheResonantStressesLevelofGasTurbineEnginesCompressorRotorWheels
621