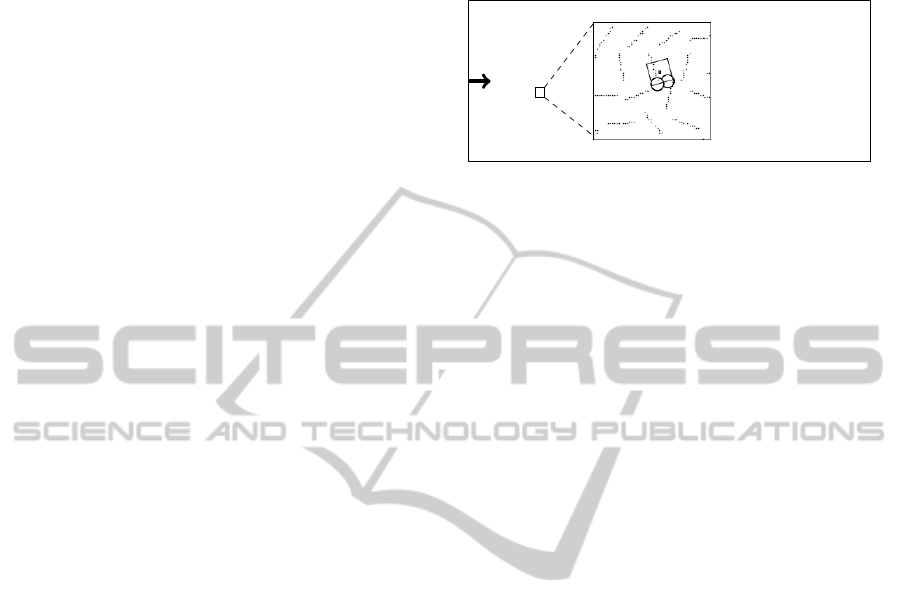
control during manufacture. Sensor assembly varia-
tion (sensor height, lateral offset and sagittal offset)
are comparably small comparing with variations on
the motor and gearbox gain, and wheel separation.
Details of robotic parameters and the sigma values for
Gaussian process are summarized in Table 1.
3.3 Training
A total of approximately 210 different robots were
generated and then individually trained using a sim-
ple line-following task for the optimal coefficients of
the PI controller using exhausted search method. A
single period sinusoid reflective line was used, as the
robot’s ability of both turning right and left would be
trained without any bias. During training all robots
have the same initial training condition: they all starts
with exactly the same position located at the begin-
ning of the sinusoid line with exactly the same orien-
tation. For every robot, this task will be repeated for a
number of times to test different sets of controller co-
efficients. The controller parameters which help the
robot achieve the best accuracy in terms of following
the target line will be chosen as the optimal parame-
ters.
To evaluate the training results, the trajectory of
each robot which is achieved with the optimal param-
eters is nearly the same with the shape of one period
of sinusoid. Therefore, the uniform training method
has helps the robots to achieve almost the same trajec-
tories. In other words, the optimal parameters com-
pensate the hardware difference among robots and
similar behaviors have been generated.
3.4 Testing
After training, robots were then tested in the testing
arena illustrated in Fig 3. The testing arena is a long
rectangle shaped area. A large number of short re-
flective lines are drawn in the arena with randomized
orientations. All lines sit on the grid, so that they do
not overlap each other. The initial condition for all
robots are the same: they all start on the left hand side
of the arena with the same location, same orientation.
While robots were doing the line-following task and
interacting with the reflective lines in the arena, the
following assumption was made. In the simulation we
consider that there is a constant “wind” from the left
to the right of the arena, which can influence a robot’s
speed and orientation. This is analogous to a small
sail on top of each robot. If there exists difference be-
tween the direction of the wind and orientation of the
robot, a force will be applied to the robot by the sail
so that the orientation of the robot will change to con-
form to the wind direction and also a subcomponent
of speed to the right will be applied to the robot.
Figure 3: A small square-shape region has been magnified,
allowing the length of the line and robot compared. The
starting point of each robots and their orientation is denoted
by the arrow. The size of the robot is 10×10 in arbitrary
unit. The arenas dimension is in the same unit.
Within the model, if the orientation of the robot
and direction of the wind is different, the speed of
each robot at each simulation step is the vector addi-
tion of the robotic autonomous speed and a subcom-
ponent of speed which is due to the blowing wind, and
an angular speed is added to the robot which force the
robot to orientate to the right. The reason of making
this assumption is that in order to separate all robot as
loosely as possible, a tendency of moving to the right
of the arena for all robots has to be enforced.
To further reduce the complexity of the problem,
all robots will be separated based only on their po-
sition on the arena’s x axis. Therefore when the
robots go beyond either upper or lower boundary of
the arena, it is assumed that they will be picked up
and put into the arena from the other side which is
the lower or upper boundary accordingly with main-
tained orientation. In this case, the position of robots
with reference to the arena y axis will not matter any
more.
Given the size of the arena, robots are able to run
in the arena for extended periods of time, thus robots
can be separated along the x axis as loosely as possi-
ble.
4 RESULTS AND DISCUSSION
Approximately 210 robots have been simulated in two
arenas (Arena1 and Arena2). Results are shown in
Fig 4 and 5. The only difference between Arena1
and Arena2 is the orientation of the reflective patterns.
According to the results from both arenas, it is found
out that some robots consistently led in the front or
left behind in both arenas.
As shown in Fig 5, the rank of robots in terms of
x coordinates for their end points after a fixed sim-
ulation period are almost consistent in both arenas.
SIMULTECH2014-4thInternationalConferenceonSimulationandModelingMethodologies,Technologiesand
Applications
634