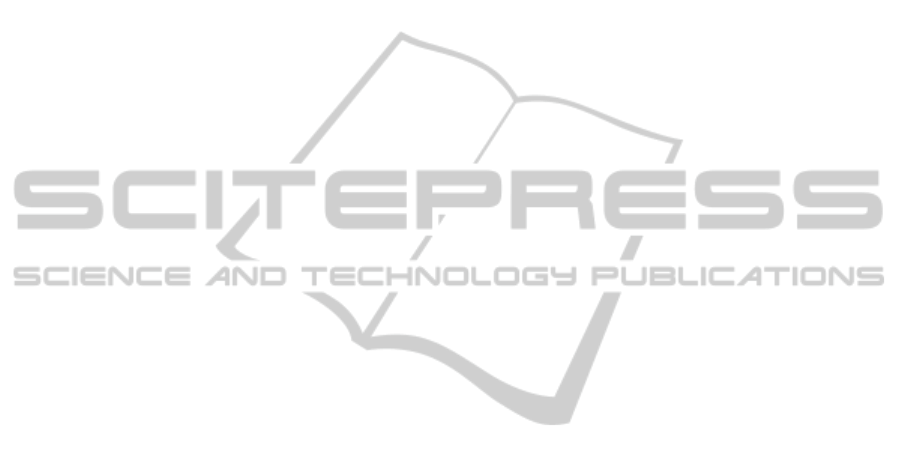
4 CONCLUSIONS
This paper introduces a new adaptive control scheme
to enhance the tracking performances for a flexible
endoscopic system using cable-conduit mechanisms.
The proposed control laws are able to deal with non-
linearities in the presence of uncertainties and dis-
turbances. Unlike current approaches of the cable-
conduit control, our control scheme has efficiently
reduced the tracking error and robustness. Experi-
mental validations have been carried out using a real
master-slave system to evaluate the controller perfor-
mances. Comparisons between the proposed model
and the experimental data show a good agreement.
It has been demonstrated that the model approach
works well on a real surgical device (Master-Slave
system) in NOTES system to carry out the task of
gripping a real object. It has also been indicated
that the proposed scheme is able to track the de-
sired reference signal regardless of the configuration
of the endoscope. In addition, no knowledge of exact
backlash hysteresis parameters is required. The pro-
posed control scheme has opened potential benefits to
other flexible endoscopic system for enhancing track-
ing performances of precise motion. Future activities
will be conducted the validations for higher degrees
of freedom of flexible endoscopic systems. In addi-
tion, in-vivo on live animal and human will be carried
out for further validations.
REFERENCES
Abbott, D., Becke, C., Rothstein, R., and Peine, W.
(2007). Design of an endoluminal notes robotic sys-
tem. In IEEE/RSJ International Conference on Intel-
ligent Robots and Systems, IROS,, pages 410–416.
Agrawal, V., Peine, W., Yao, B., and Choi, S. (2010a).
Control of cable actuated devices using smooth back-
lash inverse. In IEEE International Conference on
Robotics and Automation (ICRA), pages 1074–1079.
Anchorage, AK.
Agrawal, V., Peine, W. J., and Yao, B. (2010b). Modeling
of transmission characteristics across a cable-conduit
system. IEEE Transactions on Robotics, 26(5):914–
924.
Bardou, B., Nageotte, F., Zanne, P., and De Mathelin, M.
(2012). Improvements in the control of a flexible en-
doscopic system. In IEEE International Conference
on Robotics and Automation (ICRA), pages 3725–
3732. Saint Paul, MN.
Cai, J., Wen, C., Su, H., and Liu, Z. (2013). Robust adaptive
failure compensation of hysteretic actuators for a class
of uncertain nonlinear systems. IEEE Transactions on
Automatic Control, 58(9):2388–2394.
Chiang, L. S., Jay, P. S., Valdastri, P., Menciassi, A.,
and Dario, P. (2009). Tendon sheath analysis for
estimation of distal end force and elongation. In
IEEE/ASME International Conference on Advanced
Intelligent Mechatronics (AIM), pages 332–337.
Clark, M. P., Qayed, E. S., Kooby, D. A., Maithel, S. K., and
Willingham, F. F. (2012). Natural orifice translumenal
endoscopic surgery in humans: a review. Minimally
invasive surgery, 2012.
Do, T. N., Tjahjowidodo, T., Lau, M. W. S., and Phee, S. J.
(2013a). Dynamic friction model for tendon-sheath
actuated surgical robots: modelling and stability anal-
ysis. In ISRM 2013-Proceedings of the 3rd Inter-
national Symposium on Robotics and Mechatronics,
pages 302–311. Singapore.
Do, T. N., Tjahjowidodo, T., Lau, M. W. S., and Phee, S. J.
(2013b). Nonlinear modeling and parameter identi-
fication of dynamic friction model in tendon sheath
for flexible endoscopic systems. In ICINCO 2013-
Proceedings of the 10th International Conference on
Informatics in Control, Automation and Robotics,
pages 5–10. Reykjavik, Iceland.
Do, T. N., Tjahjowidodo, T., Lau, M. W. S., and Phee, S. J.
(2014a). Dynamic friction-based force feedback for
tendon-sheath mechanism in notes system. Interna-
tional Journal of Computer and Electrical Engineer-
ing, 6(3):252–258.
Do, T. N., Tjahjowidodo, T., Lau, M. W. S., and Phee, S. J.
(2014b). An investigation of friction-based tendon
sheath model appropriate for control purposes. Me-
chanical Systems and Signal Processing, 42(1-2):97–
114.
Do, T. N., Tjahjowidodo, T., Lau, M. W. S., Yamamoto, T.,
and Phee, S. J. (2014c). Hysteresis modeling and po-
sition control of tendon-sheath mechanism in flexible
endoscopic systems. Mechatronics, 24(1):12 – 22.
Hassani, V., Tjahjowidodo, T., and Do, T. N. (2014). A
survey on hysteresis modeling, identification and con-
trol. Mechanical Systems and Signal Processing,
49(1):209–233.
Hu, C., Yao, B., and Wang, Q. (2013). Performance-
oriented adaptive robust control of a class of nonlinear
systems preceded by unknown dead zone with com-
parative experimental results. IEEE/ASME Transac-
tions on Mechatronics, 18(1):178–189.
Kaneko, M., Paetsch, W., and Tolle, H. (1992). Input-
dependent stability of joint torque control of tendon-
driven robot hands. IEEE Transactions on Industrial
Electronics, 39(2):96–104.
Kesner, S. and Howe, R. (2011). Position control of motion
compensation cardiac catheters. IEEE Transactions
on Robotics, 27(6):1045–1055.
Kesner, S. B. and Howe, R. D. (2014). Robotic catheter
cardiac ablation combining ultrasound guidance and
force control. The International Journal of Robotics
Research, 33(4):631–644.
Minh, T. V., Kamers, B., Tjahjowidodo, T., Ramon, H.,
and Van Brussel, H. (2010). Modeling torque-angle
hysteresis in a pneumatic muscle manipulator. In
IEEE/ASME International Conference on Advanced
Intelligent Mechatronics (AIM), pages 1122–1127.
ICINCO2014-11thInternationalConferenceonInformaticsinControl,AutomationandRobotics
116