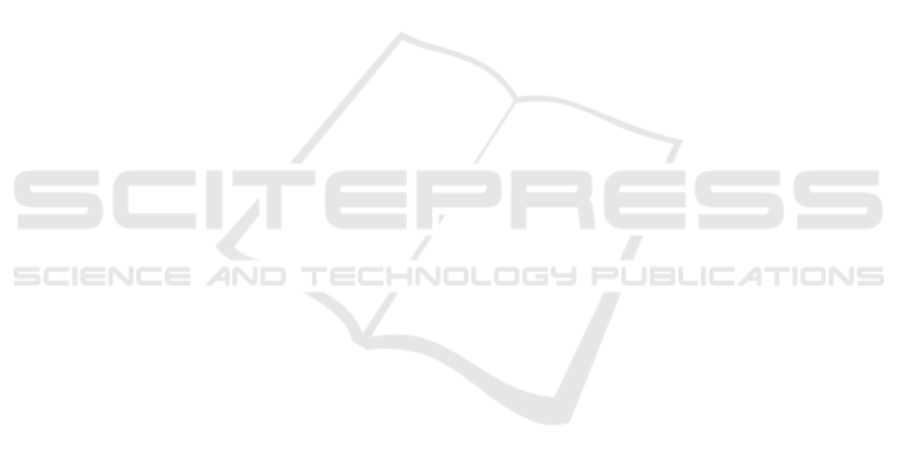
Joint Stiffness Identification of a Heavy Kuka Robot with a Low-cost
Clamped End-effector Procedure
A. Jubien
1,2
, G. Abba
3
and M. Gautier
1
1
IRCCyN (Institut de Recherche en Communications et Cybernétique de Nantes), Nantes, France
2
ONERA (The French Aerospace Lab), Toulouse, France
3
Dep. of Design, Manufacturing and Control (LCFC) and ENIM (National College of Engineering of Metz), Metz, France
Keywords: Stiffness, Industrial, Robot, Identification, Clamped End-effector.
Abstract: This paper proposes two new methods for the identification of static stiffnesses of multi degrees of freedom
heavy industrial robots. They are based on a locked link joint procedure obtained with an end-effector fixed
to the environment. The first method requires only measurements of motor positions and motor torques data
computed from motor current measurements and manufacturer's drive gains. The second one needs a torque
sensor to measure the interaction wrench between the clamped end-effector and the environment. These
methods are being experimentally validated and compared on the 2 first joints of a 6 degrees of freedom
heavy 500Kg payload industrial Kuka KR500 robot.
1 INTRODUCTION
New applications of heavy industrial robots for
performing machining operations like Friction Stir
Welding process (FSW) need trajectories with a high
accuracy end-effector position while significant
forces are applied to the end-effector.
It is then necessary to identify accurately the
stiffnesses to control and simulate precise and
reliable motion. Identification of rigid robots has
been widely investigated in the last decades, based
on the Inverse Dynamic Identification Model and
Least Squares estimation (IDIM-LS) (Hollerbach et
al., 2008). Several approaches can be used to
identify the dynamic parameters and joint dynamic
stiffnesses. One approach is based on IDIM-LS
technique and needs motor and joint positions and
motor torques (Pham et al., 2001); (Janot et al.,
2011). However, the joint positions are not measured
on industrial robots. Another approach is a closed-
loop output error method which needs to simulate
the robot (Gautier et al., 2013); (Östring, 2003).
Unfortunately, manufacturers do not want to give
the control laws of their controllers.
Another approach avoids using any internal data
(joint position, motor torque, control law) but it
requires an external measurement of the position of
the end-effector using very expensive laser-tracker
sensor with variation of the payload while the motor
positions are locked to constant values (Dumas et
al., 2011); (Alici and Shirinzadeh, 2005). In (Pfeiffer
and Holzl, 1995), each robot links are fixed
alternately to identify the current joint stiffness with
quasi-static test but this requires a different locking
system for each link.
To overcome theses expensive and heavy
procedures, this paper proposes two new methods
based on a locked link joint procedure obtained with
the end-effector clamped to the environment. The
first method requires only motor positions
measurement and motor torques data calculated
from motor current measurement and manufacturer's
drive gain data. The second one needs a torque
sensor to measure the external interaction wrench
between the clamped end-effector and the
environment, which are calculated as external link
torques using the jacobian matrix of the robot. A
first validation of our methodologies are carried out
on the 2 first joints of a 6 Degrees of Freedom (dof)
heavy 500Kg payload industrial Kuka KR500 robot.
This paper is divided into 5 sections. Section 2
describes the modeling of serial robots with the end-
effector attached to the base. Section 3 presents the
usual method for dynamic identification of robots,
based on IDIM-LS method. Section 4 is devoted to
the modeling of the Kuka KR500 heavy industrial
robot and to the identification of the first two axis of
the robot. The last section gives the conclusion.
585
Jubien A., Abba G. and Gautier M..
Joint Stiffness Identification of a Heavy Kuka Robot with a Low-cost Clamped End-effector Procedure.
DOI: 10.5220/0005115805850591
In Proceedings of the 11th International Conference on Informatics in Control, Automation and Robotics (ICINCO-2014), pages 585-591
ISBN: 978-989-758-040-6
Copyright
c
2014 SCITEPRESS (Science and Technology Publications, Lda.)