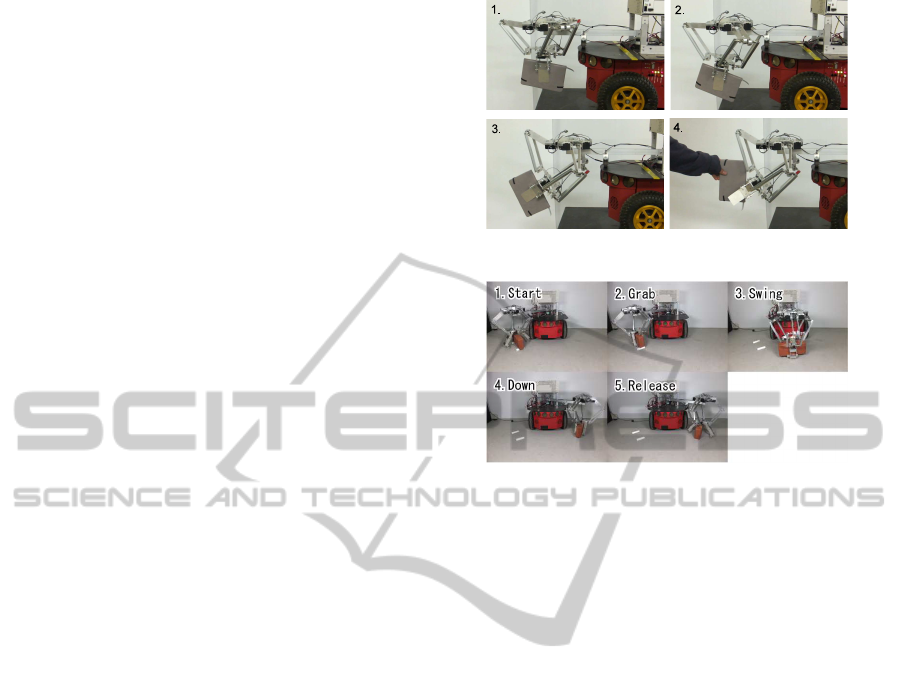
Figure 13 shows transitions of n
θ
, n
h
, p
h
(t), and
r
h
(t) to the time step in this motion. Each result was
obtained in the same way as previous motion. In this
case, the angle of swing link θ
swing
is changed linearly
to move the hand so that the destination comes in the
workable area of hand. The hand rotation angle θ
z
is
changed corresponding to the change of θ
swing
to keep
the orientation of the object.
5 EXPERIMENTS
5.1 Forward Handing Motion
Figure 14 shows an experiment for handing object.
The robot kept grasping a B4-size notebook (panel 1
in Fig. 14), started rotating the hand after slight down
(panel 2), carry the object forward (3), and handed it
by opening the hand (4). It was actually difficult to
rotate the hand forward so that the object orients hor-
izontally as shown in Fig. 10 due to some mechanical
constraints of the second and third joints of link-units.
Nevertheless, this result indicates the ability of hand-
ing task of the robot with parallel link arm.
5.2 Pick and Place from Side to Side
The robot carried an object from right to left with
swinging motion. Figure 15 shows a sequence of the
motion in this experiment. We used a 2.1 [kg] brick
as the target object, which was 100 [mm] in length,
200 [mm] in width, and 52 [mm] in height. The robot
moved the hand down at the right side (panel 1 in
Fig. 15), started grasping the object (panel 2). Af-
ter lifted it up slightly, the robot was swinging it the
parallel link arm to the left side (3). The robot finally
stopped swinging at the destination and touched the
object to the floor (4) and released it (5). This result
verified the validity of working area by utilizing the
swing link.
Although it was actually difficult to move hand
so as to keep its orientation as shown in Fig. 12 due
to some mechanical constraints, this kind of motion
shows that the robot has an ability of performing han-
dling tasks in small space, such as an arrangement of
books between book-shelves in library.
6 CONCLUSIONS
We have developed a parallel link arm to be mounted
on a wheeled mobile robot. Kinematic analysis and
Figure 14: Handing object forward.
Figure 15: Picking and placing from right to left side.
basic motions of the parallel link arm have been pre-
sented. Simulations and experiments confirmed ba-
sic handling motions of the arm even though it had
some mechanical constraints. More detailed kine-
matic analysis should be considered. In future, we
will confirm the potential of the robot by demonstrat-
ing variety of work in wide area as well as narrow
space with the advantage of parallel link by which it
can handle heavier object than serial link manipulator.
REFERENCES
Decker, M., Dang, A., and Ebert-Uphoff, I. (2001). Motion
planning for active acceleration compensation. In Pro-
ceedings of IEEE ICRA 2001, volume 2, pages 1257–
1264.
Gosselin, C. and Angeles, J. (1990). Singularity analysis of
closed-loop kinematic chains. IEEE Transactions on
Robotics and Automation, 6(3):281–290.
Graf, R. and Dillmann, R. (1997). Active Acceleration
Compensation Using a Stewart-Platform on a Mobile
Robot 2 The mobile robots 1 Introduction. In 2nd Eu-
romicro Workshop on Advanced Mobile Robots, pages
59–64.
Horin, P., Djerassi, S., Shoham, M., and Horin, R. (2006).
Dynamics of a six degrees-of-freedom parallel robot
actuated by three two-wheel carts. Multibody System
Dynamics, 16(2):105–121.
Li, Y., Xu, Q., and Liu, Y. (2006). Novel design and model-
ing of a mobile parallel manipulator. In Proceedings
of IEEE ICRA 2006, pages 1135–1140.
Pierrot, F., Uchiyama, M., Dauchez, P., and Fournier, A.
DevelopmentofaParallelLinkArmforObjectHandlingbyWheeledMobileRobot
597