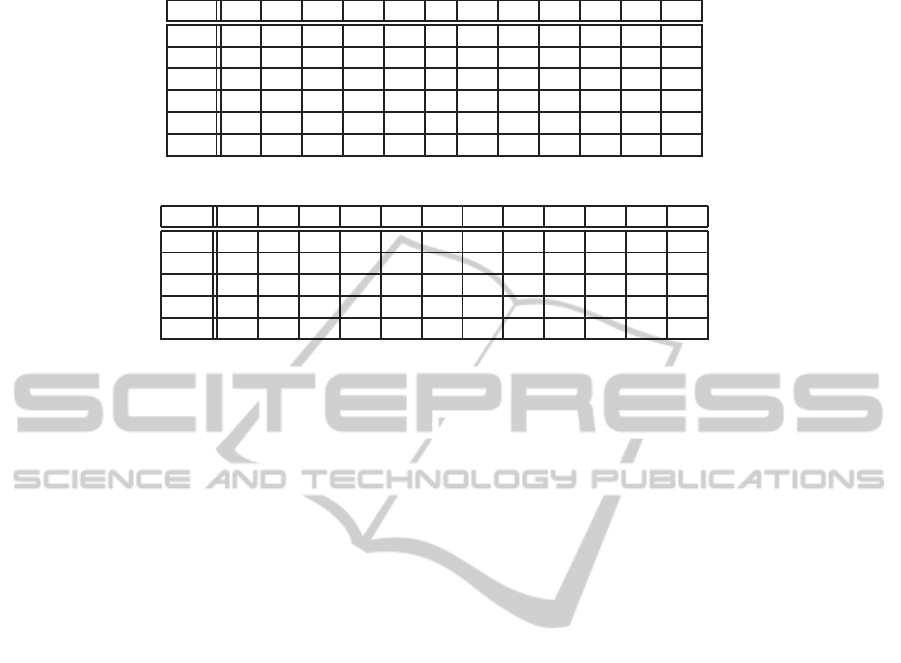
Table 6: Example – Solution variable s
v
r,t
(remanufacturing process).
t → 1 2 3 4 5 6 7 8 9 10 11 12
s
1
1,t
0 0 0 0 0 2 0 0 0 0 0 0
s
2
1,t
22 0 0 5 15 3 8 12 0 0 0 0
s
3
1,t
13 10 0 0 0 0 2 3 0 0 0 0
s
1
2,t
15 0 16 17 5 6 20 0 0 0 0 0
s
2
2,t
7 0 1 0 0 0 0 0 4 13 8 0
s
3
2,t
10 0 11 11 7 6 0 16 20 15 0 0
Table 7: Example – Solution variable a
B
p,t
(basic parts recovered in the remanufacturing process).
t → 1 2 3 4 5 6 7 8 9 10 11 12
a
B
11,t
32 40 28 63 47 27 35 41 44 58 43 10
a
B
16,t
32 89 56 67 54 50 48 57 69 64 43 10
a
B
19,t
0 49 28 4 7 23 13 16 25 6 0 0
a
B
20,t
0 98 56 8 14 46 26 32 50 12 0 0
a
B
21,t
0 98 56 8 14 46 26 32 50 12 0 0
manufacturing part and of the remanufacturing one)
and unlimited availability of returned products have
been assumed in this analysis, in order to make the
sensitiveness independent from the availability of ma-
chines and of products to be disassembled in order to
recover basic parts.
5 CONCLUSIONS
This work proposes a MIP model for planning man-
ufacturing activities in a multi-product, multi-stage
production plant which includes a remanufacturing
facility. The considered model assumes a simplified
aggregate production characterized by deterministic
information on demand and availability of returned
products. The presented experimental analysis points
out the applicability of the model at least for small-
medium size instances (the problem in the consid-
ered example has about 1150 variables and 560 con-
straints), as well as the coherence of the model be-
haviour with respect to the variations of part acquisi-
tion costs. In any case, more extensive testing with
larger instances is on its way. Besides, future im-
provements of this model will focus on the consider-
ation of explicit setups and on the relaxation of some
of the deterministic assumptions.
REFERENCES
Chen, K. and Ji, P. (2007). A mixed integer program-
ming model for advanced planning and scheduling
(aps). European Journal of Operational Research,
181(1):515–522.
Fleischmann, M., Bloemhof-Ruwaard, J. M., Dekker, R.,
van der Laan, E., van Nunen, J. A., and Van Wassen-
hove, L. N. (1997). Quantitative models for reverse
logistics: A review. European Journal of Operational
Rcsearch, 103:1–17.
Florian, M., Lenstra, J., and Rinnooy Kan, A. (1980). De-
terministic production planning: Algorithms and com-
plexity. Management Science, 26(7):669–679.
Guide Jr., V. D. R. (2000). Production planning and control
for remanufacturing: industry practice and research
needs. Journal of Operations Management, 18:467–
483.
Guide Jr., V. D. R. and Van Wassenhove, L. N. (2009). The
evolution of closed-loop supply chain research. Oper-
ations Research, 57(1):10–18.
Kolisch, R. and Hess, K. (2000). Efficient methods for
scheduling make-to-order assemblies under resource,
assembly area and part availability constraints. Inter-
national Journal of Production Research, 38(1):207–
228.
Lund, R. T. (1985). Remanufacturing: The experienceof the
united states and implications for developing coun-
tries. World Bank Technical Paper 31, The World
Bank.
Shi, J., Zhang, G., and Sha, J. (2011). Optimal production
planning for a multi-product closed loop system with
uncertain demand and return. Computers & Opera-
tions Research, 38:641–650.
Teunter, R. H., Bayindir, Z. P., and Van Den Heuvel, W.
(2006). Dynamic lot sizing with product returns and
remanufacturing dynamic lot sizing with product re-
turns and remanufacturing dynamic lot sizing with
product returns and remanufacturing. International
Journal of Production Research, 44(20):4377–4400.
Thierry, M., Salomon, M., Van Nunen, J., and Van Wassen-
hove, L. N. (1995). Strategic issues in product re-
covery management. California Management Review,
37(2):114–135.
Tonelli, F., Paolucci, M., Anghinolfi, D., and Taticchi, P.
(2013). Production planning of mixed-model assem-
bly lines: A heuristic mixed integer programming
based approach. Production Planning and Control,
24(1):110–127.
Zhang, H., Li, J., Shrivastava, P., Whitley, A., and Mer-
chant, M. E. (2004). A web-based system for reverse
manufacturing and product environmental impact as-
sessment considering end-of-life dispositions. CIRP
Annals - Manufacturing Technology, 53(1):5–8.
AMixed-IntegerMathematicalProgrammingModelforIntegratedPlanningofManufacturingandRemanufacturing
Activities
759