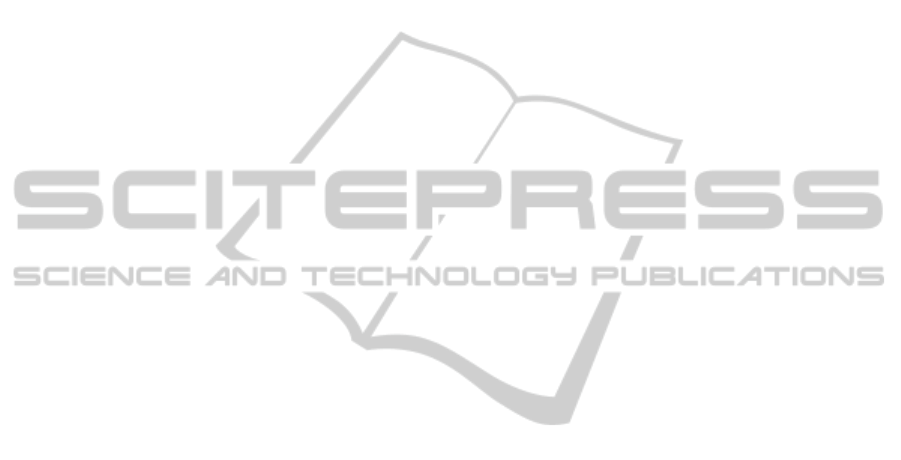
March 2014
ANSI/RIA, ANSI R15.06-1999: American National
Standard for Industrial Robots and Robot Systems—
Safety Requirements. American National Standards
Institute/Robotics Industry Association, 1999.
Casa, S. “Personensicherer Betrieb von Robotern ohne
konventionelle Sicherheitsmassnahmen. MSc. Thesis.
InES, ZHAW, Winterthur Switzerland 2012.
Elshafie, M.; Bone, G. M., "Markerless human tracking
for industrial environments, "Electrical and Computer
Engineering, 2008. CCECE 2008. Canadian
Conference on, vol., no., pp.001139, 001144, 4-7 May
2008.
Graf, J.; Puls, S.; Worn, H., "Incorporating Novel Path
Planning Method into Cognitive Vision System for
Safe Human-Robot Interaction, "Future Computing,
Service Computation, Cognitive, Adaptive, Content,
Patterns, 2009. COMPUTATIONWORLD '09.
Computation World: vol., no., pp.443,447, 15-20 Nov.
2009.
Gall, H., "The TUV approach to functional safety
assessment and certification," Is Your Product Safe? -
IEE Seminar on (Ref. No. 2004/10724), vol., no.,
pp.29, 52, 16-16 Sept. 2004.
Hong L., Jie Z., "Motion planning for Human-Robot
Interaction based on stereo vision and SIFT, "Systems,
Man and Cybernetics, 2009. SMC 2009. IEEE
International Conference on, vol., no., pp.830,834, 11-
14 Oct. 2009.
Heyer, C., "Human-robot interaction and future industrial
robotics applications," Intelligent Robots and Systems
(IROS), 2010 IEEE/RSJ International Conference on,
vol., no., pp.4749,4754, 18-22 Oct. 2010.
Infante, M. L.; Kyrki, V., "Usability of force-based
controllers in physical human-robot
interaction," Human-Robot Interaction (HRI), 2011
6th ACM/IEEE International Conference on, vol., no.,
pp.355,362, 8-11 March 2011.
ISO, ISO 10218-1:2011: Robots and robotic devices
Safety requirements for industrial robots Part 1:
Robots. Geneva, Switzerland: International
Organization for Standardization, 2011.
ISO, ISO 10218-2:2011: Robots and robotic devices
Safety requirements for industrial robots Part 2: Robot
Systems and Integration. Geneva, Switzerland:
International Organization for Standardization, 2011.
Kulić, D., Croft, E., “Pre-collision safety strategies for
human-robot interaction”, Autonomous Robots,
Volume 22, Issue 2, pp 149-164, February 2007.
Lacevic, B.; Rocco, P.; Zanchettin, A. M., "Safety
Assessment and Control of Robotic Manipulators
Using Danger Field, "Robotics, IEEE Transactions on,
vol.29, no.5, pp.1257,1270, Oct. 2013.
LaValle, S., M. “Rapidly-Exploring Random Trees, A
New Tool for Path Planning” (1998).
http://citeseerx.ist.psu.edu/viewdoc/summary?doi=10.
1.1.35.1853 last accessed 04
th
July 2014.
Lenz, C.; Panin, G.; Roder, Thorsten; Wojtczyk, M.;
Knoll, A., "Hardware-assisted multiple object tracking
for human-robot-interaction," Human-Robot
Interaction (HRI), 2009 4th ACM/IEEE International
Conference on, vol., no., pp.283,284, 11-13 March
2009.
Lenz, C., Grimm, M., Röder, T., Knoll, A. „Fusing
multiple Kinects to survey shared Human-Robot-
Workspaces,” http://mediatum.ub.tum.de/attfile/1115
447/hd2/incoming/2012-Sep/934684.pdf last accessed
14th March 2014.
Lyons, R.E., Vanderkulk, W., “The Use of Triple-Modular
Redundancy to Improve Computer Reliability”, IBM
Journal, April 1962.
Mariotti, K. “A innovative robot motion planning
approach for real-time adaptations in a dynamic
working environment”. MSc. Thesis. InES, ZHAW,
Winterthur Switzerland 2013.
Marti, S. “Ein System zum Monitoring des dynamischen
Arbeitsraums eines Roboterarms”. Project Report.
InES, ZHAW, Winterthur Switzerland 2014.
Unpublished.
Najmaei, N.; Lele, S.; Kermani, M.R.; Sobot, R., "Human
factors for robot safety assessment," Advanced
Intelligent Mechatronics (AIM), 2010 IEEE/ASME
International Conference on , vol., no., pp.539,544, 6-
9 July 2010.
OpenNI http://www.openni.org last accessed 14th March
2014.
OpenCV http://opencv.org/ last accessed 14th March
2014.
OpenGL http://www.opengl.org/ last accessed 14th March
2014.
Pilz http://www.pilz.com/de-CH/company/news/sub/
products/articles/05525 last accessed 14th March
2014.
Schmidhauser, E., Müller, R., Hüppi, R. „JILAS - Jig-Less
Airplane Assembly Montage in Kleinserien durch
Mensch-Roboter-Interaktion“ Internationales Forum
Mechatronik 2012, Proceedings of, ISBN: 978-3-200-
02777-0, Mayrhofen, 21 - 22. November 2012.
Vasic, M.; Billard, A., "Safety issues in human-robot
interactions," Robotics and Automation (ICRA), 2013
IEEE International Conference on, vol., no., pp.197,
204, 6-10 May 2013.
Zanchettin, A. M.; Rocco, P., "Path-consistent safety in
mixed human-robot collaborative manufacturing
environments," Intelligent Robots and Systems (IROS),
2013 IEEE/RSJ International Conference on, vol., no.,
pp.1131,1136, 3-7 Nov. 2013.
RobotWorkspaceMonitoringwithRedundantStructuredLightCameras-APreliminaryInvestigation
617