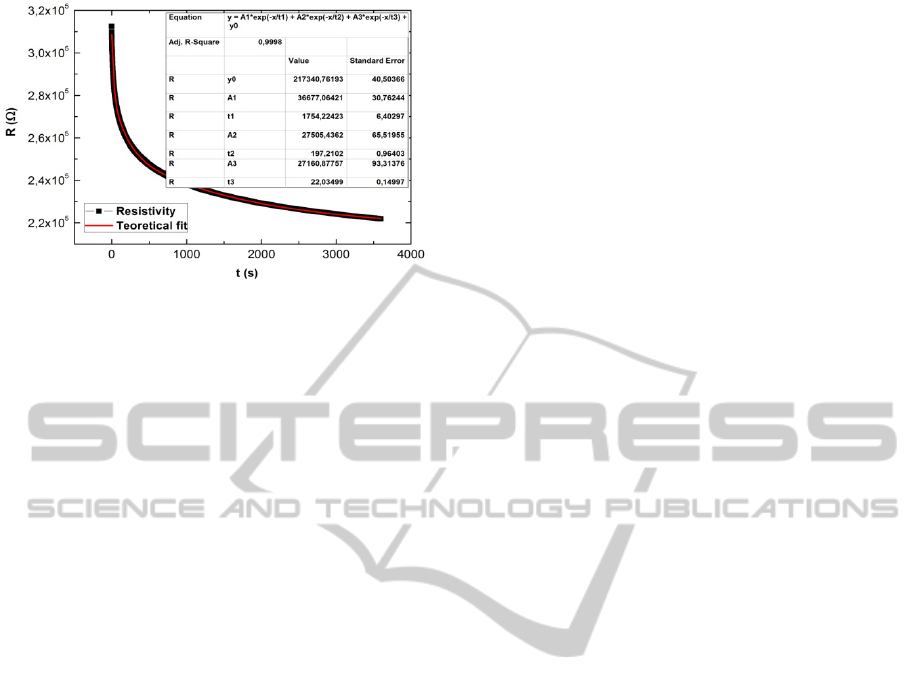
Figure 6: Fitting of experimental curve of change of
resistance in time at constant 6.6 % strain deformation
with equation (2) taking into account three mean
relaxation times:
1
= 1754,
2
= 197, and
3
= 22s.
aggregates have enough time to relax, therefore R
also relaxes with time when the mechanical loading
and the strain sensitivity is the highest. At higher
(>1Hz) frequencies CB aggregates have a difficulty
to follow the macromolecular chains during loading,
so the strain sensitivity decreases versus frequency.
4 CONCLUSIONS
It was shown that the polyisoprene high structure
carbon black composite samples can be used for
periodically changed mechanical load or mechanical
vibration testing. The maximal and minimal values
of resistivity increase with mechanical load
frequency while the piezoresistivity effect decreases.
These can be explained by analysing the
experimentally determined values of relaxation
times of carbon black aggregates and polymer
chains. The limiting factors for use of the developed
sensors at higher mechanical load frequencies are
the rise of maximal and minimal resistivity as well
as the decrease of piezoresistivity versus frequency.
ACKNOWLEDGEMENTS
This study was supported by ESF Grants Nr.
1DP/1.1.1.2.0/13/APIA/VIAA/021.
REFERENCES
Knite, M., Teteris, V., Kiploka, A., Kaupuzs, J.
2004.Polyisoprene-carbon black nanocomposites as
strain and pressure sensor materials, Sensors &
Actuators A: Physical, Volume 110, Issue 1-3, pp.
142-149
Nanni, F., Ruscito, G., Puglia, D., Terenzi, A.,Kenny,
J.M., Gusmano, G.2011.Effect of carbon black
nanoparticle intrinsic properties on the self-
monitoring performance of glass fibre reinforced
composite rods, Composites Science & Technology,
Volume 71, Issue 1, pp. 1-8
Knite, M., Klemenok, I., Shakale, G., Teteris, V., Zicans,
J. 2007.Polyisoprene carbon nano composites for
application in multifunctional sensors. Journal of
Alloys & Compounds, Volume 434-435, pp. 850-853
Sebastian, J., Schehl, N., Bouchard, M.Boehle, M., Li, L.,
Lagounov, A., Lafdi, K. 2014. Health monitoring of
structural composites with embedded carbon nanotube
coated glass fiber sensors. Carbon, Volume 66, pp.
191-200
Canavese, G., Stassi, S.,Fallauto, C.,Corbellini, S., Cauda,
V.,Camarchia, V., Pirola, M.,Pirri, C. F.
2014.Piezoresistive flexible composite for robotic
tactile applications. Sensors & Actuators A: Physical,
Volume 208, pp. 1-9
Wang, L., Cheng, L. 2014. Piezoresistive effect of carbon
nanotube silicone-matrix composite. Carbon, Volume
71, pp. 319-331
Zhou, J.F., Song, Y.H., Zheng, Q., Wu, Q., Zhang
M.Q.2008. Percolation transition and hydrostatic
piezoresistance for carbon black filled
poly(methylvinylsilioxane) vulcanizates. Carbon,
Volume 46, Issue 4, pp. 679-691
Wang, L., Ma, F., Shi, Q., Liu, H., Wang, X. 2011. Study
on compressive resistance creep and recovery of
flexible pressure sensitive material based on carbon
black filled silicone rubber composite. Sensors and
actuators, Volume 165, Issue 2, pp. 207-215
Aldraihem, O., Akl, W., Baz, A. 2009. Nanocomposite
functional paint sensor for vibration and noise
monitoring. Sensors & Actuators A: Physical, Volume
149, Issue 2, p233-240
Jung, J., Kim, M., Choi, J.K., Park, D.W., Shim, S.E.
2013.Piezoresistive effects of copper-filled
polydimethylsiloxane composites near critical
pressure. Polymer, Volume 54, pp. 7071-7079
Zavickis, J., Linarts, A., Knite, M. 2011. The downshift of
the electrical percolation threshold in polyisoprene–
nanostructured carbon composites. Energetika,
Volume 57, Issue 1, pp. 44-49
Zha, J. W., Li, W. K., Zhang, J., Shi, C. Y., Dang, Z. M.
2014. Influence of the second filler on the positive
piezoresistance behavior of carbon nanotubes/silicone
rubber composites. Materials Letters, Volume 118,
Issue 1, pp. 161-164
Stassi, S., Cauda, V., Canacese, G., Pirri, C.F. 2014.
Flexible tactile sensing based on piezoresistive
composites: A review. Sensors, Volume 14, pp.5296-
5332
Wang L., Ding T., Peng Wang P. 2008. Effects of
instantaneous compression pressure on electrical
resistance of carbon black filled silicone rubber
composite during compressive stress relaxation,
Composites Science & Technology, Volume 68,
pp.3448-3450
ICINCO2014-11thInternationalConferenceonInformaticsinControl,AutomationandRobotics
420