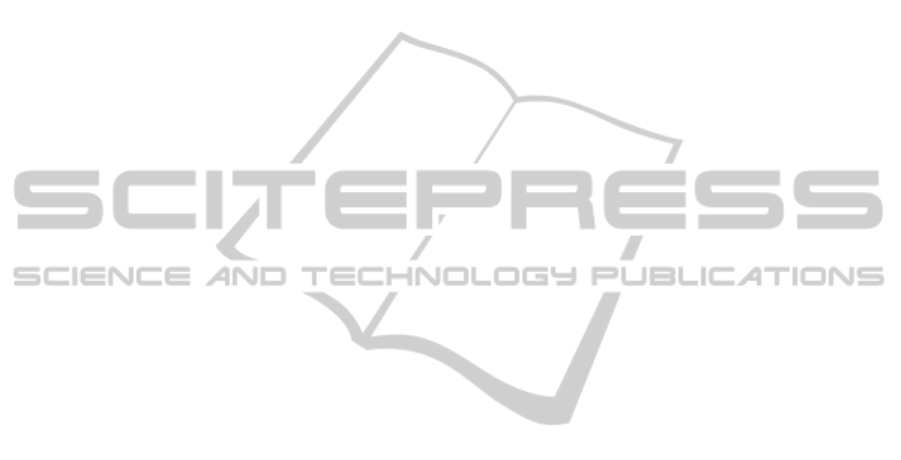
REFERENCES
FLUENT, ver. 14, ANSYS Inc., Southpointe, 275
Technology Drive, Canonsburg, PA 15317, 2012.
Garner, J., Botnvarpan og bunadur hennar, Fiskifelag
Islands, 1967.
Haraldsson, H.O., “Fluid Dynamics Simulation of Fishing
Gear,” M.Sc. Thesis, University of Iceland, May 1996,
ICEM CFD, ver. 14, ANSYS Inc., Southpointe, 275
Technology Drive, Canonsburg, PA 15317, 2012.
Jonsson, E., Leifsson, L., and Koziel, S. “Trawl-Door
Performance Analysis and Design Optimization with
CFD”, 2nd Int. Conf. on Simulation and Modeling
Methodologies, Technologies, and Applications
(SIMULTECH), Rome, Italy, July 28-31, 2012.
Jonsson, E., Hermannsson, E., Juliusson, M., Koziel, S.,
and Leifsson, L. “Computational Fluid Dynamic
Analysis and Shape Optimization of Trawl-Doors,”
51st AIAA Aerospace Sciences Meeting including the
New Horizons Forum and Aerospace Exposition,
Grapevine, Texas, January 7-10, 2013.
Ladson, C.L., “Effects of Independent Variation of Mach
and Reynolds Numbers on the Low-Speed
Aerodunamic Characteristics of the NACA 0012
airfoil Section,” NASA Technical Memorandum 4074,
NASA, 1988.
Leifsson, L., Koziel, S., Hermannsson, E., and Reza
Fakhraie, “Trawl-Door Design Optimization by Local
Surrogate Models,” 55th AIAA/ASMe/ASCE/AHS/SC
Structures, Structural Dynamics, and Materials
Conference, National Harbor, MD, January 2014.
Matlab, ver. R2014a, The Mathworks Inc., Natick,
Massachusetts, U.S.A, 2014.
Rumsey, C. L., Smith, B. R., and Huang, G. P.,
“Description of a Website Resource for Turbulence
Modeling Verification and Validation,” 40th AIAA
Fluid Dynamics Conference and Exhibit, AIAA Paper
2010-4742, Chicago, U.S.A., July 2010.
Tannehill, J.A., Anderson, D.A., and Pletcher, R.H.,
Computational fluid mechanics and heat transfer, 2nd
edition, Taylor & Francis, 1997.
Whicker, L. F., and Fehlner, L. F. “Free-Stream
Characteristics of a Family of Low-Aspect Ratio, All-
Movable Control Surfaces for Application to Ship
Design,” National Technical Information Service, U.S.
Department of Commerce, U.S.A, December 1958.
SIMULTECH2014-4thInternationalConferenceonSimulationandModelingMethodologies,Technologiesand
Applications
784