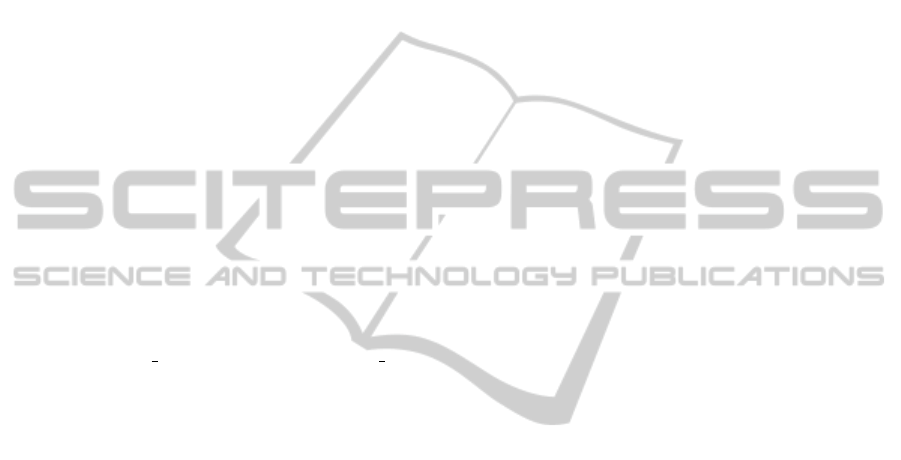
optimal number of the operators working at the line
and the optimal capacity control of the human work-
force are also need to be considered, since their im-
pact on the production planning factors like process-
ing times and WIP are critical.
The implementation of the methods and tech-
niques in a framework (as depicted in Figure 1) would
result in a comprehensive production planning and
capacity management solution that provide reliable
long- and mid-term solutions for companies apply-
ing identical assembly system structures. The core
of the planning system would be the common pro-
duction database that could be fed either by the pro-
duction planners or the MES system. The database
would form the basis for the integrated optimization
models as well as for the self-building mathematical
models that can provide feasible solution for the line
assignment problem and the mid-term capacity and
production planning problems.
ACKNOWLEDGEMENTS
Research has been partially supported by the Hun-
gary, Grants No. ED 13-2-2013-0002 and VKSZ 12-
1-2013-0038.
REFERENCES
Asl, F. M. and Ulsoy, A. G. (2003). Stochastic optimal
capacity management in reconfigurable manufactur-
ing systems. CIRP Annals-Manufacturing Technol-
ogy, 52(1):371–374.
Bousonville, T., Focacci, F., Le Pape, C., Nuijten, W.,
Paulin, F., Puget, J.-F., Robert, A., and Sadeghin, A.
(2005). Integration of rules and optimization in plant
powerops. In Integration of AI and OR Techniques
in Constraint Programming for Combinatorial Opti-
mization Problems, pages 1–15. Springer.
Boysen, N., Fliedner, M., and Scholl, A. (2009a). Pro-
duction planning of mixed-model assembly lines:
overview and extensions. Production Planning and
Control, 20(5):455–471.
Boysen, N., Fliedner, M., and Scholl, A. (2009b). Sequenc-
ing mixed-model assembly lines: Survey, classifica-
tion and model critique. European Journal of Opera-
tional Research, 192(2):349–373.
Ceryan, O. and Koren, Y. (2009). Manufacturing capac-
ity planning strategies. CIRP Annals-Manufacturing
Technology, 58(1):403–406.
Colledani, M. and Tolio, T. (2005). A decomposition
method to support the configuration/reconfiguration
of production systems. CIRP Annals-Manufacturing
Technology, 54(1):441–444.
Deif, A. M. and ElMaraghy, W. (2006). Effect of re-
configuration costs on planning for capacity scalabil-
ity in reconfigurable manufacturing systems. Inter-
national Journal of Flexible Manufacturing Systems,
18(3):225–238.
Giard, V. and Jeunet, J. (2010). Optimal sequencing of
mixed models with sequence-dependent setups and
utility workers on an assembly line. International
Journal of Production Economics, 123(2):290–300.
Gyulai, D., K
´
ad
´
ar, B., Kov
´
acs, A., and Monostori, L.
(2014a). Capacity management for assembly systems
with dedicated and reconfigurable resources. CIRP
Annals - Manufacturing Technology, 63(1):457 – 460.
Gyulai, D., K
´
ad
´
ar, B., and Monostori, L. (2014b). Capac-
ity planning and resource allocation in assembly sys-
tems consisting of dedicated and reconfigurable lines.
In Proceedings of the 8th International Conference on
Digital Enterprise Technology. Fraunhofer IAO.
Gyulai, D. and V
´
en, Z. (2012). Order-stream-oriented sys-
tem design for reconfigurable assembly systems. In
Pannon, U., editor, Proceedings of the Factory Au-
tomation 2012, pages 138–143. University of Pan-
nonia.
Gyulai, D., V
´
en, Z., Pfeiffer, A., V
´
ancza, J., and Monostori,
L. (2012). Matching demand and system structure
in reconfigurable assembly systems. Procedia CIRP,
3:579–584.
Hon, K. and Xu, S. (2007). Impact of product life cycle on
manufacturing systems reconfiguration. CIRP Annals-
Manufacturing Technology, 56(1):455–458.
Iijima, J. (1996). Automatic model building and solving
for optimization problems. Decision Support Systems,
18(3):293–300.
Niroomand, I., Kuzgunkaya, O., and Asil Bulgak, A.
(2012). Impact of reconfiguration characteristics for
capacity investment strategies in manufacturing sys-
tems. International Journal of Production Economics,
139(1):288–301.
Pfeiffer, A., K
´
ad
´
ar, B. G., Popovics, G., Kardos, C., V
´
en,
Z., Kem
´
eny, L., and Monostori, L. (2012). Apply-
ing model-reconstruction by exploring MES and PLC
data for simulation support of production systems. In
Proceedings of the 2012 Winter Simulation Confer-
ence, pages 1–13, Seattle. IEEE.
Popovics, G., Kardos, C., Kem
´
eny, L., Gyulai, D., and
Monostori, L. (2012). Uniform data structure for
production simulation. In Zudor, A. I., Kem
´
eny, Z.,
and Monostori, L., editors, MITIP 2012. 14th Inter-
national Conference on Modern Information Technol-
ogy in the Innovation Processes of the Industrial En-
terprises. Proceedings volume, pages 168–177, Bu-
dapest. MTA SZTAKI.
SIMULTECH2014-DoctoralConsortium
28