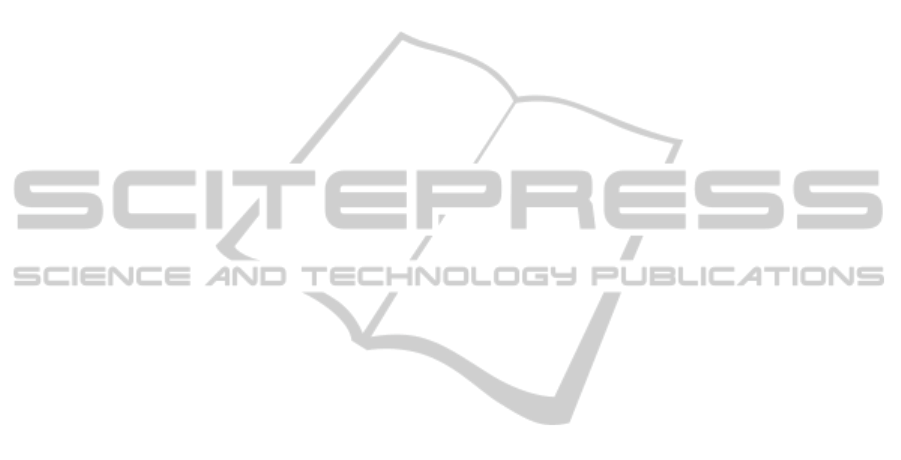
importance in literature. Several initiatives have
been taken by legislative authorities European
Commission (EC), UNEP etc. These initiatives
emphasize on adopting methodologies and tools to
facilitate eco-efficient decision making in
manufacturing system. This would lead to
incorporation of environmental management
strategies in the whole factory more specifically in
the manufacturing planning ensuring better
environmental operational performance on the
factory floor. Sroufe et al. 2002 made a detailed
analysis on scientific literature that establishes
relation between environment management and the
operational performance of the manufacturing
system. Several models have therefore been
investigated linking the environmental emissions
with operations performance and listed in (Sroufe et
al. 2002) thereby highlighting its importance in
evaluating manufacturing performance based on
environmental impact (Figge et al. 2002)
(Schaltegger et al. 2000). The incorporation of this
criterion in decision making is a big challenge for
enterprises particularly the SMEs. Such system is
not yet implemented there possibly due to
development costs (Golinska and Romano, 2012).
However, the cost factor changes when a
manufacturing planning is viewed from the
hierarchical perspective. In (Sroufe et al. 2001), the
researchers have grouped environmental
management related practices at operational, tactical
and strategic levels in a performed case study. This
study shows that the manufacturers are now
emphasizing on adopting environment related
decisions at the operational level. These practices
include scheduling, sequencing and capacity
planning. Apart from introduced methodologies to
evaluate environmental impact in distinct areas of
the manufacturing, numerous tools have been
reported in the literature which uses eco-efficiency
related performance indicators in the manufacturing
planning particularly in the efficiency evaluation of
supply chains. For example, the efficiency of the
supply chain is based on how well the material
requirements planning is made, which is primarily
dependent upon effective tools addressing all the
necessary strategic and the derived operational
objectives and performance indicators of the
company. Melynk et al. 2001 introduced a Green
material requirement tools to incorporate
environmental issues in material requirement
planning. It is one among many preliminary
concepts that targeted minimization of
environmental impacts of waste stream generated in
manufacturing processes. A model based on fuzzy
set theory for the assessment of environmental
hazards in manufacturing is introduced in (Hui et al.
2002). The big issue in such assessment is the
uncertainty of the information used. A case study
was performed (Hui et al. 2002) manifesting the
fuzzy set based approach as a lever to minimize
uncertainty in the information being used for
environment assessment of manufacturing processes.
Manufacturing processes generally consume huge
amount of energy which directly affects the
environment. Therefore, research literature
principally addresses issue of evaluation of energy
performance in manufacturing systems, defining
strategies to reduce energy consumption and the
environmental impact of manufacturing processes.
The environmental impact reduction through energy
performance improvement has been targeted and
several solutions have been proposed. A common
measurement framework for guiding the company
managers and external stakeholders to adopt eco-
efficiency as means for environmental sustainability
has been introduced in (Verfaillie et al. 2000). This
framework provides assessment of environmental
impact during product creation and during service
based on five prominent indicators i.e. energy
consumption, water consumption, material
consumption, Green house gas emissions (GHG) and
Ozone depleting substance emissions (ODS). Hence
this way, the framework provides a flexible
framework that is widely used, broadly accepted and
easily interpreted in the environmental measurement
framework. Therefore, more environmental
sustainability can be ensured once the guidelines
mentioned in this framework are followed. However
the quantification of sustainability needs assessment
methodology that can be practically used widely in
the industry. One of the methodologies for such
quantifications is the Life Cycle Assessment
approach. It is termed as the grouping and
assessment of potential environmental impact of
products and services along the life cycle, enabling
determination of the environmentally aggressive
stages in the product life cycle. Preuss (2005)
emphasized the need for environmental management
system for greening the supply chain. Several
methods were outlined e.g. allowing manufacturers
laying focus on eco-efficiency of the material
acquired from the suppliers, including the criteria of
eco-efficiency in the selection of suppliers,
incorporating better environmental monitoring
procedures based on environmental standards like
ISO 14001 and by establishing environmental
management system in a manufacturing company.
Bojarski et al. 2009 introduced optimization based
KEOD2014-InternationalConferenceonKnowledgeEngineeringandOntologyDevelopment
398