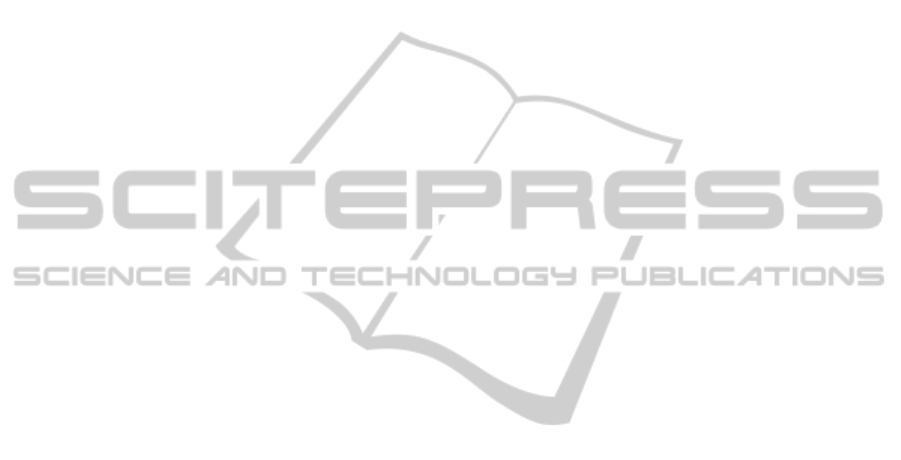
Fawaz, K., Merzouki, R., and Ould-Bouamama, B. (2009).
Model Based Real Time Monitoring for Collision
Detection of an Industrial Robot. Mechatronics,
19(5):695 – 704.
Figueiredo, M., Oliveira, J., Araujo, B., and Pereira, J.
(2006). An Efficient Collision Detection Algorithm
for Point Cloud Models. Technical report.
Garg, D. P. and Kumar, M. (2002). Optimization techniques
applied to multiple manipulators for path planning and
torque minimization. Engineering Applications of Ar-
tificial Intelligence, 15(3-4):241–252.
Gilbert, E. G. (1988). A Fast Procedure for Computing
the Distance Between Objects in Three-Dimensional
Space. Technical report.
Gilbert, E. G. and Foo, C. P. (1990). Computing the
Distance Between General Convex Objects in Three-
Dimensional Space. IEEE Transactions on Robotics
and Automation, 6(1):53–61.
Gosselinj, C. (1994). Robot Path Planning Using Neural
Networks and Fuzzy Logic. (418).
Heidelberger, B. (2004). Detection of Collisions and Self-
collisions Using Image-space Techniques. Journal of
WSCG, 12(3):145–152.
Heidelberger, B., Teschner, M., and Gross, M. (2003). Vol-
umetric Collision Detection for Deformable Objects.
Technical report.
Hermann, A. (2013). GPU-based real-time collision de-
tection for motion execution in mobile manipulation
planning. Advanced Robotics (ICAR), 2013 16th In-
ternational Conference on.
Huang, S.-j. and Lian, R.-j. (1997). A hybrid fuzzy logic
and neural network algorithm for robot motion con-
trol. IEEE Transactions on Industrial Electronics,
44(3):408–417.
Jang, H.-Y. (2006). GPU-based Image-space Approach to
Collision Detection among Closed Objects.
Jang, H.-Y., Jeong, T., and Han, J. (2007). Image-space
Collision Detection Through Alternate Surface Peel-
ing. In Proceedings of the 3rd international confer-
ence on Advances in visual computing - Volume Part I,
ISVC’07, pages 66–75, Berlin, Heidelberg. Springer-
Verlag.
Juan C. Fraile, M. M. and Dodds, G. I. (1999). Optimiza-
tion of Collision Free Trajectories in Multi-Robot Sys-
tems.
Kazem, B. I., Mahdi, A. I., and Oudah, A. T. (2008). Mo-
tion Planning for a Robot Arm by Using Genetic Al-
gorithm. 2(3):131–136.
Kitamura, Y., Tanaka, T., Kishino, F., and Yachida, M.
(1995). 3-D Path Planning in a Dynamic Environ-
ment Using an Octree and an Artificial Potential Field.
Technical report.
Klanke, S., Lebedev, D., Haschke, R., Steil, J., and Ritter,
H. (2006). Dynamic Path Planning for a 7-DOF Robot
Arm. 2006 IEEE/RSJ International Conference on In-
telligent Robots and Systems, (i):3879–3884.
Klein, J. and Zachmann, G. (2004). Point Cloud Collision
Detection. In Cani, M.-P. and Slater, M., editors, Com-
puter Graphics forum (Proc. EUROGRAPHICS), vol-
ume 23, pages 567–576, Grenoble, France.
Kockara, S., Halic, T., K.Iqbal, Bayrak, C., and Rowe, R.
(2007). Collision detection: A survey. Technical re-
port.
LaValle, S. M. (2006). Planning Algorithms. Cambridge
University Press, Cambridge.
Lebedev, D. V., Steil, J. J., and Ritter, H. J. (2005). The
dynamic wave expansion neural network model for
robot motion planning in time-varying environments.
49(0):1–50.
Li, S., Chen, S., Liu, B., Li, Y., and Liang, Y. (2012). De-
centralized kinematic control of a class of collabora-
tive redundant manipulators via recurrent neural net-
works. Neurocomputing, 91:1–10.
Lin, M. C. and Canny, J. F. (1991). A Fast Algorithm for
Incremental Distance Calculation. In In IEEE Interna-
tional Conference on Robotics and Automation, pages
1008–1014.
Lin, M. C. and Manocha, D. (1993). Efficient Contact De-
termination Between Geometric Models. Technical
report, International Journal of Computational Geom-
etry And Applications.
Mirtich, B. V. (1996). Impulse-based Dynamic Simulation
of Rigid Body Systems. PhD thesis. AAI9723116.
Mirtich, B. V. (1998). V-Clip: fast and robust polyhedral
collision detection. ACM Trans. Graph., 17(3):177–
208.
Moore, M. and Wilhelms, J. (1988). Collision Detection
and Response for Computer Animation. In Computer
Graphics, pages 289–298.
Myszkowski, K., Okunev, O. G., and Kunii, T. L. (1995).
Fast Collision Detection Between Complex Solids Us-
ing Rasterizing Graphics Hardware. The Visual Com-
puter, 11(9):497–511.
Pan, J., Chitta, S., and Manocha, D. (2011). Probabilistic
Collision Detection Between Noisy Point Clouds Us-
ing Robust Classification. In International Symposium
on Robotics Research, Flagstaff, Arizona.
Pedrocchi, N., Malosio, M., and Tosatti, L. M. (2009). Safe
Obstacle Avoidance for Industrial Robot Working
Without Fences. In Proceedings of the 2009 IEEE/RSJ
international conference on Intelligent robots and sys-
tems, IROS’09, pages 3435–3440, Piscataway, NJ,
USA. IEEE Press.
Saravanan, R., Ramabalan, S., and Balamurugan, C. (2007).
Evolutionary optimal trajectory planning for indus-
trial robot with payload constraints. The Interna-
tional Journal of Advanced Manufacturing Technol-
ogy, 38(11-12):1213–1226.
Scott, D. S. and Vuillemin, J. (1986). Art Gallery Theorems
and Algorithms.
Stewart, N. T. (2008). An Image-Space Algorithm for
Hardware-based Rendering of Constructive Solid Ge-
ometry - (1).
Stroulia, E., Schneider, D., and Prassler, E. (1997). Pur-
poseful and Reactive Navigation Based on 9 Qualita-
tive Path Planning and Fuzzy Logic.
Tang, L., Dian, S., Gu, G., Zhou, K., Wang, S., and Feng,
X. (2010). A Novel Potential Field Method for Obsta-
cle Avoidance and Path Planning of Mobile Robots.
Technical report.
ICINCO2014-DoctoralConsortium
46