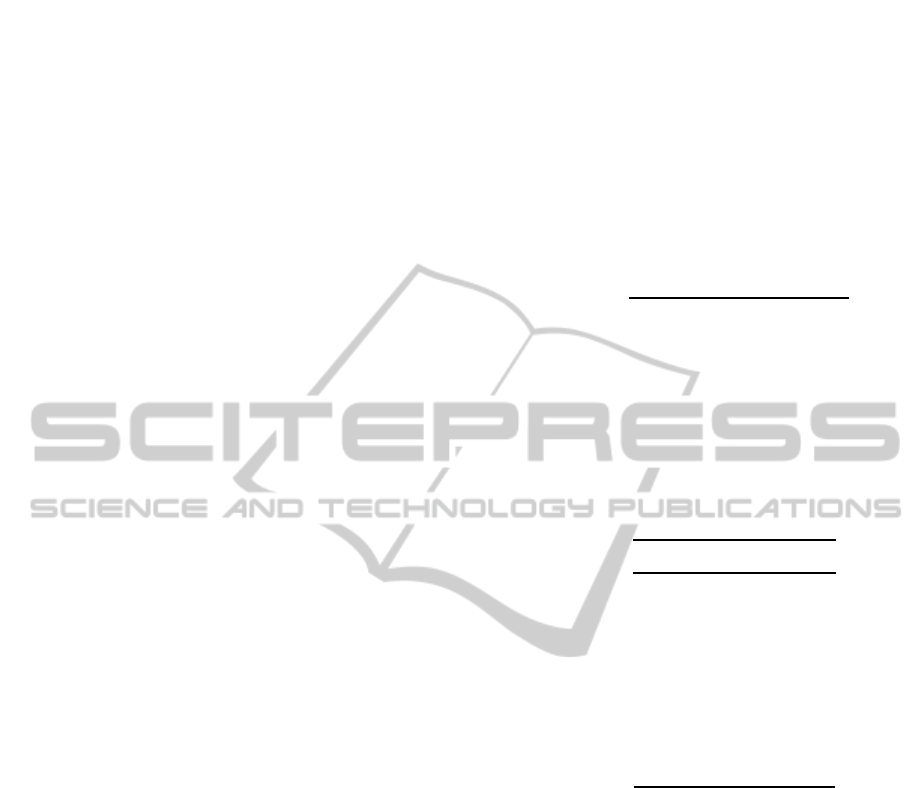
2 OEE & OLE
Overall Equipment Effectiveness (OEE) can be
implemented to benchmark, analyze and improve a
production process by measuring inefficiencies and
groups them in different categories (B. Dal et al.,
2000). The most common inefficiency causes in
industry are those called “six big losses.” These
losses can be categorized in downtime losses, speed
losses, and quality losses. To find a way to monitor
and improve a manufacturing process, six big losses
are addressed as follows.
(1) Downtime losses: Downtime is the most
important loss for equipment effectiveness
improvement since other metrics cannot be
addressed if the manufacturing process is down.
Tooling failures, unplanned maintenance, equipment
breakdowns are some examples of downtime losses.
(2) Setup and Adjustment: This loss is the time
between the last acceptable part produced before
setup to the first consistent acceptable parts
produced after setup and adjustment. This is often a
set of adjustments to machines and/or equipment in
order to produce a product that meets the standard
requirements.Warm up time and changeovers can be
represented as setup and adjustment losses in a
manufacturing process. These losses are considered
in calculation of the availability factor.
(3) Small Stops: These stoppages occur when the
machine stops due to a temporary problem such as
an activated sensor that shuts the machine down
automatically. These minor stoppages are usually
less than 10 minutes and can be dealt with by the
operator and generally there is no need to call a
maintenance team.
(4) Reduced Speed: Knowing the ideal cycle time
of a machine and comparing it with the actual cycle
time, it will be possible to monitor low running or
reduced speed losses. Machines may run at the speed
less than the ideal run rate for various reasons.
Training level of operators, and worn equipment can
be categorized as the aforementioned reasons. Small
stops and reduced speed are known as speed losses
and are taken into account in performance factor
calculation.
(5) Start up Rejects: Startup losses occur in the
initial start of a machine up to the stabilization of its
products quality. A root cause analysis can be done
to pinpoint the potential causes of rejects and to
prevent similar losses from occurring in the future. It
is necessary to note that reworks, scraps and
incorrect assembly, all are considered as rejects in
the production processes.
(6) Production Rejects: This loss occurs in a
steady-state production and is not attributed to start
up. Damage, scraps, and reworks, are some
examples of production reject losses.
The last two losses are considered quality losses
and affect the quality factor of OEE.
The traditional method of OEE calculation
considers availably, performance, and quality
factors as follows:
Availability: Availability is the ratio of actual
production time that a machine is working divided
by the time the machine is planned to work.
A=
Operation time
Planned production time
Performance: Performance of a machine is the
percentage of total number of parts on that machine
to its production rate. In simple words, performance
measures the ratio of actual operating speed of the
equipment and the ideal speed (M. Lesshammar,
1999).
P =
Ideal cycle time
Operation time
Total pieces
Quality: To gain insight into the quality aspect of
a production process the quality portion of OEE is
defined. The Quality metric represents good
(acceptable) units produced by machine divided by
the total units produced by that machine in the
production time.
Q=
Acceptable Pieces
Total Pieces
Given the above, the OEE is normally calculated as
follows:
OEE = A × P × Q
Therefore OEE takes into account the six major
losses. Significant improvement can be achieved
within a short period by eliminating these losses in
industry as a result of enhanced maintenance
activities and equipment management (M. Maran et
al., 2012).
In a situation where a manufacturing line
consists of unbalanced/decoupled machines OEE
alone is not sufficient (Braglia et al., 2009). Also
OEE is measured for an isolated individual
equipment and controlling a single tool does not
seem to be effective (Richard Oechsner et al., 2002).
OLE evaluates the line Efficiency in the production
phase and takes into account of effectiveness (OEE)
FCTA2014-InternationalConferenceonFuzzyComputationTheoryandApplications
200