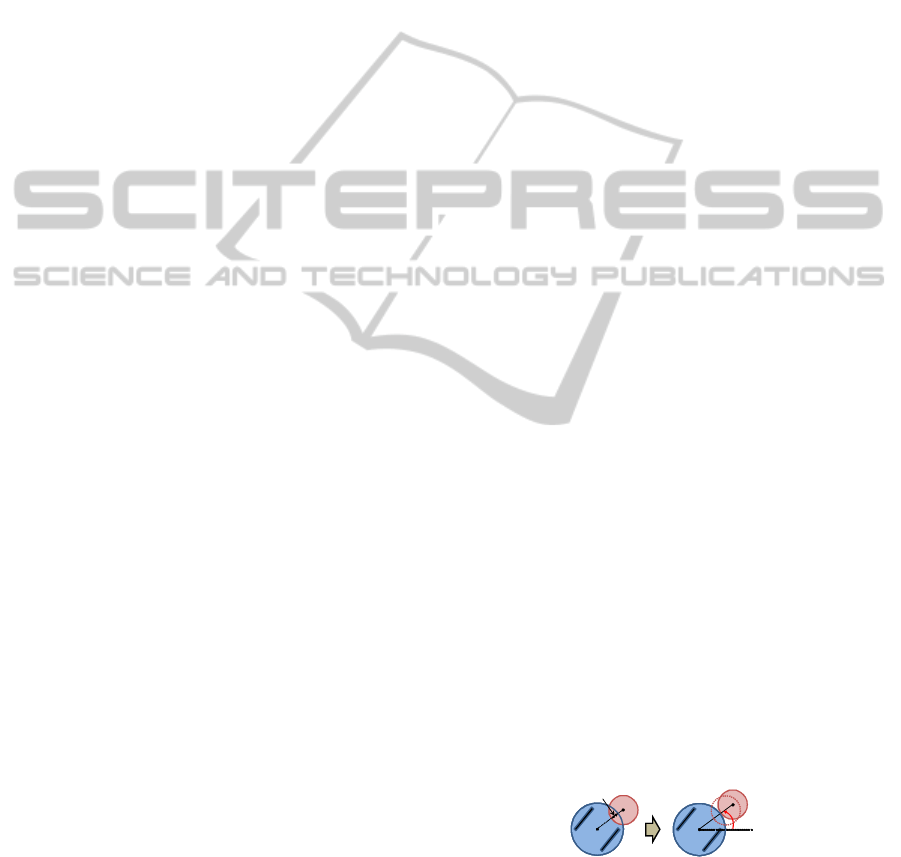
6 CONCLUSIONS
In this paper, we presented a method of generating an
object-pushing manipulation for a two-wheeled robot
based on consideration of effectiveness of re-pushing
and idea of mode switching. The task of pushing ma-
nipulation was divided into two phases; approaching
and pushing, both which DP was applied to. Planning
frameworkunder the consideration of uncertainty was
proposed to find appropriate timing for re-pushing
action decision. Simulation results showed that the
proposed planning framework realized better perfor-
mance in comparison with a re-pushing strategy with
a simple rule. The proposed framework will be fur-
ther improved not only for taking recovery motion but
also expansion to manipulation problem under coop-
eration of multiple mobile robots.
ACKNOWLEDGEMENTS
This research was partly supported by Tateishi Sci-
ence and Technology Foundation and Research Foun-
dation for the Electrotechnology of Chubu.
REFERENCES
Bertsekas, D. (2005). Dynamic Programming and Optimal
Control. Athena Scientific.
Ghosh, A., Chowdhury, A., Konar, A., and Janarthanan, R.
(2012). Multi-robot cooperative box-pushing prob-
lem using multi-objective particle swarm optimization
technique. In Information and Communication Tech-
nologies, pages 272–277.
Kobayashi, Y. and Hosoe, S. (2010). Planning-space shift
motiongeneration : variable-space motion planning
toward flexible extension of body schema. In Journal
of Intelligent and Robotic Systems, volume 62, pages
467–500.
Kondo, T. and Ito, K. (2003). A study on designing con-
troller for peg-pushing robot by using reinforcement
learning with adaptive state recruitment strategy. In
SICE Annual Conference.
Mas, I. and Kitts, C. (2012). Object manipulation using co-
operative mobile multi-robot systems. In Proceedings
of the World Congress on Engineering and Computer
Science.
Morimoto, J. and Doya, K. (2001). Acquisition of stand-
up behavior bya real robot using hierarchical rinforce-
ment learning. In Robotics and Autonomous Systems,
volume 36(1), pages 37–51.
Mukai, T., Hirano, S., H.Nakashima, and Kato, Y. (2010).
Development of a nursing-care assistant robot riba
that can lift a human in its arms. In Intelligent Robots
and Systems.
Nagatani, K., Kiribayashi, S., and Tadokoro, S. (2011). Re-
design of rescue mobile robot quince. In Safety, Secu-
rity, and Rescue Robotics.
Sekiguchi, T., Kobayashi, Y., Shimizu, A., and Kaneko, T.
(2012). Online learning of optimal robot behavior for
object manipulation using mode switching. In Proc.
of IEEE Int. Symposium on Robotic and Sensors En-
vironments, volume 61-66.
Sutton, R. S. and G.Barto, A. (1998). Reinforcement Learn-
ing. MIT Press.
Theodorou, E., Buchli, J., and Schaal., S. (2010). Re-
inforcement learning of motor skills in high dimen-
sions:a path integral approach. In In International
Conference on Robotics and Automa-tion.
Thrun, S., Burgard, W., and Fox, D. (2005). Probabilistic
Robotics. The MIT Press.
Tribelhorn, B., Mudd, C. H., and Dodds, Z. (2007). Eval-
uating the roomba: A low-cost, ubiquitous platform
for robotics research and education. In Robotics and
Automation.
van der Schaft, A. and Schumacher, H. (2000). An intro-
duction to hybrid. In Dynamical Systems.
APPENDIX
Position of the Object at Impact
This section is describes behavior of the object when
the object and the circular robot collides. When the
robot has interfered to the object by distance d, the
object is moved to a position in contact with the robot
on an extended line connecting the centers of the ob-
ject and the robot. The position of the robot is not
changed by the interference. Let the previous position
of the object be denoted by (x
ob
,y
ob
), and the angle
between x-axis and line segment connecting the cen-
ters of the object and the robot be denoted by ψ. Then
position of the object after the collision (x
ob
,y
ob
) is
expressed by the following equation.
x
oa
= x
ob
+ d cosψ (10)
y
oa
= y
ob
+ d sinψ (11)
d
ψ
Figure 12: Position of the object after contact with the
robot.
PlanningofPushingManipulationbyaMobileRobotConsideringCostofRecoveryMotion
327