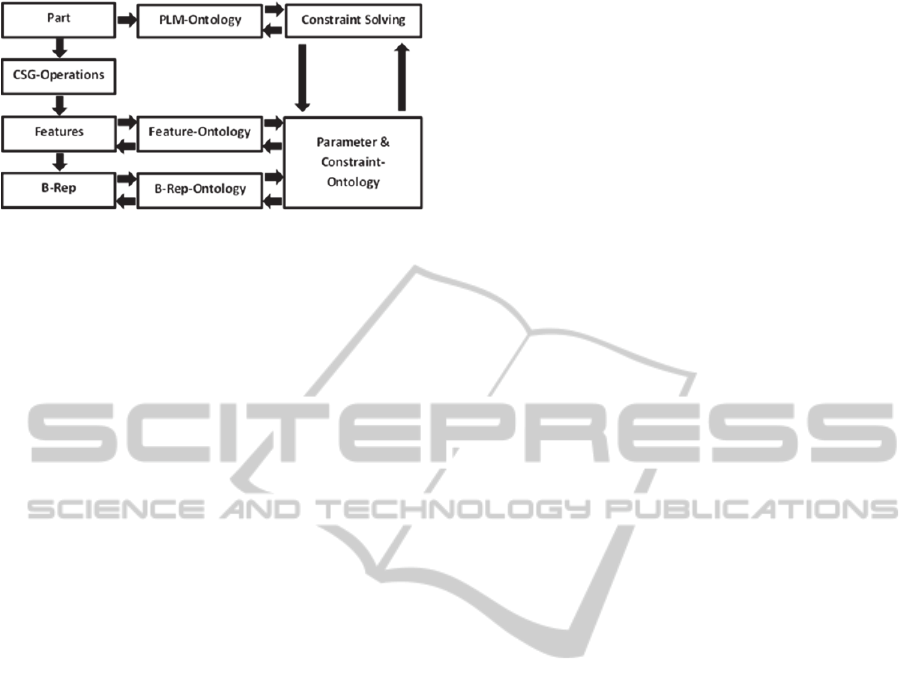
Figure 3: Ontology-based constraint solving for parametric
product data.
5 FUTURE WORKS
Future work is supposed to extend the existing
framework for the control of uncertainty in different
directions:
The uncertainty information model has to
be extended by time dependent properties.
Strategies for an automated A-Box
Ontology generation will be defined.
Existing feature- and B-Rep-Ontologies
will be combined and extended for
parametric modelling.
Existing translation algorithms between
feature-Ontologies and features have to be
analysed.
6 CONCLUSIONS
Parametric modelling is a well-known standard in
CAD-systems. Combining this technology with
ontologies opens up the possibility to reason over
incomplete information and uncertainty information.
We provide an overview of current literature about
semantics in CAD and PLM and deduce challenges
for future research and development. Our concept
for the use of Ontologies in parametric modelling
extends our existing research findings on the field of
uncertainty representation and proposes new
capabilities for the integration of PLM knowledge
into CAD. Future research on the properties of
probabilistic first-order and description logic opens
up possible applications of Ontologies in CAD.
ACKNOWLEDGEMENTS
The authors like to thank the German Research
Foundation DFG for funding this research within the
Collaborative Research Center (SFB) 805 “Control
of Uncertainties in Load-Carrying Structures in
Mechanical Engineering”
REFERENCES
Abdul-Ghafour, S., Ghodous, P., & Shariat, B. (2012).
IEEE IRI. Integration of Product Models by Ontology
Development (pp. 548-555). Las Vegas, Nevada, USA:
IEEE.
Alani, L. I. (2007). Template-basierte Erfassung von
Produktanforderungen in einem CAD System. Berlin:
Technische Universität Berlin.
Altidor, J., Wileden, J., McPherson, J., Grosse, I.,
Krishnamurty, S., Cordeiro, F., et al. (2011). A
Programming language Approach to Parametric CAD
Data Exchange. Proceedings of the ASME 2011
International Design Engineering Technical
Conferences & Computers and Information in
Engineering Conferences, pp. 779-791.
Anderl, R., & Mendgen, R. (1996). Modelling with
constraints: theoretical foundation and application.
Computer-Aided Design (Vol.28 No.3), pp. 155-168.
Anderl, R., Maurer, M., Rollmann, T., & Sprenger, A.
(2013). Representation, Presentation and Visualization
of Uncertainty. CIRP Design 2012 - Sustainable
Product Design -, pp. 257-266.
Andersen, O., & Vasilakis, G. (2007). Building an
Ontology of CAD Model Information. In K.-A. L. G.
Heasle, Geometric Modelling, Numerical Simulation,
and Optimization: Applied Mathematics at SINTEF
(pp. 11-40). Springer.
Dartigues, C., Ghodous, P., Gruninger, M., Pallez, D., &
Sriram, R. (2007). CAD/CAPP Integration using
Feature Ontology. Concurrent Engineering: Research
and Applications, pp. 237-249.
Ding, L.-J. S. (2010). Ontology-based Semantic
Interoperability among Heterogeneous CAD Systems.
Information Technology Journal, pp. 1635-1640.
Engelhardt, R., Koenen, J., Enss, G., Sichau, A., Platz, R.,
Kloberdanz, H., et al. (2010). Proceedings of the 1st
International Conference on Modeling and
Management of Engineering Processes. A Model to
Categorize Uncertainty in Load-Carrying Systems.
Springer.
Franke, M., Klein, P., Schröder, L., & Thoben, K.-D.
(2011). Ontological Semantics of Standards and PLM
Repositories in the Product Development Phase.
Global Product Development, pp. 473-482.
Hughes, T., Cottrell, J., & Bazilevs, Y. (2005, Vol. 194).
Isogeometric analysis: CAD, finite elements, NURBS,
exact geometry and mesh refinement. Computer
Methods in Applied Mechanics and Engineering, pp.
4135-4195.
Kuhn, O., Dusch, T., Ghodous, P., & Collet, P. (2012).
Framework for the support of knowledge-based
engineering template update. Computers in Industry
(Vol. 63), pp. 423-432.
Ontology-basedRepresentationofTimeDependentUncertaintyInformationforParametricProductDataModels
403