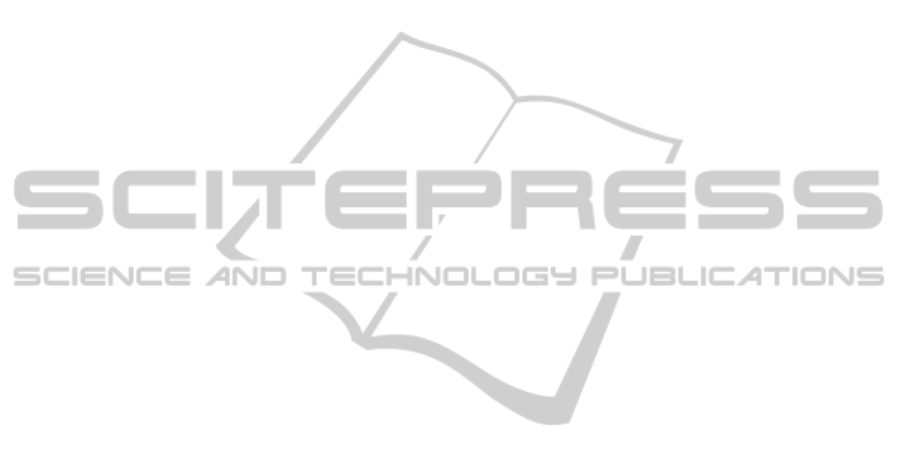
performance comparison online-searching approach
with ep-based approach. In Proceedings of the IEEE
International Conference on Robotics and Automation
(ICRA), volume 2, pages 1811 – 1816 vol.2.
Higashimori, M., Utsumi, K., Omoto, Y., and Kaneko, M.
(2009). Dynamic manipulation inspired by the han-
dling of a pizza peel. IEEE Transactions on Robotics,
25(4):829 –838.
Kim, H. and Park, S. (1995). A strong cutting plane al-
gorithm for the robotic assembly line balancing prob-
lem. International Journal of Production Research,
33(8):2311–2323.
Kopicki, M., Stolkin, R., Zurek, S., Morwald, T., and Wyatt,
J. (2010). Predicting workpiece motions under push-
ing manipulations using the principle of minimum en-
ergy. In Proceedings of the RSS workshop on Repre-
sentations for Object Grasping and Manipulation in
Single and Dual Arm Tasks. submitted.
Kothari, M. and Postlethwaite, I. (2013). A probabilisti-
cally robust path planning algorithm for uavs using
rapidly-exploring random trees. Journal of Intelligent
& Robotic Systems, 71(2):231–253.
Kuwata, Y., Teo, J., Member, S., Fiore, G., Member, S.,
Karaman, S., Member, S., Frazzoli, E., Member, S.,
How, J. P., and Member, S. Realtime motion planning
with applications to autonomous urban driving. IEEE
Transactions on Control Systems, page 2009.
LaValle, S. and Kuffner, J.J., J. (1999). Randomized kin-
odynamic planning. In Proceedings of the IEEE In-
ternational Conference on Robotics and Automation,
volume 1, pages 473–479.
Levitin, G., Rubinovitz, J., and Shnits, B. (2006). A genetic
algorithm for robotic assembly line balancing. Euro-
pean Journal of Operational Research, 168(3):811 –
825.
Lozano-Pérez, T., Jones, J. L., Mazer, E., O’Donnell, P. A.,
Grimson, W. E. L., Tournassoud, P., and Lanusse, A.
(1987). Handey: A robot system that recognizes,
plans, and manipulates. In IEEE International Confer-
ence on Robotics and Automation, pages 843=–849.
Luders, B., Karaman, S., Frazzoli, E., and How, J. (2010).
Bounds on tracking error using closed-loop rapidly-
exploring random trees. In American Control Confer-
ence (ACC), pages 5406–5412.
Lynch, K., Shiroma, N., Arai, H., and Tanie, K. (1998). The
roles of shape and motion in dynamic manipulation:
the butterfly example. In Proceedings of the IEEE In-
ternational Conference on Robotics and Automation,
volume 3, pages 1958 –1963 vol.3.
Lynch, K. M. (1992). The mechanics of fine manipulation
by pushing. In Proceedings of the IEEE International
Conference on Robotics and Automation, pages 2269–
2276.
Lynch, K. M. (1997). Dynamic manipulation with a one
joint robot. In Proceedings of the IEEE International
Conference on Robotics and Automation, pages 356–
366.
Mehrandezh, M., Sela, N., Fenton, R., and Benhabib, B.
(2000). Robotic interception of moving objects using
an augmented ideal proportional navigation guidance
technique. IEEE Transactions on Systems, Man and
Cybernetics, 30(3):238–250.
Michael, J., Chudej, K., Gerdts, M., and Pannek, J. (2013).
Optimal rendezvous path planning to an uncontrolled
tumbling target.
Phoka, T. and Sudsang, A. (2009). Contact point clustering
approach for 5-fingered regrasp planning. In Proceed-
ings of the IEEE/RSJ International Conference on In-
telligent Robots and Systems, pages 4174 –4179.
Rapela, D., Rembold, U., and Kuchen, B. (2002). Planning
of regrasping operations for a dextrous hand in assem-
bly tasks. Journal of Intelligent and Robotic Systems,
33:231–266.
Roa, M. A. and Suarez, R. (2009). Regrasp planning in the
grasp space using independent regions. In Proceed-
ings of the 2009 IEEE/RSJ international conference
on Intelligent robots and systems, IROS’09, pages
1823–1829, Piscataway, NJ, USA. IEEE Press.
Rybus, T. and Seweryn, K. (2013). Trajectory planning
and simulations of the manipulator mounted on a free-
floating satellite. In SÄ
ˇ
Esiadek, J., editor, Aerospace
Robotics, pages 61–73. Springer.
Senoo, T., Namiki, A., and Ishikawa, M. (2008). High-
speed throwing motion based on kinetic chain ap-
proach. In IROS, pages 3206–3211.
Shkolnik, E., Walter, M., and Tedrake, R. (2009).
Reachability-guided sampling for planning under dif-
ferential constraints. In in In Proceedings of the
IEEE/RAS International Conference on Robotics and
Automation (ICRA).
Sintov, A. and Shapiro, A. (2014b). Time-based RRT al-
gorithm for rendezvous planning of two dynamic sys-
tems. In Proceedings of the IEEE International Con-
ference on Robotics and Automation.
Sintov, A. and Shapiro, A. (Submitted July 2014a).
Skip: Semi-stochastic kinodynamic planning algo-
rithm. The IEEE Transactions on Robotics.
Srinivasa, S., Erdmann, M., and Mason, M. (2005). Using
projected dynamics to plan dynamic contact manipu-
lation. In Proceedings of the IEEE/RSJ International
Conference on Intelligent Robots and Systems, pages
3618 – 3623.
Stuheli, M., Caurin, G., Pedro, L., and Siegwart, R. (2013).
Squeezed screw trajectories for smooth regrasping
movements of robot fingers. Journal of the Brazil-
ian Society of Mechanical Sciences and Engineering,
35(2):83–92.
Sudsang, A. and Phoka, T. (2003). Regrasp planning for a 4-
fingered hand manipulating a polygon. In Proceedings
of the IEEE International Conference on Robotics and
Automation, volume 2, pages 2671 – 2676 vol.2.
Tabata, T. and Aiyama, Y. (2001). Tossing manipulation by
1 degree-of-freedom manipulator. In Proceedings of
the IEEE/RSJ International Conference on Intelligent
Robots and Systems, volume 1, pages 132 –137.
Tahara, K., Maruta, K., Kawamura, A., and Yamamoto, M.
(2012). Externally sensorless dynamic regrasping and
manipulation by a triple-fingered robotic hand with
torsional fingertip joints. In Proceedings of the IEEE
International Conference on Robotics and Automation
(ICRA), pages 3252 –3257.
Tournassoud, P., Lozano-Perez, T., and Mazer, E. (1987).
Regrasping. In Proceedings of the IEEE International
IJCCI2014-DoctoralConsortium
24