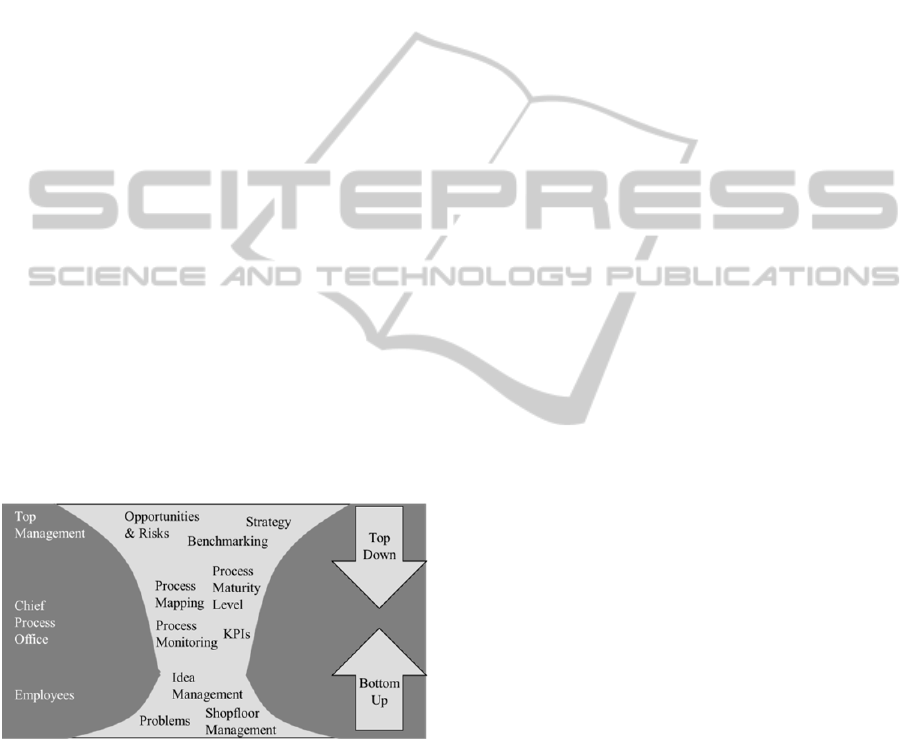
(3) Definition of the process for bottom up input
from employees
(4) Implementation of the quantitative process map
The first step is to set up a central responsibility -
the chief process office (CPO). A chief process
office is a staff unit responsible for the business
process management system. Within the chief
process office the people are responsible to
implement the strategy into processes, to perform
process optimization projects, to evaluate processes
and to take care of the idea management. In addition
the chief process office is offering process
governance in terms of standards for process
management regarding design, measurement and
improvement of processes.
Strategy implementation into processes means to
analyze processes regarding their contribution to
strategy and if necessary improving processes in
order to reach strategic targets.
Process optimization projects are based on
evaluation and strategic as well as bottom up input.
The chief process office offers different optimization
methods regarding intensity of process optimization
and based on maturity level of processes.
Evaluation of processes contains process
monitoring and maturity level assessment.
After the CPO is set up and its tasks are
described, the processes for top down and bottom up
input have to be defined. The combination of top
down and bottom up input as well as CPO tasks are
shown in figure 5.
Figure 5: Process selection.
The chief process office has the task to
implement strategy into processes. Therefor there is
on one hand side some top down input to process
selection from top management to the chief process
office. This input should consider opportunities and
risks as well as general strategic decisions and
information out of benchmarking activities. The
structured approach suggests to define on a yearly
basis the strategic driven change projects as top
down input from top management to the chief
process office.
On the other hand there is information available
from the employees regarding concrete problems in
processes. Those problems or improvement ideas
can be considered for process selection as bottom up
input. The presented approach of this article suggest
to use an idea management driven by the chief
process office to generate and evaluate ideas. It is
also recommended to use a standardized meeting
structure like shopfloor management to identify
problems in daily business.
The chief process office itself generates
knowledge about needed process optimization via
process mapping, process monitoring including KPIs
and the tracking of process maturity levels. Process
maturity levels are only useful in combination with
performance indicators. Otherwise there would be
the risk of over-engineering. Not every process has
to reach highest maturity level. There also might be
processes, which are on highest maturity level but do
not fullfil required performance indicators. In this
case a radical process improvement, for example
using design thinking, is indicated.
The results from top down, bottom up and CPO
process evaluation are used to build up the
quantitative process map. The most important
processes are derived from top management input,
the performance is deduced from bottom up input.
The CPO brings the information together and does
additional evaluations regarding key performance
indicators and process maturity level, taking current
projects and available resource into account. The
CPO sets up the quantitative process map as shown
in figure 6.
The shown process map contains the eleven most
important processes of the company. Within the map
the processes are divided into management, core and
support processes, representing the structure of the
company. The three different sections include end-
to-end processes on the highest level of abstraction.
Those processes where evaluated by importance to
the company and performance. The bigger the boxes
of each process are, the more important the process
is for the company. The color of the boxes implies
the performance of the processes. For example the
core process idea-to-market is the biggest box and is
colored dark. This means it is important but its
performance is low. If a decision for process
improvement has to be taken, processes number 3
and 7 would be the first to be optimized. Based on
the quantitative process map the CPO decides on
processes for optimization.
QuantitativeProcessMaps-AConceptforPrioritizationofBusinessProcessImprovementProjects
445