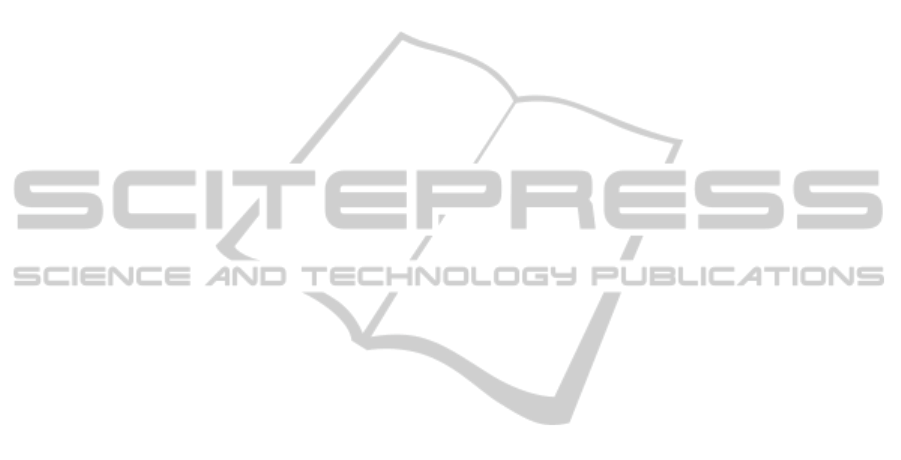
More work has to be developed for answering
some questions that have risen, namely at the room
humidity and temperature level, which reveled some
influence on the on the process but that was not able
to be monitor at the time.
About the tube baking, there is the need to
understand why, in this system, the residues left on
the tube in the first growth are essential and improve
the results in the next sessions and what residues are
those. An approach to “see” inside the tube should
be created in order to evaluate the substances
remaining in the tube after the growths and how they
behave to contribute to reducing the heights
obtained.
The universal protocol proposed in this paper is
only an initial model, which still needs to be
improved by solving the raised questions and by
enhancing the parametric study developed.
ACKNOWLEDGEMENTS
The authors wish to thank FCT – Fundação para a
Ciência e Tecnologia, Portugal, for the financial
support provided under the project PTDC/EEI-
ELC/1838/2012.
The authors would like to acknowledge INESC-
MN for the deposition of catalysts thin-films.
REFERENCES
Atiyah, M. R. et al., 2011. Low Temperature Growth of
Vertically Aligned Carbon Nanotubes via Floating
Catalyst Chemical Vapor Deposition Method. Journal
of Materials Science & Technology, 27(4), pp.296–
300.
Bareket-Keren, L. & Hanein, Y., 2012. Carbon nanotube-
based multi electrode arrays for neuronal interfacing:
progress and prospects. Frontiers in neural circuits,
6(January), p.122.
Brukh, R. & Mitra, S., 2006. Mechanism of carbon
nanotube growth by CVD. Chemical Physics Letters,
424(1-3), pp.126–132.
Calderón-Colón, X. et al., 2009. A carbon nanotube field
emission cathode with high current density and long-
term stability. Nanotechnology, 20(32), p.325707.
Chen, G. D. et al., 2012. Nanoporous micro-element
arrays for particle interception in microfluidic cell
separation. Lab on a chip, 12(17), pp.3159–67.
Chen, R. et al., 2014. Production of hydrogen-rich gas and
multi-walled carbon nanotubes from ethanol
decomposition over molybdenum modified Ni/MgO
catalysts. Journal of Energy Chemistry, 23(2), pp.244–
250.
Fabbro, A., Prato, M. & Ballerini, L., 2013. Carbon
nanotubes in neuroregeneration and repair. Advanced
drug delivery reviews, 65(15), pp.2034–44.
Garcia, E. et al., 2008. Fabrication and multifunctional
properties of a hybrid laminate with aligned carbon
nanotubes grown In Situ. Composites Science and
Technology, 68(9), pp.2034–2041.
Hart, A. J., 2007. Chemical, Mechanical, and Thermal
Control of Substrate-Bound Carbon Nanotube
Growth. Massachussets Institute of Technology.
Holzinger, M., Le Goff, A. & Cosnier, S., 2012. Carbon
nanotube/enzyme biofuel cells. Electrochimica Acta,
82, pp.179–190.
Jacobs, C. B., Peairs, M. J. & Venton, B. J., 2010. Review:
Carbon nanotube based electrochemical sensors for
biomolecules. Analytica chimica acta, 662(2), pp.105–
27.
Jourdain, V. & Bichara, C., 2013. Current understanding
of the growth of carbon nanotubes in catalytic
chemical vapour deposition. Carbon, 58, pp.2–39.
Kumar, M. & Ando, Y., 2010. Chemical Vapor Deposition
of Carbon Nanotubes: A Review on Growth
Mechanism and Mass Production. Journal of
Nanoscience and Nanotechnology, 10(6), pp.3739–
3758.
Newman, P. et al., 2013. Carbon nanotubes: their potential
and pitfalls for bone tissue regeneration and
engineering. Nanomedicine : nanotechnology, biology,
and medicine, 9(8), pp.1139–58.
Oliver, C. R. et al., 2013. Statistical analysis of variation
in laboratory growth of carbon nanotube forests and
recommendations for improved consistency. ACS
nano, 7(4), pp.3565–80.
Qiao-juan, G. et al., 2013. Catalytic growth of multi-wall
carbon nanotubes on carbon cloth using powdery
ferrous sulfate heptahydrate as catalyst precursor. New
Carbon Materials, 28(6), pp.421–427.
Raffa, V. et al., 2011. Carbon Nanotubes for Biomedical
Applications R. Klingeler & R. B. Sim, eds., Berlin,
Heidelberg: Springer Berlin Heidelberg.
Sepúlveda, a T. et al., 2011. Nanocomposite Flexible
Pressure Sensor for Biomedical Applications.
Procedia Engineering, 25, pp.140–143.
Stein, I. Y. & Wardle, B. L., 2013. Coordination number
model to quantify packing morphology of aligned
nanowire arrays. Physical chemistry chemical
physics : PCCP, 15(11), pp.4033–40.
Tran, P. a, Zhang, L. & Webster, T. J., 2009. Carbon
nanofibers and carbon nanotubes in regenerative
medicine. Advanced drug delivery reviews, 61(12),
pp.1097–114.
Wang, Y. et al., 2014. Quantum chemical simulations
reveal acetylene-based growth mechanisms in the
chemical vapor deposition synthesis of carbon
nanotubes. Carbon, 72, pp.22–37.
Wardle, B. L. et al., 2008. Fabrication and
Characterization of Ultrahigh-Volume- Fraction
Aligned Carbon Nanotube-Polymer Composites.
Advanced Materials, 20(14), pp.2707–2714.
BIODEVICES2015-InternationalConferenceonBiomedicalElectronicsandDevices
102