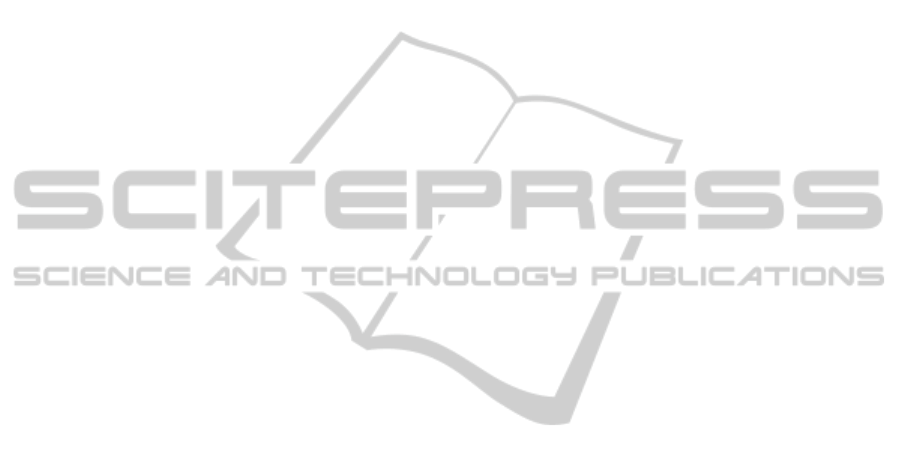
that it is easier to find a feasible solution, or even an
optimal one, when handling terminals operating with
a mixed mode. Moreover, our experiments provide
insight into the number of gates to be changed from
exclusive to mixed in order to guarantee the best per-
formance.
For future research, it may be interesting to inves-
tigate the special case of the problem with p
i
= p.
The complexity of Pm|r
i
,
˜
d
i
, p
i
= p|
∑
w
i
C
i
is open
((Kravchenko and Werner, 2011)) and this problem is
a special case of our problem with p
i
= p : take |I| = 1
with i ∈ I, define
˜
d
i
= r
i
+ p
i
such that s
i
= r
i
and de-
fine for all o ∈ O, r
′
o
= max{r
o
;r
i
+ p
i
} and w
o
= w
io
.
Another interesting problem is an extension in
which trailers are allowed to remain at the gate longer
than strictly needed for loading or unloading. In this
way, the number of direct transfers from inbound to
outbound trailers can be augmented and consequently,
the usage of the storage area can be decreased.
ACKNOWLEDGEMENTS
This research was part of ROCKS project supported
by CNRS/INS2I (Centre National de la Recherche
Scientifique/Institut des Sciences de l’Information et
de leurs Interactions), PICS action n 6421.
REFERENCES
Alpan, G., Ladier, A.-L., Larbi, R., and Penz, B. (2011a).
Heuristic solutions for transshipment problems in a
multiple door cross docking warehouse. Computers
& Industrial Engineering, 61(2):402–408.
Alpan, G., Larbi, R., and Penz, B. (2011b). A bounded dy-
namic programming approach to schedule operations
in a cross docking platform. Computers & Industrial
Engineering, 60(3):385–396.
´
Alvarez P´erez, G., Gonz´alez-Velarde, J., and Fowler, J.
(2009). Crossdocking – Just in time scheduling: an
alternative solution approach. Journal of the Opera-
tional Research Society, 60:554–564.
Apte, U. and Viswanathan, S. (2000). Effective cross dock-
ing for improving distribution efficiencies. Interna-
tional Journal of Logistics: Research and Applica-
tions, 3(3):291–302.
Boysen, N. (2010). Truck scheduling at zero-inventory
cross docking terminals. Computers & Operations Re-
search, 37:32–41.
Boysen, N. and Fliedner, M. (2010). Cross dock scheduling:
Classification, literature review and research agenda.
Omega, 38:413–422.
Boysen, N., Fliedner, M., and Scholl, A. (2010). Scheduling
inbound and outbound trucks at cross docking termi-
nals. OR Spectrum, 32:135–161.
Carlo, H. and Bozer, Y. (2011). Analysis of optimum shape
and door assignment problems in rectangular unit-
load crossdocks. International Journal of Logistics:
Research and Applications, 14(3):149–163.
Chen, F. and Lee, C.-Y. (2009). Minimizing the makespan
in a two-machine cross-docking flow shop problem.
European Journal of Operational Research, 193:59–
72.
Chen, F. and Song, K. (2009). Minimizing makespan
on two-stage hybrid cross docking schedule problem.
Computers & Operations Research, 36:2066–2073.
Christofides, N., Alvarez-Vald´es, R., and Tamarit, J.
(1987). Project scheduling with resource constraints:
A branch-and-bound approach. European Journal of
Operational Research, 29(3):262–273.
Dyer, M. E. and Wolsey, L. A. (1990). Formulating the sin-
gle machine sequencing problem with release dates as
a mixed integer problem. Discrete Applied Mathemat-
ics, 26:255–270.
Joslin, D. E. and Clements, D. P. (1999). Squeaky wheel op-
timization. Journal of Artificial Intelligence Research,
10(1):353–373.
Kravchenko, S. and Werner, F. (2011). Parallel machine
problems with equal processing times: a survey. Jour-
nal of Scheduling, 14(5):435–444.
Laborie, P. and Nuijten, W. (2008). Constrained pro-
gramming formulations and propagation algorithms.
In Artigues, C., Demassey, S., and N´eron, E., edi-
tors, Resource-Constrained Project Scheduling. Con-
trol Systems, Robotics and Manufacturing Series.
ISTE Ltd. Chapter 4.
Lenstra, J., Kan, A. R., and Brucker, P. (1977). Complexity
of machine scheduling problems. Annals of Discrete
Mathematics, 1:343–362.
Li, Y., Lim, A., and Rodrigues, B. (2004). Crossdocking
– JIT scheduling with time windows. Journal of the
Operational Research Society, 55:1342–1351.
Maknoon, M. Y. (2013). Scheduling material handling in
cross-docking terminals. PhD thesis,
´
Ecole polytech-
nique de Montr´eal.
Miao, Z., Lim, A., and Ma, H. (2009). Truck dock assign-
ment problem with operational time constraint within
crossdocks. European Journal of Operational Re-
search, 192:105–115.
van Belle, J., Valckenaers, P., and Cattrysse, D. (2012).
Cross docking: State of the art. Omega, 40(6):827–
846.
Yu, W. and Egbelu, P. (2008). Scheduling of inbound and
outbound trucks in cross docking systems with tem-
porary storage. International Journal of Production
Economics, 184:377–396.
TheTruckSchedulingProblematCrossdockingTerminals-ExclusiveversusMixedMode
253