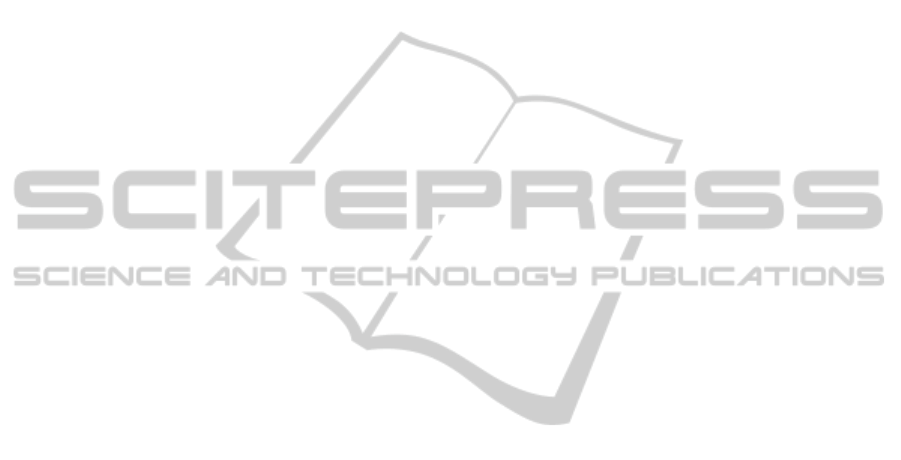
context. Regarding agricultural supply chains (ASC),
authors in (Ahumada and Villalobos, 2009) identified
four main functional areas: production, harvest, stor-
age and distribution. In this work, we want to handle
the production and storage first, leaving distribution
for future work. For ”harvest” models especifically
applied to pork supply chains, see (Rodrguez et al.,
2009), regarding sow farms. In particular, we for-
mulate a linear mixed integer program (MILP) that
addresses decisions at the operative level of the pro-
cessing phase in a meat packing plant. In Section 2,
we outline some background information on the pork
industry through a literature review to frame and mo-
tivate our work. In Section 3 we describe the details
of the problem. Section 4 describes the mixed integer
linear programming formulation that, indicates how
often a cutting pattern is applied and on which type of
carcase, in order to keep a certain level of inventory,
meeting demand requirements and other storage ca-
pacities. Section 5 summarizes the computational re-
sults and finishes with a sensitivity analysis on some
stochastic parameters. Section 6 summarizes the main
conclusions and discusses future work.
2 LITERATURE REVIEW
The planning in a meat packing plant has been stud-
ied by several authors. Although most of the exist-
ing literature targets beef production, these contribu-
tions can also be applied to pork production as we
will show later. To the best of our knowledge, the
first contribution was done by (Whitaker and Cam-
mel, 1990), who presented a linear programming for-
mulation of a partitioned cutting stock problem ap-
plied in a meat industry. The main feature of their for-
mulation is the partitioning of cutting patterns among
carcass sections that vastly reduces the number of cut-
ting patterns in the formulation. However, such model
was devoted to market planning purposes, and con-
sequently lacks elements that support the production
planning, such as inventory and time horizon, among
others.
Years later (Stokes et al., 1998) presents a contri-
bution for a Meat Packing Plant production plan, us-
ing a Mixed Integer Goal Programming formulation
to pursue multiple objectives, however such a model
does not take into account that in a given batch there
may be different types of carcasses, and variations in
some parameters. (Bixby et al., 2006) presents an in-
tegrated system of 45 linear programming models to
schedule operations in a real case for Swift & Com-
pany, a beef meat packing plant. Several thesis dis-
sertations have also been found in the literature. One
of these (Wikborg, 2008) develops online optimiza-
tion techniques for determining which cutting pattern
to use in each carcass according to both carcass at-
tributes and demand. (Reynisdottir, 2012) presents
a linear programming formulation to maximize the
value of pork products. (S
´
anchez, 2011) develops a
DEA study on some parameters and uses a planning
model to determine the levels of pork production by
product. (Sanabria, 2012) develops a planning pro-
duction model for a beef meat packing plant but with-
out including multi-periods.
Unlike the approaches existing in the literature,
the proposed model takes into consideration a plan-
ning horizon, different type of products, raw material
availability, and regards the quality and availability of
carcasses from pigs supplied. Also, our approach con-
siders the perishability issue through the modeling of
a specific variable that manages the freshness of meat,
and more importantly, we realize and consider the ex-
istence of different types of carcasses in a batch of
pigs. On the other hand, biological and economical
parameters in pork production systems are subject to
large variations (like the weight of the animal or its
fat content), but no previous study has assessed the
economic impact of these variations. Hence, our ap-
proach aims to cover some of the gaps found in the
literature related to the animal’s yield and its impor-
tance.
3 PROBLEM DESCRIPTION
The pork supply chain involves several operations for
producing pork and by-products from pigs. Usually
in an integrated structure each chain echelon is spe-
cialized in one or two productive operations. The fat-
tening farms are in charge of producing fattened pigs
ready to be slaughtered. Slaughter and packing op-
erations are usually developed in two facilities: the
Slaughterhouse and the Meat Packing Plant (MPP).
For our formulation lets assume that they are located
close to one another and are both part of a MPP. Every
day, a batch of fattened pigs arrive at the MPP facility
by truck. The truck is unloaded and the pigs are kept
in a pen waiting for the slaughtering time. Slaughter-
ing operations are straightforward; slaughter the en-
tire batch of pigs because inventory of pigs is not pos-
sible. Once the entire batch of pigs is slaughtered,
the carcasses (carcass means body of the slaughtered
animal with the head, limbs, blood and entrails re-
moved) are sent to a freezing storing room where the
carcasses are kept for a period of time in order to de-
crease carcass temperature. The carcasses are pro-
cessed forward to obtain several pork products and
AMixedIntegerLinearProgramforOperationalPlanninginaMeatPackingPlant
255