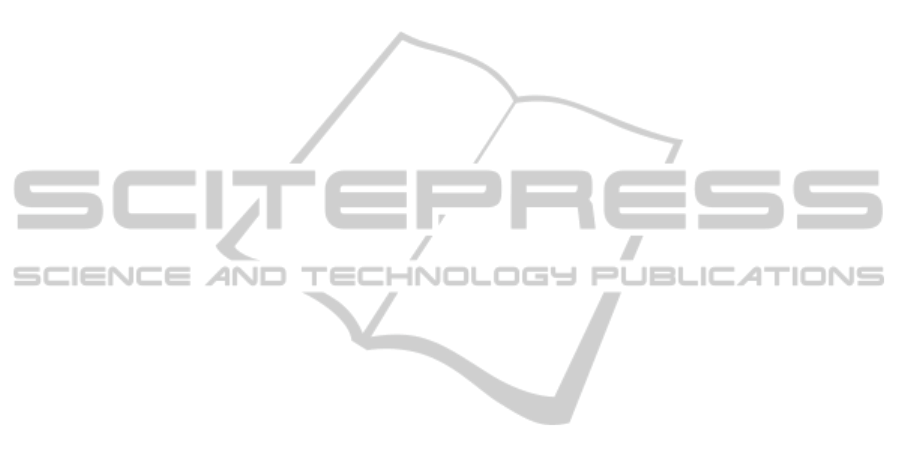
inadequate construction methods, improper planning
and scheduling, mistakes during construction,
inadequate contractor experience and poor site
management and supervision by contractor. The
contractor plays a decisive role in construction
projects and the quality of its performance is crucial
to avoid delays. If the contractor is not committed to
finishing the project on time than its performance
will be poor and delays will occur frequently.
Contractor performance and commitment brings
together all these causes of delay into one unique
factor and it is easy to understand the correlation
between them.
The second factor (lack of productivity) groups 5
causes of delays related with materials, labour and
equipment: shortages in materials, delay in materials
delivery, low labour productivity, equipment
unavailability and failure and inadequate equipment.
Unavailability of equipment or inadequate
equipment can significantly decrease labour
productivity and it is a clear sign of improper
planning and poor site management. In addition,
shortage in material, which can be a consequence of
delays in materials delivery or improper planning,
also leads to a decrease in labour productivity. Low
labour productivity combined with work stoppages
due to shortages of materials or equipment failure
can also be considered a major reason for
construction delays.
The third factor (poor control) links 4 causes of
delay, all of them related to poor control by the
consultant: inflexibility of consultant, delay in
approval of drawings, delay in quality control and
waiting time for approval of tests and inspections.
Consultants also play an important role in
construction projects and rigidity and inflexibility on
their part can cause significant delays in work
progress. Consultants have to ensure the quality of
the contractor’s performance and have the power to
stop the work progress to perform tests and
inspections. Therefore, if a consultant takes too long
on this process or is inflexible on its demands,
delays can occur and work schedules can be
compromised.
The fourth factor (lack of commitment)
associates 4 causes of delay related with various
categories: lack of control over subcontractor,
inadequate quality of materials, change in materials’
prices and lack of motivation for contractor to finish
early. Although these causes of delays may seem
unrelated, their correlation relies mostly on the
subcontractor’s commitment. Lack of motivation on
the part of the contractor means that it is sloppier in
the process of choosing and controlling the
subcontractors, making it harder for the consultants
to control and monitor all of them. Because of this,
subcontractors feel free to lower the quality of
materials and change their prices in order to increase
their profits.
The fifth factor (lack of communication) groups
together 3 causes of delays related with the contract
and contractual relationships: unrealistic time
schedule and specifications in contract, lack of
communication between parties and disputes and
negotiations between parties. In order to be
competitive, contractors reduce time schedules
beyond reasonable terms and then are unable to meet
their initial proposal. This issue immediately
originates time overruns and frequently leads to
disputes between parties that slow down or stop
work progress. In addition to this, lack of
communication between all parties involved also
leads to disputes and negotiations.
The sixth factor (interference of the developer)
links 3 developer-related causes of delays: slow
decision making by the developer, developer
interference and change orders. Along with the
contractor and the consultant, the developer plays a
major role in construction projects. All these causes
of delay are related to developer interference in the
process, so the correlation between them makes
sense. Slow decision making and interference can
slow down or even stop the work progress and
generate delays. Change orders by the developer
also lead to scheduling modifications that can delay
the completion of a project.
The seventh factor (financial constraints)
associates 3 causes of delays related with financial
issues: delay in progress payments by developer,
financial constraints on the contractor and the
bidding and award of contract process. These causes
of delays are directly related with the financial
problems faced by both the developer and
contractor. Delays in progress payments by the
developer force the contractor to use their own
financial resources to supply the project activities,
otherwise the work will be halted. The type of
bidding and award of contract process is also
associated with these causes due to its financial
nature. Developers frequently choose the lowest
bidder in awarding their contracts. In order to be
more competitive and offer lower prices, contractors
reduce their profit margins and become more
vulnerable to payment delays.
The eighth factor (excess of and changes in
bureaucracy) contain 2 causes of delays related with
bureaucracy: bureaucracy in the developer’s
organization and changes in government regulations.
CausesofDelaysinPortugueseConstructionProjects
121