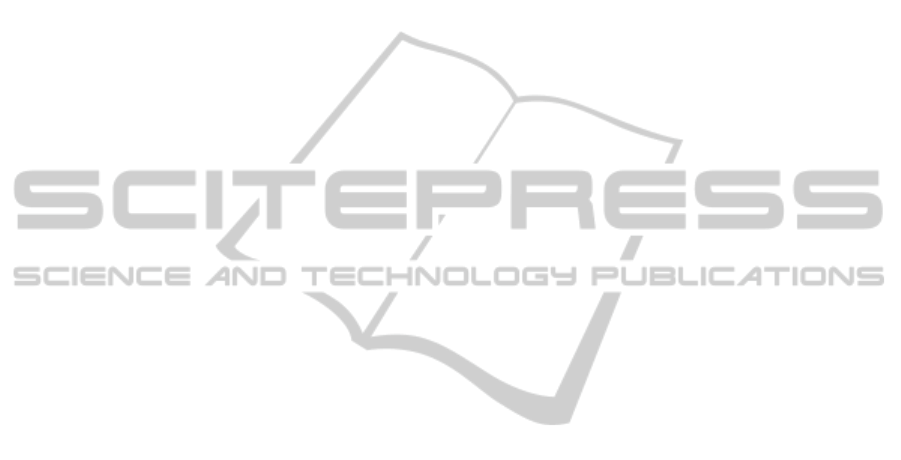
40 percent of costs and even 70 percent of production
time. During an assembly single machine parts are
joined to first-order assemblies (pre-assembly), then
to assemblies of higher order (intermediate assem-
bly) and finally to an end product (final assembly).
The German VDI guideline 2860 (German Engineers’
Association, 1990) further differentiates between pri-
mary assembly, which includes the main joining oper-
ations as defined with the DIN 8580 (DIN Deutsches
Institut f
¨
ur Normung e.V., 2003), and secondary as-
sembly, including all additional assembly activities
like handling, adjustment and control of parts, mate-
rial, tools, and machines. Assembly operations such
as joining directly refer to physical activities of the
worker. A more detailed description of the manual
operations as well as of the physical work environ-
ment can , for example, be found in (Aehnelt et al.,
2014).
Traditionally, a worker is equipped with work or-
ders describing the work to be done on an abstract
level. It strongly depends on his individual knowl-
edge and experiences to interpret the given informa-
tion correctly. Information assistance, especially in
complex and continuously changing assembly work
processes, improves the quality of work by ensuring
an immediate transfer of required work information
to the workplace and back to planning systems for ex-
ample. Here, we differentiate between five general
types of information assistance:
• Raising awareness: The worker requires up-to-
the-minute knowledge about his direct and rele-
vant work environment in order to align his own
activities accordingly. Knowing early enough the
malfunction or breakdown of a machine, which
produces parts for his own assembly, influences
his situational decisions and activities. Thus, in-
formation assistance needs to make the worker
aware of relevant states, events and occurrences
within the work environment which have an in-
fluence on the planning and execution of the
worker’s tasks.
• Guiding: The worker requires orientation with re-
spect to his current and upcoming assembly tasks.
This needs to be given through operational guid-
ance which filters available information for each
specific work step, in order to reduce the parallel
information load to a required minimum. Know-
ing the exact joining procedure beforehand does
not reduce the risk of failures, especially in com-
plex assembly cases. Thus, information assistance
needs to split complex procedures into smaller
but easier understandable parts, used to guide the
worker step-by-step through the assembly.
• Monitoring: In the first place, monitoring the as-
sembly process has a practical value. It allows a
detailed comparison as well as re-calculation of
planned and real time figures. Additionally, it en-
ables the early identification of quality issues or
interruptions. Information assistance needs to col-
lect required data from the workplace which sup-
ports the continuously production re-planning. It
also needs to control the correct execution of as-
sembly procedures to avoid reworking in case of
wrong assembly orders, skipped parts or incorrect
tool usage.
• Documenting: When it comes to quality issues or
even complaints, information assistance needs to
support tracking back these issues to their roots,
which requires a parallel documentation of assem-
bly tasks. However, this kind of documentation
can also be helpful to evaluate assembly proce-
dures finding examples of best practice or expert
knowledge inherited within individual work pro-
cesses.
• Guarding: The physical and cognitive loads at the
assembly workplace vary from situation to situ-
ation. Information assistance needs to guard the
worker from overload by balancing the load lev-
els within healthy borders or by visualising it.
Based on the use cases introduced above, we dis-
cuss the current state of the art in assistance for man-
ual assembly tasks. Smart assistance is no novelty
in manufacturing. However, we find there a major-
ity of specialised and single task solutions focussing
on quality assurance and information transfer (Berndt
and Sauer, 2012). Other research deals with con-
cepts for smart factories which automate the plan-
ning and execution of manufacturing processes in au-
tonomously working factories. Focussing on the au-
tomation of robot cells Mayer et al. proposed the
usage of intelligent systems to resemble human de-
cision making and problem solving for complex as-
sembly tasks (Mayer et al., 2011). They introduce
the cognitive control unit (CCU) which ensures the
numerical planning of robot behaviour backed by a
cognitive architecture. Cognitive architectures can be
understood as a mean to implement intelligent and au-
tonomous behaviour in assistance applications. They
have proven capable of supporting complex problem
solving tasks. A recent example is the simulation of
mission management for unmanned aircrafts (Gunetti
et al., 2013).
Our own work contributes to the growing demand
of information assistance for manual work operations
in manufacturing which underlies human flexibility
and failures as motivated by (Bader and Aehnelt,
2014). In particular, we focus on assistance that can
be generated automatically from existing knowledge
ICAART2015-InternationalConferenceonAgentsandArtificialIntelligence
144