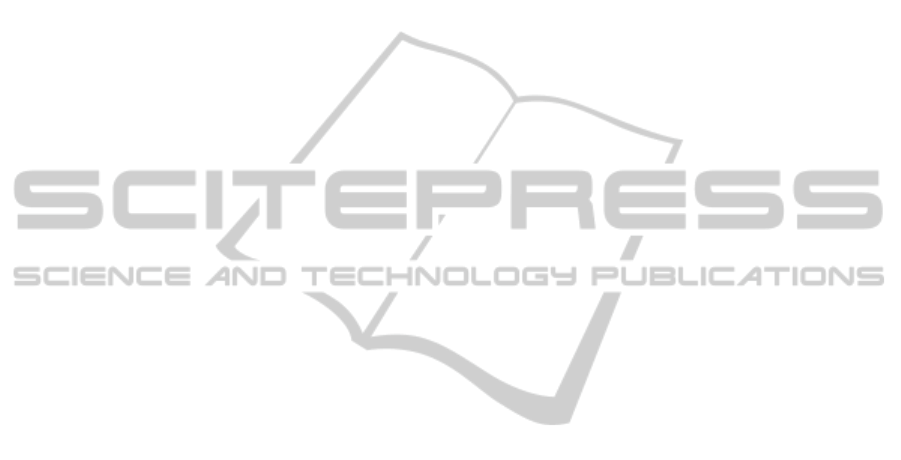
H.-J. Kim, D.-H. Lee, and P. Xirouchakis, “Disassembly
scheduling: literature review and future research
directions,” International Journal of Production
Research, vol. 45, no. 18–19, pp. 4465–4484, 2007.
K. N. Taleb and S. M. Gupta, “Disassembly of multiple
product structures,” Computers & Industrial
Engineering, vol. 32, no. 4, pp. 949–961, Sep. 1997.
K. Inderfurth and I. M. Langella, “Heuristics for solving
disassemble-to-order problems with stochastic yields,”
OR Spectrum, vol. 28, no. 1, pp. 73–99, Jan. 2006.
D.-H. Lee, P. Xirouchakis, and R. Zust, “Disassembly
Scheduling with Capacity Constraints,” CIRP Annals -
Manufacturing Technology, vol. 51, no. 1, pp. 387–
390, 2002.
D.-H. Lee and P. Xirouchakis, “A two-stage heuristic for
disassembly scheduling with assembly product
structure,” J Oper Res Soc, vol. 55, no. 3, pp. 287–
297, 2004.
H.-J. Kim, D.-H. Lee, P. Xirouchakis, and R. Züst,
“Disassembly Scheduling with Multiple Product
Types,” CIRP Annals - Manufacturing Technology,
vol. 52, no. 1, pp. 403–406, 2003.
H.-J. Kim, D.-H. Lee, and P. Xirouchakis, “Two-phase
heuristic for disassembly scheduling with multiple
product types and parts commonality,” International
Journal of Production Research, vol. 44, no. 1, pp.
195–212, 2006.
H.-J. Kim, D.-H. Lee, and P. Xirouchakis, “Two-phase
heuristic for disassembly scheduling with multiple
product types and parts commonality,” International
Journal of Production Research, vol. 44, no. 1, pp.
195–212, 2006.
Y. Barba-Gutiérrez, B. Adenso-Díaz, and S. M. Gupta,
“Lot sizing in reverse MRP for scheduling
disassembly,” International Journal of Production
Economics, vol. 111, no. 2, pp. 741–751, Feb. 2008.
H.-J. Kim and P. Xirouchakis, “Capacitated disassembly
scheduling with random demand,” International
Journal of Production Research, vol. 48, no. 23, pp.
7177–7194, 2010.
B. Adenso-Diaz, S. Carbajal, and S. Lozano,
“Disassembly scheduling of complex products using
parallel heuristic approaches,” in 2010 IEEE/ACS
International Conference on Computer Systems and
Applications (AICCSA), 2010, pp. 1–4.
X. Liu, C. Wang, F. Chu, and C. Chu, “A forward
algorithm for capacitated lot sizing problem with lost
sales,” in Fifth World Congress on Intelligent Control
and Automation, 2004. WCICA 2004, 2004, vol. 4,
pp. 3192–3196 Vol.4.
N. Absi, B. Detienne, and S. Dauzère-Pérès, “Heuristics
for the multi-item capacitated lot-sizing problem with
lost sales,” Computers & Operations Research, vol.
40, no. 1, pp. 264–272, Jan. 2013.
J. Rezaei and M. Davoodi, “Multi-objective models for
lot-sizing with supplier selection,” International
Journal of Production Economics, vol. 130, no. 1, pp.
77–86, Mar. 2011.
D.-H. Kim and D.-H. Lee, “A heuristic for multi-period
disassembly leveling and scheduling,” in 2011
IEEE/SICE International Symposium on System
Integration (SII), 2011, pp. 762–767.
A. Aydemir-Karadag and O. Turkbey, “Multi-objective
optimization of stochastic disassembly line balancing
with station paralleling,” Computers & Industrial
Engineering, vol. 65, no. 3, pp. 413–425, Jul. 2013.
M. Schoenauer, K. Deb, G. Rudolph, X. Yao, E. Lutton, J.
J. Merelo, and H.-P. Schwefel, Eds., Parallel Problem
Solving from Nature PPSN VI, vol. 1917. Berlin,
Heidelberg: Springer Berlin Heidelberg, 2000.
M. Godichaud, Amodeo L., Multi-objective Optimization
of Supply Chains with Returns, International
Conference on Metaheuristics and Nature Inspired
Computing, META 2012, Sousse, Tunisia, 27-31
October 2012.
D. Sánchez, L. Amodeo, and C. Prins, “Meta-heuristic
Approaches for Multi-objective Simulation-based
Optimization in Supply Chain Inventory
Management,” in Artificial Intelligence Techniques
for Networked Manufacturing Enterprises
Management, L. Benyoucef and B. Grabot, Eds.
Springer London, 2010, pp. 249–269.
Li X., Yalaoui F., Amodeo L., Chehade H., Metaheuristics
and exact methods to solve a multiobjective parallel
machines scheduling problem, Special Issue on
Advanced Metaheuristics For Integrated Supply Chain
Management, Journal of Intelligent Manufacturing
(ISI), Vol 23, pp 1179-194, 2012.
ICORES2015-InternationalConferenceonOperationsResearchandEnterpriseSystems
178