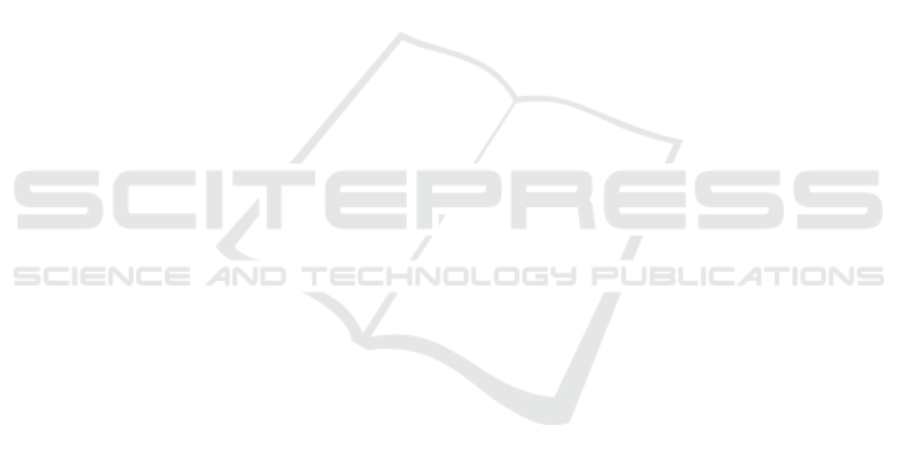
Data Mining Analysis of Turn around Time Variation
in a Semiconductor Manufacturing Line
Il-Gyo Chong
1
, Chenbo Zhu
2
and Yanfeng Wu
3
1
Semiconductor R&D Center, Samsung Electronics, 1 Samsungjeonja-ro, Hwaseong-si 445-330, Republic of Korea
2
College of Economics and Management, Zhejiang University of Technology, 288 Liuhe Road, Hangzhou, China
3
School of management, Fudan University, 670 Guoshun Road, Shanghai, China
Keywords: Semiconductor Manufacturing Line, Turn around Time (TAT), Data Mining, Variable Selection, Variable
Importance in the Projection (VIP) Scores, Partial Least Squares Regression.
Abstract: Variation reduction of Turn Around Time (TAT) in a manufacturing line is one of the important issues for
line optimization. In a manufacturing line with many sequential process steps such as semiconductor
fabrication, it is not easy to find the root causes of the TAT variation because (1) there might be a big time
gap (more than 30 days) between cause and effect, and (2) there are so many machines (or tools) related
with a process. The purpose of this paper is to propose a data mining based method to identify the root cause
of TAT variation. We also aim to validate the performance of the proposed method through a simulation
study.
1 INTRODUCTION
We consider a Turn Around Time (TAT) reduction
problem of a manufacturing line that consists of
many sequential process steps such as
semiconductor fabrication. Due to long time gap
(more than 30 days) between cause and effect, it is
difficult to make a timely solution. When engineers
make a solution of the cause, the cause is not a
current problem. Thus, in the field, a mostly used
strategy for reducing TAT focuses on solving
current problems of each machine under one’s own
supervision. However this strategy requires many
human resources and does not provide priority of the
causes because engineers do not know how much
the cause will make an effect on the TAT.
Furthermore, if there are many machines (or tools)
in a manufacturing line, the problem becomes more
difficult to assign the resource to solve the problem.
Specially, when investing for buying new machines,
identifying the true causes is very important because
the cost of a machine is recently very expensive in a
high technology industry.
The objective of this paper is to propose a data
mining based method which identifies the root cause
of TAT variation. Firstly, we build a relation model
between time variables of each process step (e.g.,
tool processing, waiting time, etc.) and the TAT by
using Partial Least Squares Regression (PLSR).
Secondly, we calculate the VIP scores of importance
of the time variables by applying the Variable
Importance in the Projection (VIP) method to the
PLSR model. We apply the proposed method to two
simulation experiments which mimic the real
situation. The result shows good performance. More
exhaustive simulation study is underway.
The rest of the paper is organized as follows. A
brief description of PLSR, the VIP method for
selecting important variables, and the concept of the
proposed method is given in Section 2. Section 3
describes the simulation design and experiment
factors. Simulation results of two different cases are
given in Section 4. Finally, Section 5 concludes the
current work with a summary.
2 PROPOSED METHOD
2.1 VIP Method based on PLSR
2.1.1 Partial Least Squares Regression
In case of single response y and p variables, PLS
regression model with h (hp) latent variables can
185
Chong I., Zhu C. and Wu Y..
Data Mining Analysis of Turn around Time Variation in a Semiconductor Manufacturing Line.
DOI: 10.5220/0005253301850189
In Proceedings of the International Conference on Operations Research and Enterprise Systems (ICORES-2015), pages 185-189
ISBN: 978-989-758-075-8
Copyright
c
2015 SCITEPRESS (Science and Technology Publications, Lda.)