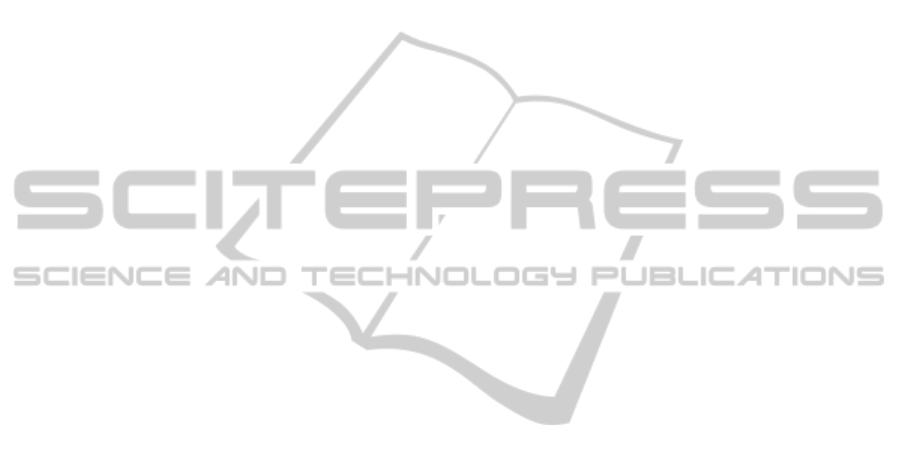
We have proposed a simplified representation of
the dependency graph by eliminating sketch nodes
that do not add value to the overall visualization and
only showing the multilevel dependencies
(grandparent-child) that are explicitly defined by
geometric and dimensional constraints. The result is
a clearer and more intuitive representation of the
internal structure of the parametric model. While the
system need to be tested on a large, "real-world"
example with a more extensive group of models, in
many cases the number of nodes can be reduced by
at least half, which contributes to a more effective
visualization.
Although the algorithm presented in this paper
was implemented as an add-in for the CAD package
SolidWorks, further developments are planned for
the near future. At the present time, the software
prototype can extract model information and export
it to a graph structure (which is visualized by an
external application), but a complete interactive
solution that is fully integrated within the CAD
environment would be beneficial. In addition, the
simplified model representation can be analyzed,
restructured, and optimized by applying clustering
and partitioning algorithms, which have the potential
to make models more flexible and reusable.
Furthermore, comparative studies of the graph
structures can be performed and assessed using
complexity metrics.
ACKNOWLEDGEMENTS
The Spanish Ministry of Economy and
Competitiveness and the FEDER Funds, through the
ANNOTA project (Ref. TIN2013-46036-C3-1-R)
supported this work.
REFERENCES
Baxter, D, Gao, J, Case, K., Harding, J, Young, B,
Cochrane, S & Dani, S, 2007. An engineering design
knowledge reuse methodology using process
modelling. Research in engineering design, vol. 18,
no. 1, pp. 37-48.
Bhaskara, S, 2011. Analysis and Visualization of Complex
Computer Aided Design Models as a Design Structure
Matrix. Proceedings of the 13th International DSM
Conference. Cambridge, MA, USA.
Bodein, Y, Rose, B & Caillaud, E, 2014. Explicit
Reference Modeling Methodology in Parametric CAD
System. Computers in Industry, vol. 65, no. 1, pp.
136-147.
Bondy, JA & Murty, USR, 1976. Graph theory with
applications. Vol. 6. Macmillan, London.
Deo, N, 2004. Graph theory with applications to
engineering and computer science, PHI Learning.
New Delphi.
Eppinger SD, 1991. Model-based approaches to managing
concurrent engineering. Journal of Engineering
Design, vol. 2, pp. 283–290.
Franciosa, P, Patalano, S & Riviere, A, 2010. 3D tolerance
specification: an approach for the analysis of the
global consistency based on graphs. International
Journal on Interactive Design and Manufacturing,
vol. 4, no. 1, pp. 1-10.
Hanratty, PJ, 1995. Parametric/relational solid modelling.
In D.E. LaCourse (Ed.), Handbook of solid modeling,
pp. 8.1-8.25. New York: McGraw-Hill.
Hartman, NW, 2005. Defining Expertise in the Use of
Constraint-Based CAD Tools by Examining Practicing
Professionals. Engineering Design Graphics Journal,
vol. 69, no. 1, pp. 6-15.
Karniel, A, Belsky, Y & Reich, Y, 2005. Decomposing the
problem of constrained surface fitting in reverse
engineering. Computer-Aided Design, vol. 37, no. 4,
pp. 399-417.
Lai, X & Gershenson, JK, 2008. Representation of
similarity and dependency for assembly modularity.
International Journal of Advanced Manufacturing
Technology, vol. 37, no. 7-8, pp. 803-827.
Marchenko, M, Behrens, BA, Wrobel, G, Scheffler, R &
Pleßow, M, 2011. A New Method of Visualization and
Documentation of Parametric Information of 3D CAD
Models. Computer-Aided Design and Applications,
vol. 8, no. 3, pp. 435-448.
Michael, DK & Battiston, S, 2009. From Graph Theory to
Models of Economic Networks. A Tutorial. Networks,
Topology and Dynamics, pp. 23-63. Springer Berlin
Heidelberg.
Mohammed, J, May, J & Alavi, A, 2008. Application of
Computer Aided Design (CAD) In Knowledge Based
Engineering. Proceedings of The 2008 IAJC-IJME
International Conference. Nashville, TN, USA.
Myung, S & Han, S, 2001. Knowledge-based parametric
design of mechanical products based on configuration
design method. Expert Systems with Applications, vol.
21, Elsevier Science Ltd., pp. 99-107.
Owensby, JE & Summers, JD, 2014. Assembly Time
Estimation: Assembly Mate Based Structural
Complexity Metric Predictive Modeling. Journal of
Computing and Information Science in Engineering,
vol. 14, no. 1, 011004.
Patalano, S, Vitolo, F & Lanzotti, A, 2013. A Graph-based
Software Tool for the CAD Modeling of Mechanical
Assemblies. International Conference on Computer
Graphics Theory and Applications GRAPP/IVAPP,
pp. 60-69. Barcelona, Spain.
Peak, RS, Burkhart, RM, Friedenthal, SA, Wilson, MW,
Bajaj, M & Kim, I, 2007. Simulation-Based Design
Using SysML Part 1: A Parametrics Primer. INCOSE
International Symposium. San Diego, California,
USA.
Salehi, V & McMahon, C, 2009. Action Research into the
GRAPP2015-InternationalConferenceonComputerGraphicsTheoryandApplications
24