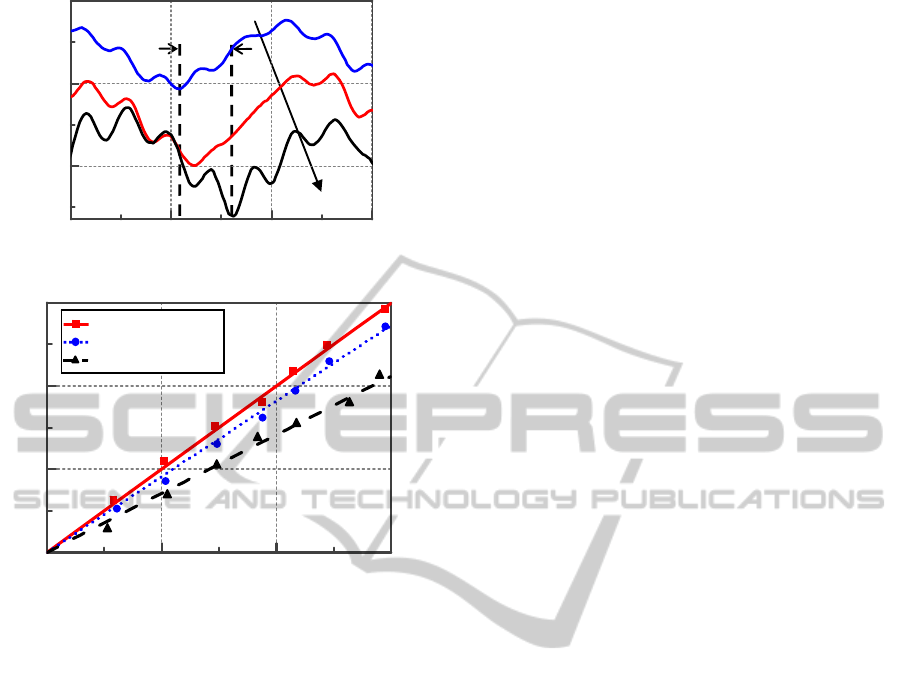
(a)
(b)
Figure 5: Transmission spectra at various applied
pressures on the diaphragm. The centre position of the
Bragg structures are (0, 0), and (b) wavelength shift
versus the pressure when the centre position of the Bragg
structure are (0, 0), (45, 45), and (-84, 84).
represent the measured and simulated results,
respectively. The solid, dotted and dashed line show
the Δλ as the function of P when the center position
of the Bragg structure is (0, 0), (45, 45), and (-84,
84), respectively which shows a good linearity
between the output of the pressure sensor and the
measured pressure. The slopes of the lines C
3
= Δλ/P
is equal to the sensitivity of the nano-opto-
mechanical pressure sensor. C
3
is 1.55×10
-3
nm/kPa,
when the center position of the Bragg structure is (0,
0) which is at least 1.42 times larger than that of the
(-84, 84). The resolution of the nano-opto-
mechanical pressure sensor is limited by the
resolution of the optical spectrum analyzer used in
the experiment. The optical spectrum analyzer
allows for a spectral resolution of approximately 2
pm. Consequently, the pressure resolution is 1.29
kPa which can be obtained by the Eq. (7).
4 CONCLUSIONS
In summary, a highly sensitive nano-opto-
mechanical pressure mapping sensor based on Bragg
structure is designed, fabricated and characterized
for pressures ranging from 0 kPa to 60 kPa. The
sensitivity as high as 1.55 pm/kPa has been
experimentally achieved which is in good agreement
with numerical prediction. The pressure sensor
structure make it possible to detect the shear stress
displacement distribution in highly accurate
measurement with low-cost advantages. The
characteristics indicate potential for various
applications such as mass sensor, bio-medical
sensors and optical integrated circuits etc.
REFERENCES
D. Donlagic and E. Cibula, 2005.All-fiber high-sensitivity
pressure sensor with SiO
2
diaphragm. Opt. Lett.
G. T. Kanellos, G. Papaioannou, D.Tsiokos, C.
Mitrogiannis, G. Nianios and N. Pleros, 2010.Two
dimensional polymer-embedded quasi-distributed
FBG pressure sensor for biomedical applications.
Opti. Express.
Y. C. Chao, W. J. Lai, C.Y. Chen, H. F. Meng, and H W
Zan, 2009."Low voltage active pressure sensor based
on polymer space-change-limited transisitor. Appl.
Phys. Lett.
M. Esashi, H. Komatsu, and T. Matsuo, 1983.Biomedical
pressure sensor using buried piezoresistors. Sens.
Actuators A.
C. S. Sander, J. W. Knutt and J. D. Meindl, 1980.A
monolithic capacitive pressure sensor with pulse-
period output.IEEE Trans. Electron Devices.
D. D. Bruyker, and R. Puers, 2000.Thermostatic control
for temperature compensation of a silicon pressure
sensor.Sens. Actuators A.
M. C. Oh, J. W. Kim, K. J. Kim, and S. S. Lee,
2009.Optical pressure sensors based on vertical
directional coupling with flexible polymer waveguides.
IEEE Photonics Technol. Lett.
M. Shimada, Y. Kinefuchi, and K. Takahashi,
2008.Sleeve-type ultra miniature optical fiber pressure
sensor fabricated by DRIE. IEEE Sensors J.
Y. Zhu and A. Wang, 2005.Miniature fiber-optic pressure
sensor, IEEE Photon. Technol. Lett.
B.J. Luff, J.S.Wilkinson, J. Piehler, U. Hollenbach, J.
Ingenhoff, N. Fabricius, 1998.Integrated optical
Mach–Zehnder biosensor. J. Light. Technol.
M. Ohkawa, M. Izutsu, and T. Sueta. 1989.Integrated
optic pressure sensor on silicon substrate, Appl. Opt.
N. Pelletier, B. Bêche, N. Tahani, J. Zyss, L. Camberlein,
and E.Gaviot, 2007.SU-8 waveguiding interferometric
micro-sensor for gage pressure measurement. Sens.
Actuators A.
1593
-45.0
-46.6
Output transmission (dBm)
60 kPa
0 kPa
1593
15931593
Wavelen
th
nm
0.093 nm
-40.0
-42.5
Pressure P
kPa
Wavelength shift (pm)
93
31
0
40
20 0
62
Position (0, 0)
Position (45, 45)
Position (-84, 84)
1.55 pm/kPa
1.09 pm/kPa
1.41 pm/kPa
60
BIODEVICES2015-InternationalConferenceonBiomedicalElectronicsandDevices
142