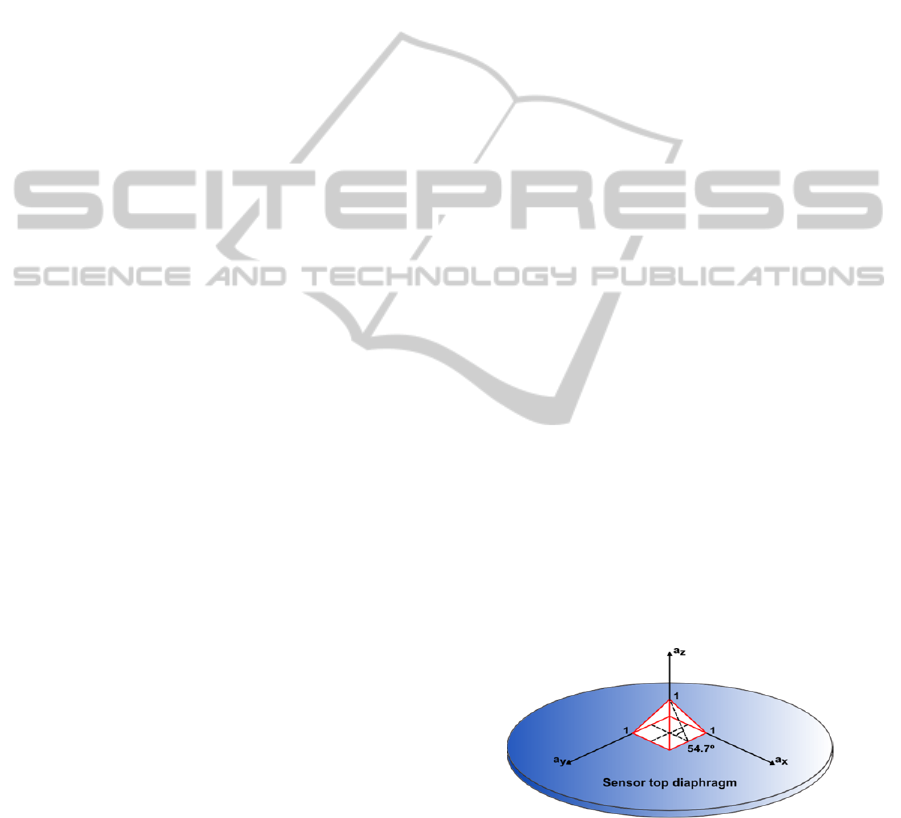
time data from physiological signals related to the
vessel condition, have positioned themselves as an
economic alternative to ISR follow-up.
Smart stents, as implantable electronic devices,
must fulfil certain design constraints, including
small size, low power requirements, output stability,
and reliability over time without recalibration. This
last challenge makes testing and fault modelling
critical issues to validate the fabricated device.
Generally, MEMS testing has been limited to a
set of electrical, optical and mechanical analyses,
used to check the functionality of the device.
However, the correlations between the detected
failures and their underlying physical causes are
usually missing. These relationships are needed to
allow an accurate modelling of complex fabrication
defects, and can be useful in the generation of
realistic faults models, as well as in the development
of capable testing techniques. For this reason, fault
models must include real defective behaviours in
order to reach high fault coverage and test quality.
This work focuses on the generation of a fault
model for an implantable MEMS capacitive pressure
sensor. Finite Elements (FE) tools have been proven
to be necessary to model those faults whose
complexity makes analytical descriptions inapt. The
results from FE analysis will give rise to a realistic
fault model library, and to the development of a
comprehensive Design-for-Test (DfT) methodology.
In Section 2, the most common failure
mechanisms affecting MEMS devices are described.
Section 3 introduces the proposed heterogeneous
system, focusing on the analytical modelling of its
MEMS sensors under fault-free conditions. Section
4 illustrates the need of FE analysis to model the
behaviour of MEMS sensors under the presence of
certain faults. Finally, in Section 5 conclusions are
presented.
2 MEMS FAULT CLASSES AND
FAILURE MECHANISMS
Several failure mechanisms or defects can appear
during the fabrication process of heterogeneous
devices, being possible to distinguish between
defects arising during the CMOS process and defects
occurring during micromachining.
Microelectronic and MEMS components can be
created on the same silicon substrate by means of a
set of conductor, semiconductor and dielectric
layers. Each one of the technological operations
used to grow these layers, such as oxidation,
deposition, photolithography or etching, is a
potential source of defects, where contaminants can
appear, degrading the succeeding fabrication steps.
In the particular case of CMOS-compatible
MEMS, failure mechanisms can be classified
according to the physical property being affected.
MEMS faults can be initially grouped into
parametric or catastrophic types, in the same way as
for analog testing. However, the nature of MEMS
devices gives rise to new types of manufacturing
defects, which require an extended classification
scheme. Thus, it is necessary to distinguish between
faults affecting the microsystem gauge and those
affecting the supporting structure. Each of these
faults can be again classified as a parametric fault,
changing the physical properties of the device and
altering its performance; or as a catastrophic fault,
preventing any use of the system.
In this work, the case of impurities appearing
during the anisotropic wet etching process used to
create diaphragms is analysed in detail. Impurities in
the form of small crystal lattice defects located in the
bulk material during this process can cause the
growth of pyramids on top of the diaphragm.
Depending on their size and location, these pyramids
can strongly change the properties of the diaphragm.
As can be seen in Fig. 1, the sidewall slope of the
pyramids is a fixed parameter which depends on the
angles between the main crystal planes of a single
silicon crystal. For instance, this slope presents a
value of 54.7º in the case of anisotropic wet etching
of a {100} oriented wafer, corresponding to the
angle between the {100} and {111} planes. It must
be noticed that the height of the pyramid can be
obtained from the sidewall slope, so a change in the
base length of the pyramid will alter its size (Rosing,
Reichenbach, Richardson, 2002) (Landsberger,
Nashed, Kahrizi, Paranjape, 1996).
Figure 1: Pyramid defect growth during anisotropic wet
etching process.
3 MEMS PRESSURE SENSOR
MODELLING
One of the simplest and more reliable smart stent
FaultModelingofImplantableMEMSSensors
163