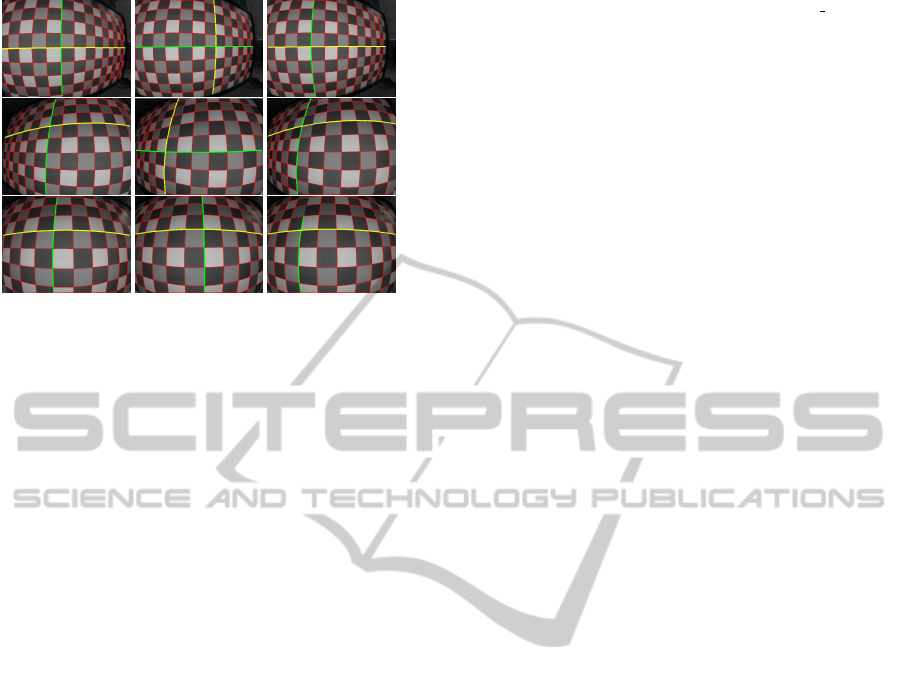
Figure 4: A sample of 3 stereopairs extracted from the
2x10 image set processed according to the second calibra-
tion pipeline, (line bundles object and non-metric calibra-
tion). Each row shows the data corresponding to a stere-
opair. From left to right are shown the grid axis extracted
from the left image, from the right image and the corrected
grid of right image.
The obtained results show that a periodic pattern
can be successfully detected across multiple views
only enforcing the rigidity constraint of the camera
system and the discrete nature of the grid detection
indeterminacy.
5 CONCLUSION
In this paper we derived a new technique, that sim-
plifies the extraction of a symmetric 2D grid pattern
across calibration pattern images obtained using mul-
ticamera systems, under the condition of partial visi-
bility of the calibration object without the use of addi-
tional markers identifying the grid origin and the axis
orientation.
The algorithm effectiveness has been proven on
the simulated muticamera and real stereo camera
datasets. We believe that this work provides a use-
ful solution for a problem that inevitably arises in the
context of multicamera calibration and allows for the
design of a user-friendly camera calibration interface.
REFERENCES
Agisoft Lens (2014). Agisoft lens automatic lens calibration
software. http://www.agisoft.ru/products/lens/. [21
August 2014].
Atcheson, B., Heide, F., and Heidrich, W. (2010). Cal-
tag: High precision fiducial markers for camera cal-
ibration. In Proc. VMV, pages 41–48.
Bouguet, J. (2013). Camera calibration toolbox for matlab.
http://www.vision.caltech.edu/bouguetj/calib doc/.
[21 August 2014].
CAMcal (2014). Camcal camera calibration program.
http://people.scs.carleton.ca/cshu/Research/Projects/
CAMcal/. [8 September 2014].
Datta, A., Kim, J., and Kanade, T. (2009). Accurate camera
calibration using iterative renement of control points.
In ICCV Workshop on Visual Surveillance (VS).
Douskos, V., Grammatikopoulos, L., Kalisperakis, I., Kar-
ras, G., and Petsa, E. (2009). Fauccal: An open source
toolbox for fully automatic camera calibration. In
XXII CIPA Symposium.
Faugeras, O. (1993). Three-Dimensional Computer Vi-
sion: a Geometric Viewpoint. MIT Press, ISBN:
9780262061582.
Fiala, M. and Shu., C. (2008). Self-identifying patterns for
plane-based camera calibration. 19(4):209–216.
Hartley, R. I. and Zisserman, A. (2000). Multiple View Ge-
ometry in Computer Vision. Cambridge University
Press, ISBN: 0521623049.
Heikkila, J. (2000). Geometric camera calibration using cir-
cular control points. 22(10):1066–1077.
Kanatani, K. (1994). Analysis of 3-d rotation fitting. IEEE
T-PAMI, 16(5):543–549.
Kanatani, K. (2009). Calibration of ultrawide fisheye lens
cameras by eigenvalue minimization. IEEE T-PAMI,
35(4):813–822.
Kassir, A. and Peynot, T. (2010). Reliable automatic
camera-laser calibration. In Proc. of ACRA.
Lepetit, V., F.Moreno-Noguer, and P.Fua (2009). Epnp:
An accurate o(n) solution to the pnp problem. IJCV,
81(2).
Mei, C. and Rives, P. (2007). Single view point omnidirec-
tional camera calibration from planar grids. In Proc.
IEEE ICRA, pages 3945–3950.
OpenCV (2014). Open source computer vision library.
http://opencv.org/. [8 September 2014].
Oyamada, Y., Fallavollita, P., and Navab, N. (2012). Single
camera calibration using partially visible calibration
objects based on random dots marker tracking algo-
rithm.
Shu, C., Brunton, A., and Fiala, M. (2003). Automatic grid
finding in calibration patterns using delaunay triangu-
lation. Tech. Rep.
Tsai, Y. R. (1986). An efficient and accurate camera cal-
ibration technique for 3D machine vision. In Proc.
CVPR.
Vaish, V. (2006). The stanford calibration grid de-
tector. http://graphics.stanford.edu/software/findgrid.
[21 August 2014].
Vo, M., Wang, Z., luu, L., and Ma., J. (2011). Advanced
geometric camera calibration for machine vision. Op-
tical Engineering, 50(11).
Wedekind, J., Penders, J., Howarth, M., Lockwood, A. J.,
and Sasada, K. (2013). Using generic image process-
ing operations to detect a calibration grid. Tech. Rep.
Zhang, Z. (2000). A flexible new technique for camera cal-
ibration. IEEE Transactions on Pattern Analysis and
Machine Intelligence, 22(11):1330–1334.
Zhang, Z. (2002). Camera calibration with one-dimensional
objects. volume 4, pages 161–174.
PeriodicPatternsRecoveryforMulticameraCalibration
67