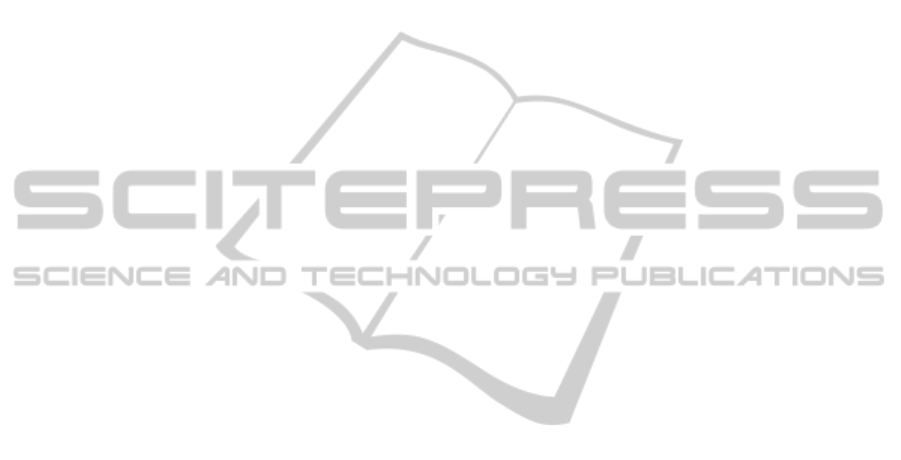
3.2.3 Result
In the foundry the matching procedures can not be
used at the moment. The sand cores pass through a
long way between the production and the assembly to
the mold. On the whole way the orientation of the
sand core can not be defined and the distance of the
camera can change.
However we could show that the sand cores are
distinguishable. In Section 3.2.4 we suggest some ad-
ditional procedures for continue works on the sand
core identification.
3.2.4 Next Steps
To improve the identification rate of the sand cores
additional physical notches can be added to the sand
cores to simplify the orientation detection of the sand
cores. Another approach can be done by object de-
tection. The shape of the sand core can be detected
and delivers additional information about the position
orientation and distance.
4 CONCLUSION
In this research paper we have shown that optical
sensors may well be used for data acquisition in the
rough environments of foundries. Especially for mid-
dle sized foundries with automation levels from low
to medium this approach is very promising. We have
developed a complete object marking and recogni-
tion system for cast parts, including a self developed
code, an autonomous mechanical marking element
for molds and a procedure to recognize the marked
cast parts by image analysis. With the planned im-
provements described above we expect to achieve ac-
ceptable failure rates. Furthermore we have investi-
gated in sand core identification by image analysis.
In that process we are not as close to an industrial
application like in the case of cast parts. The main
problem in this case is, that the recognition methods
which work well are not rotation invariant. We plan to
improve this method by adding notches to the cores,
which allows the recognition procedure to identify the
orientation in a first step.
Our next steps are further improvements for the
processes described in this paper, especially regarding
the robustness of our algorithms. Furthermore, there
are more process parameters to be acquired, e.g. anal-
ysis of cast spurts and flask layout or damage recog-
nition for sandcores. The initial analysis of our col-
leagues of mechanical engineering has shown, that the
first two important acquired data sets described in this
paper will already help to reduce failure rate in the ex-
amined foundries extremely. It is important to men-
tion, that only a few defect cast parts may cause very
high impact to total cost and, of course, to nature, be-
cause especially in medium sized foundries cast parts
tend to be quite large, up to ten or twelve tons.
REFERENCES
Baggio, D. (2012). Mastering OpenCV with Practical Com-
puter Vision Projects. PACKT Publishing, Birming-
ham, 1st edition.
Clemens, H. (2008). BuhlMark praegt die Produktdaten
auf das Gussteil und macht damit jedes Teil eindeutig
rueckverfolgbar.
D. Hartmann, J. Gottschling, S. M. M. S. (2014). Intelli-
gente Prozesssteuerung in Giessereien.
Duda, R. O. and Hart, P. E. (1972). Use of the Hough Trans-
formation To Detect Lines and Curves in Pictures.
E.N.Gilbert (1957). Gray Codes and Paths on the n-Cube.
Ethan, R. (2011). Orb: an efficient alternative to sift or surf.
In Computer Vision (ICCV), 2011 IEEE International
Conference on, pages 2564–2571. IEEE.
Gagne, M. (2004). Sorelmetal Gusseisen mit Kugelgraphit.
Rio Tinto Iron and Titanium, Montreal (Quebec), 1st
edition.
Gray, F. (1947). Gray Code.
Hasse, S. (2003). Guss und Gefuegefehler. Schiele und
Schoen, Berlin, second edition edition.
Hovorka, F. (1996). Method for identifying cast parts. US
Patent 5,584,113.
Kimme, C., Ballard, D., and Sklasnky, J. (1975). Finding
Circles by an Array of Accumulators.
Laganiere, J. (2011). OpenCV 2 Computer Vision Appli-
cation Programming Cookbook. PACKT Publishing,
Birmingham, 1st edition.
Leong, L. K. and Yue, W. (2009). Extraction of 2D Barcode
Using Keypoint Selection and Line Detection. In Ad-
vances in multimedia information processing - PCM.
Springer-Verlag.
Lorsakul, A. (2007). Traffic Sign Recognition for Intelli-
gent Vehicle/Driver Assistance System Using Neural
Network on OpenCV.
Meissner, K. (2011). Die neue Giessuhr vollflexibles
Markiersystem fr Gussteile.
Nicholson, M. and Monahan, B. (1999). Having the capa-
bility of operating over a broad range of temperatures;
capable of operation in harsh, high temperature fac-
tory environments. US Patent 5,973,599.
Parker, J. R. (2011). Algorithms for Image Processing and
Computer Vision. Wiley Publishing, Inc., Indeanapo-
lis, second edition edition.
Wadhwa, R. S. (2013). Traceability and Data Support in
SME Manufacturing.
VISAPP2015-InternationalConferenceonComputerVisionTheoryandApplications
70