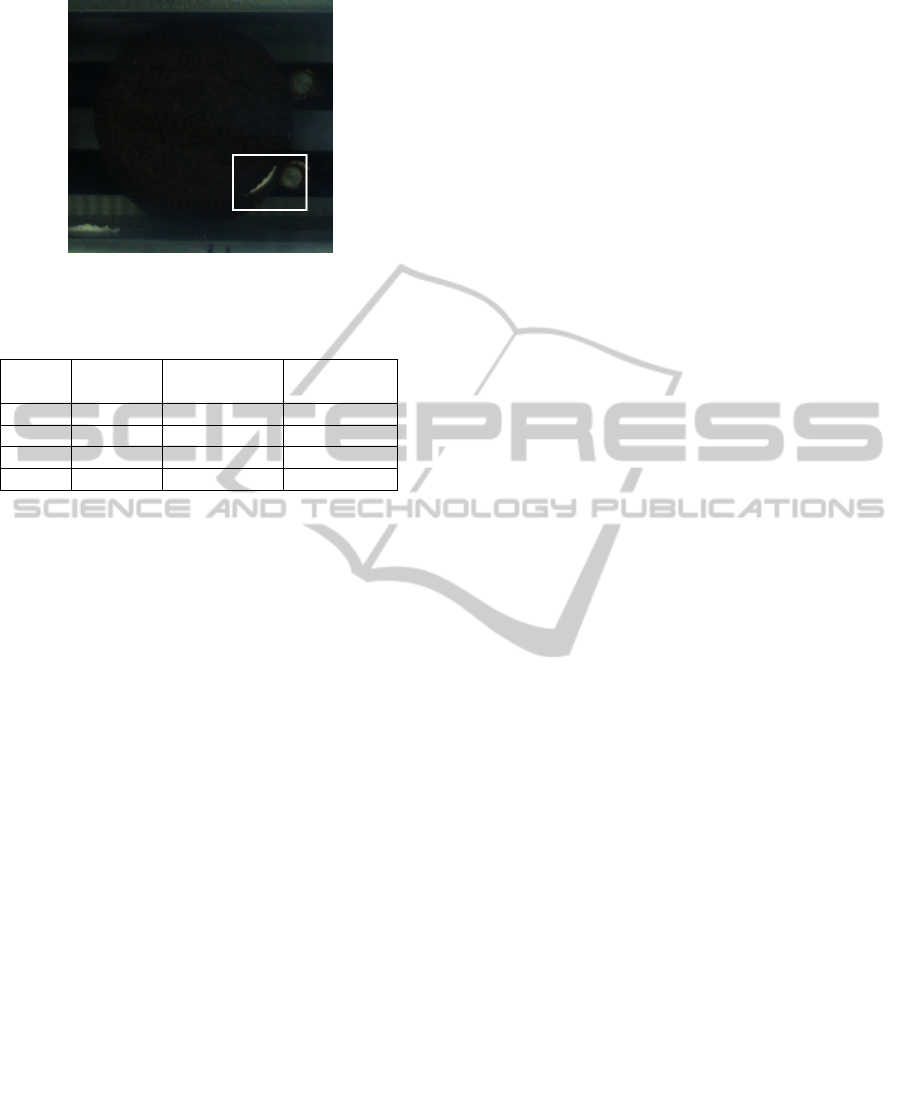
Figure 10: The result of cream overflow biscuit.
Table 2: The proportion of FP and FN in cream overflow
detection.
Group
Number of
biscuits
Proportion of
false positive
Proportion of
false negative
1 21756 0.05‰ 0.14‰
2 22052 0.14‰ 0.18‰
3 22034 0.09‰ 0.32‰
4 126843 0.12‰ 0.21‰
The time consuming of detecting a biscuit is less
than 40 ms in on-line experiments, which can satisfy
the speed of production. The experiments
demonstrate that our system is effective and efficient.
5 CONCLUSIONS
In this paper, a biscuit inspection system is proposed
in on-line detection. The feature extraction algorithm
can be described to three steps: locate and unfold
the ring area; calculate the membership for pixels;
find the longest line in each column and compose
the feature vector. The application of polarized light
can detect cream overflow of biscuit. The result of
experiment shows that our method is accurate and
can meet real-time demands. The system has been
implemented on biscuit production line.
ACKNOWLEDGEMENTS
Partially supported by Postdoctoral Fund
(No.023207009).
REFERENCES
Chenbo, S., Guijin, W., Xinggang, L., Yongming, W.,
Chao, L., Quan, M., 2010. Topology based affine
invariant descriptor for MSERs. IEEE Conference on
Image Processing, 133-136.
Eugene, H., 2002. Optics, Addison Wesley. United
States of America, 4
th
edition.
Freund, Y. and Schapire, R. E., 1997. A decision-theoretic
generalization of on-line learning and an application to
boosting. Journal of computer and system sciences, 55,
119-139.
Heikkila, M., Pietikainen, M., 2006. A texture-based
method for modeling the background and detecting
moving objects. IEEE Transactions on pattern
analysis and machine intelligence, 28(4), 657-662.
Herbert, B., Andreas, E., Tinne, T., Luc, V.G,. 2008. Surf:
Speeded Up Robust Features. Computer vision and
image understanding, 110(3) 346-359.
Hernandez, J.A., Heyd, B., Trystram, G., 2007. On-line
assessment of brightness and surface kinetics during
coffee roasting. Journal of food engineering, 87(3),
314-322.
Hoang, M., 2005. Energy-based geometric multi-model
fitting. International Journal of Computer Vision, 97(2)
23-147.
Hossam, I., Yuri, B., 2012. Color texture measurement
and segmentaion. Signal Processing, 85(2) 265-275.
Johannes, A.R., Magne, Setnes., Janos, A., 2001. Learning
fuzzy classification rules from labeled data.
Information sciences, 150(2003) 77-93.
Liu, C., Wang, G., Lin, X., Li, L., 2012. Person re-
identification by spatial pyramid color representation
and local region matching. IEICE Trans. Information
& System. E95D, 2154-2157.
Mahalakshmi, T., Muthaiah, R. and Swaminathan, P.,
2012. Review Article: An Overview of Template
Matching Technique in Image Processing. Research
journal of applied sciences, engineering and
technology. 4(24): 5469-5473.
Mak, K. L., Peng, P., Lau, H. Y. K., 2005. A real-time
computer vision system for detecting defects in textile
fabrics. ICIT’05, IEEE International Conference on
Industrial Technology., 469-474.
McNaught, A. D., Wilkinson, A., 1997. Compendium of
Chemical Terminology, International Union of Pure
and Applied Chemistry. Zürich. 2
nd
edition.
Mikolajczyk, K., Schmid, C., 2005. A performance
evaluation of local descriptors. IEEE Transactions on
pattern analysis and machine intelligence, 27(10),
1615-1630.
Perrot, N., Trystram, D., Guennec, F. And Guely, F.,
1996. Sensor fusion for real time quality evaluation of
biscuit during baking. journal of food engineering,
29(3-4), 301-315.
Senni, L., Ricci, M., Palazzi, A., 2014. On-line automatic
detection of foreign bodies in biscuits by infrared
thermography and image processing. journal of food
engineering, 128, 146-156.
Shi, C., Wang, G., Pei, X., He, B., Lin, X., 2012. Stereo
matching using local plane fitting in confidence-based
support window. IEICE Trans. Information & System.
E95D, 699-702.
Vollhardt, K. P. C., Schore, N. E., 2003. Organic
Chemistry, W. H. Freeman. American.4
th
edition.
VISAPP2015-InternationalConferenceonComputerVisionTheoryandApplications
536