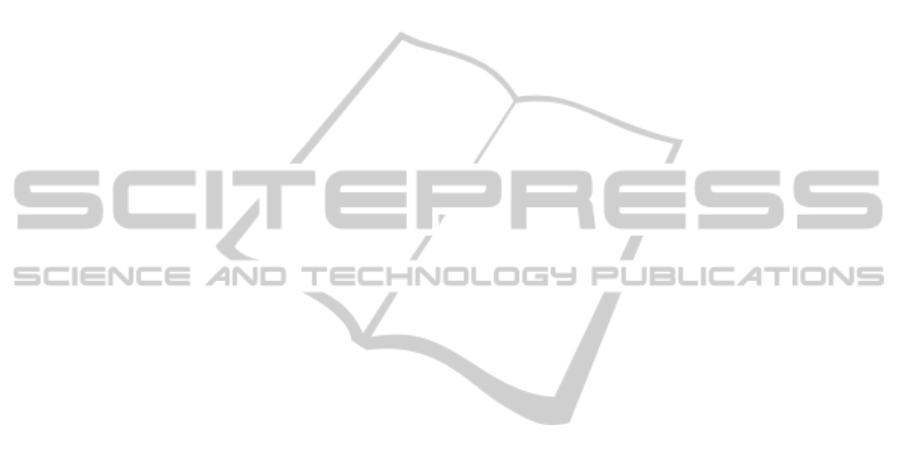
2 BACKGROUND MATERIAL
2.1 Real-Time Systems and Scheduling
Policy
Real-Time Systems (RTS) are defined as these sys-
tems in which correctness depends not only on the
correct result, but they must also consider time con-
straints, mainly deadlines, to deliver this result. Our
work focuses on soft real-time control tasks i.e. tasks
that may miss deadlines from time to time (in contrast
to the so called hard real-time tasks). As a conse-
quence the objective of our scheduling algorithm is to
optimize the QoC. We use the scheduling theory in or-
der to check temporal constraints. The EDF algorithm
(Liu and Layland, 1973) is probably the most known
fixed-job priority assignment scheduler in real-time
systems. It is optimal regarding schedulability in the
context of independent tasks and preemptive unipro-
cessor scheduling. Our aim in using EDF is to im-
prove the QoC which does not require, as shown later
in this paper, to meet all the deadlines.
2.2 Power Management Techniques
The conventional power management techniques are
classified into two categories based on the nature of
energy dissipation reduction. One of them is Dy-
namic Power Management (DPM). It aims to reduce
the static energy dissipation by switching the active
component to the low power state or shutting down
the idle components. The other technique is Dynamic
Voltage and Frequency Selection (DVFS) which aims
to reduce the dynamic energy dissipation by lowering
the operating frequency of the processor. In our work,
we consider the DVFS capabilities.
3 RELATED WORKS
Traditional real-time scheduling algorithms, after the
seminal works of (Liu and Layland, 1973), that in-
troduced Rate Monotonic (RM) and Earliest Dead-
line First (EDF), are built on precisely known and
fixed timing constraints and depend on workload to
provide performance guarantees in predictable envi-
ronments. However, the Worst-Case Execution Time
(WCET) taken into account in task models is the up-
per bound of a highly volatile parameter (Axer et al.,
2014). In addition, these classical algorithms may
perform poorly in dynamic environments. The feed-
back scheduling (FBS) (Cervin, 2003; Xia, 2006;
˚
Arz´en et al., 2006) offers a promising approach to
overcome these limitations where actual execution
times are not fixed and unknown until the task com-
pletes. Several authors treated the problems of min-
imizing power by combining feedback control meth-
ods and DVFS strategy in order to take the effective
task duration into account. For instance, the popu-
lar PID (Proportional-Integral-Derivative)control has
been integrated into several DVFS algorithms (Soria-
Lopez et al., 2005). A feedback fuzzy-DVFS schedul-
ing method has been developed in (Jin et al., 2007). In
(Xia et al., 2008), a solution is proposed to achieve
further reduction in energy consumption over pure
DVFS while not jeopardizing the quality of control,
the sampling period of each control loop is adapted
to its actual control performance, thus exploring flex-
ible timing constraints on control tasks. However,
these algorithms do not consider energy harvesting
capabilities. For ambient energy harvesting, a variant
of EDF, called Lazy Scheduling Algorithm (LSA) is
proposed in (Moser et al., 2007) to optimally sched-
ule tasks with deadlines, periodic or not. However,
the task slack is not exploited for energy savings and
DVFS was not considered (Liu et al., 2012). Some
heuristics have been compared to LSA in (Chetto and
Zhang, 2010) with no DVFS capabilities. Recently,
in (Chetto, 2014) a novel energy-aware scheduling al-
gorithm, namely ED-H, is presented. This algorithm,
based on WCET, proved to be optimal and appropri-
ate for the scheduling of real time jobs.
In our work, we are concerned with the DVFS
technique that we apply in the so-called real-time en-
ergy harvesting systems. Closely related to our work,
Liu et al. (Liu et al., 2008) proposed a DVFS algo-
rithm (called EA-DVFS) to enhance the performance
of LSA. EA-DVFS adjusts the processor behavior ac-
cording to the stored energy and the energy prediction
(harvested energy in future). Particularly, if the sys-
tem has a sufficient amount of energy, tasks are ex-
ecuted at full speed; otherwise, the processor slows
down to save energy. However, EA-DVFS is based
on WCET and considers one task at a time instead
of considering all tasks together. In addition, since
the EA-DVFS algorithm uses the energy prediction,
it schedules the task at full speed if there may be just
as little as 1% energy left in the energy storage while
the system can operate at full speed for a task without
depleting the energy. That is not the desired behavior.
More recent works can be found in (Liu et al., 2009;
Liu et al., 2012), which also present extensions of
LSA with DVFS technical and permit to improve the
deadline miss rate and energy saving. The proposed
algorithms compute both the start time and finishing
time of every task from timing and energy constraints
such as WCET. As mentioned above, this will lead
PECCS2015-5thInternationalConferenceonPervasiveandEmbeddedComputingandCommunicationSystems
350