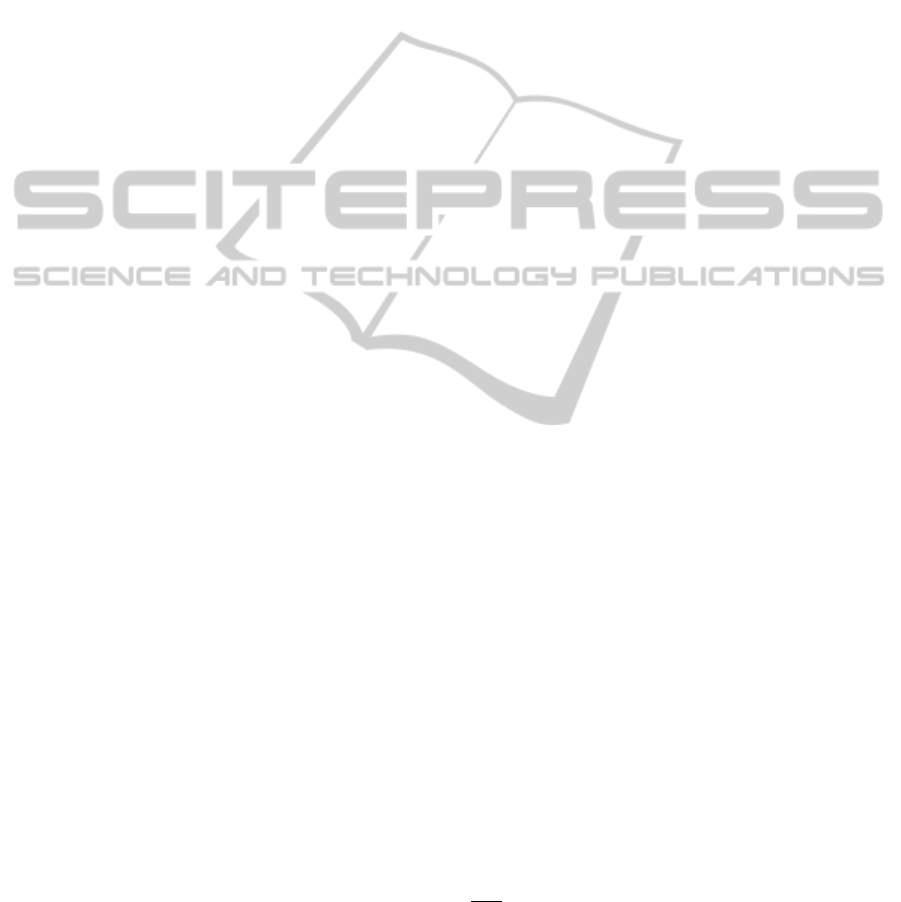
faces behind the crack tip will act like cables, forc-
ing the faces to close, creating a traction stress in that
area. However, to maintain a force equilibrium, a
compression field is formed ahead the crack tip. The
compression-traction fields move as the crack grows.
1.3 Crack/Delamination Detection in
Fibre Reinforced Plastic Materials
Sensing technology has been implemented in order to
track delamination in FRP materials. Acoustic emis-
sion (Silversides et al., 2013) that measures the stress
waves generated by the crack front growing, vibration
(Kyriazoglou and Guild, 2004) that detects changes in
the specific damping capacity of the structure, model
analysis (Hu et al., 2006) by monitoring the material
natural frequencies and mode shapes, piezo-electric
actuators/sensors and wavelet analysis (Yan and Yam,
2002) based on the energy variation of the structural
dynamic. However, these measurement systems have
several limitations, among these the need for quali-
fied operators, expensive hardware and impractical to
use under operation. Also, to detect delamination in
FRP materials the sensor must be embedded in the
laminate layers or in the interface of the FRP and a
structural adhesive.
Fibre Bragg Gratings (FBG) have the capability to
be embedded in the FRP material, even in an opera-
tional structure, without compromising its structural
resistance. This is due to the FBG reduced size, with
a diameter of 125µm, it is virtual non-intrusive to the
material. Also, FBG sensors present other interesting
features, such high resolution, multiplexing capabil-
ity, immunity to electromagnetic fields, chemical in-
ertness and long term stability (fatigue behaviour).
1.4 Crack/Delamination Detection by
Embedded Fibre Bragg Gratings
During a crack/delamination event different fracture
features will be present near the crack tip. Being able
to identify and measure this specific phenomena with
a FBG sensor is a key factor to correctly determine
the presence of damage and it growth.
In figure 2, the different stages of the FBG re-
sponses under a crack growth event are presented.
First, before the crack reach the proximity of the grat-
ing, figure 2a), the material will build up uniform
strain (considering structure loading or geometric sin-
gularities distant enough from the grating), that will
make a uniform wavelength shift in the FBG reflected
peak. Next, a compression field is formed ahead of
the crack tip due to the formation of a crack bridging
zone, witch was discussed in section 1.2, will reach
the grating area creating a peak splitting of the FGB
response, figure 2b). This peak split phenomena will
be discussed later, but briefly is due a birefringent ef-
fect. Then, when the grating is near the influence of
the crack singularity (region dominated by stress con-
centration) a non-uniform strain field will also create
a change in the shape of the reflected peak, as showed
in figure 2c). Finally, after the crack passes the FBG
sensor, the shape of the reflected peak will go back
to the original shape, and the sensor response will
again be a simple wavelength shift, because at this
stage only uniform strains will be present in the FBG
proximity, figure 2d).
2 FIBRE BRAGG GRATING
WORKING PRINCIPLE
A Fibre Bragg Grating (FBG) is formed by a perma-
nent periodic modulation of the refractive index along
a section of an optical fibre, by exposing the optical
fibre to an interference pattern of intense ultra-violet
light (Hill and Meltz, 1997). The photosensitivity of
the silica exposed to the ultra-violet light is increased,
so when the optical fibre is illuminated by a broad-
band light source a very narrow wavelength band is
reflected back. The spectral response of a homoge-
neous FBG is a single peak centred at the wavelength
λ
b
. The wavelength λ
b
is described by the Bragg con-
dition ,
λ
B
= 2n
e f f ,0
Λ
,0
(1)
where n
0
is the mean effective refractive index at the
location of the grating, the index 0 denotes unstrained
conditions (initial state). n
e f f
is the effective refrac-
tive index and Λ is the constant nominal period of the
refractive index modulation (Morey et al., 1990).
2.1 Fibre Bragg Grating Response to a
Uniform Variation of Strain and/or
Temperature
The wavelength shift ∆λ
b
of an embedded FBG under
a uniform variation of strain ε
zz
, and temperature ∆T
is given by the equation 2 (Zhang et al., 2008),
∆λ
b
λ
b
= (1 − p
e
)ε
zz
+ [(1 − p
e
)(α
s
− α
f
) + ξ]∆T (2)
where p
e
is a photoelastic coefficients, α
s
and α
f
are
the thermal expansion coefficients of the host material
and the optical fibre, respectively, and ξ is the thermo-
optic coefficient.
PHOTOPTICS2015-InternationalConferenceonPhotonics,OpticsandLaserTechnology
134