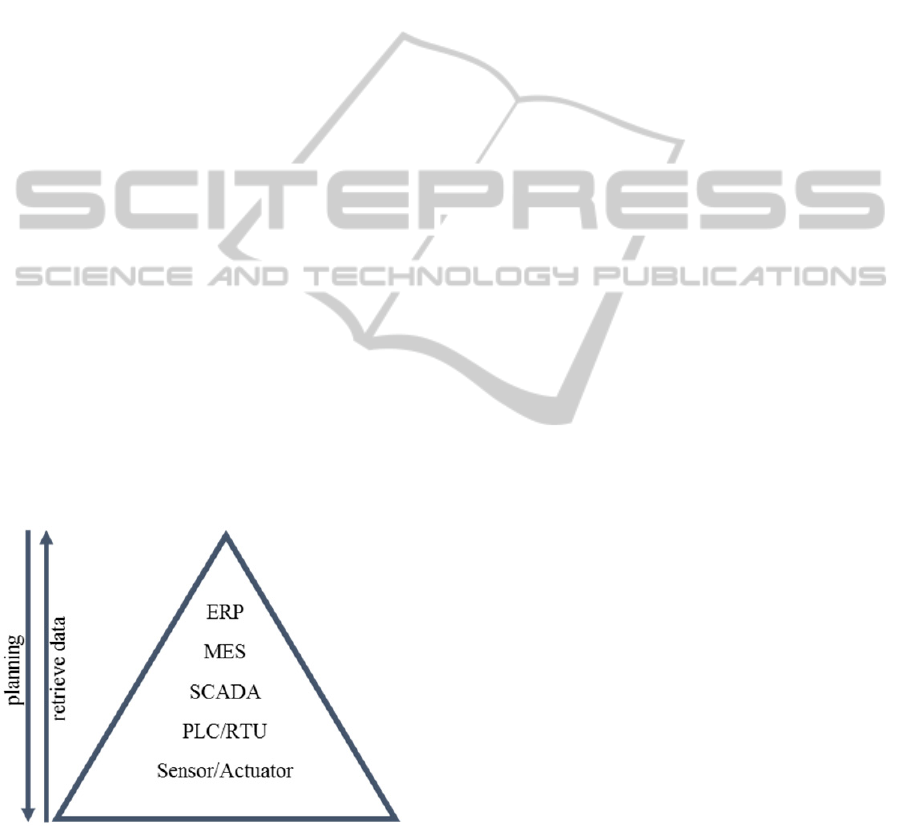
security analysis of a Beckhoff CX5020, a
commonly used PLC in SCADA/ICS systems. The
goal of the investigation is to find out, if a modern
PLC, which is based on a well-known platform like
Windows CE, has exploitable vulnerabilities in the
platform or the PLC part of the system. The
description of our investigation will start in chapter
2 with a brief description of ICS, SCADA, the
protocols used and the specifics of a Beckhoff
CX5020. Chapter 3 and 4 explain our analysis
approach and results which lead to a set of possible
attacks described in chapter 5. Chapter 6 gives a set
of recommendations to the manufacturer and to
users of the Beckhoff CX5020, which protect
against the described attacks.
2 ICS/SCADA SECURITY
2.1 SCADA Systems and Protocols
A typical SCADA system consists of different parts.
The low-level control algorithm is running on a PLC
or RTU (Remote Terminal Unit). These devices are
connected to sensors and actuators. They retrieve
sensor data, evaluate the local system state and
control actuators based on the data evaluation result.
Multiple SCADA systems operate as MES
(Manufacturing Execution System) and several
MESs are controlled by ERP (Enterprise Resource
Planning). The layering of the different systems is
depicted in the automation pyramid in Figure 1.
Figure 1: Automation pyramid.
An HMI (Human Machine Interface) is used to
present the current system state and allows to
manually edit parameters. An HMI’s control
directive is not limited to one PLC or RTU, it is
more likely to control multiple devices via a single
HMI. Therefore the PLC or RTU and HMI have to
be interconnected. A local setup is called remote
site. The MTU (Master Terminal Unit) is a central
place where the system state of multiple remote sites
is supervised and controlled from (Krutz 2006:7). To
achieve supervisory control and data acquisition an
EWS (Engineering Workstation) is running at the
MTU. It is a normal computer with specific SCADA
software installed that allows remote diagnostics,
sending control instructions and reprogramming. A
so-called historian saves retrieved telemetry data of
remote sites into a central database for future
evaluation (Trend Micro Incorporated:5).
SCADA makes use of networks protocols to
transport PLC administration and programming
commands. The protocols are also used for
communication between PLCs. The connection to
corporate networks and/or the Internet – for
instance, for remote maintenance – is frequently
realized through standard programs such as HTTP,
Telnet, or FTP. Connectivity on the link layer
usually takes place via Ethernet.
2.2 General SCADA Security Issues
Many SCADA systems nowadays are based on or
encapsulate higher layer protocols in unencrypted
and unauthenticated protocols like Telnet. Integrated
HMIs, which simplify control, usually operate over
HTTP and have no encryption for login credentials.
Many of the special programs and protocols used
for programming of PLCs and controlling the
infrastructure of ICSs are unsecure as well. At the
time of their development security was not part of
the requirements. Therefore, they turn out to be a
security risk (European Network and Information
Security Agency 2011a:27).
It is this kind of vulnerabilities, which allows
viruses like “Stuxnet” to be successful. Stuxnet was
not only able to exploit operating systems in the
control centre, it was also able to continue the attack
on downstream PLCs, which had no protection
against the attack. Vulnerabilities in the protocols
helped to obtain further rights and infected
machines, using for instance hardcoded passwords
of the PLCs or the credentials of the database server.
As a reaction to these new threats the automation
industry has started to develop better and more
secure components. Still, security by design, as it is
applied in software engineering by the traditional
software industry, is still a new area for ICS
manufacturers and mistakes are made. And even if
new and more secure components are made
available for retrofit or replacement of insecure parts
of an ICS, many companies avoid modernization as
ICISSP2015-1stInternationalConferenceonInformationSystemsSecurityandPrivacy
138