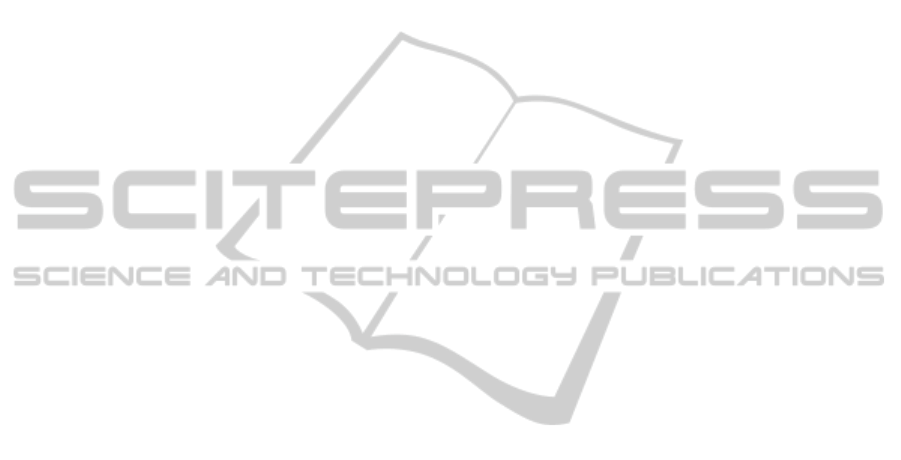
efficiency of production management on shop floor
level implemented merely by software.
Analysis of potential target functions and
possible algorithms for solving the problem are
presented for the stated problem of balanced load of
production facilities. Other two approaches are
based on historical information accumulated in the
industrial base. Statement of primal and inverse
problems of assessment and prediction of shop
schedule is presented, as well as flow charts of their
solution. Statement and solution chart of problem of
decision-making support during assignment of
executor is also given. Benefits for shop floor staff
in their routine operations are identified for all the
approaches.
REFERENCES
Boussaïd, I., Lepagnot, J., Siarry, P., 2013. A survey on
optimization metaheuristics. Information Sciences.
237. p. 82–117.
Abazari, A.M., Solimanpur, M., Sattari, H., 2012.
Optimum loading of machines in a flexible
manufacturing system used a mixed-integer linear
mathematical programming model and genetic
algorithm. Computers & Industrial Engineering. 62
(2). p. 469-478.
Xi, Y., Jang, J., 2012. Scheduling jobs on identical parallel
machines with unequal future ready time and sequence
dependent setup: An experimental study. International
Journal of Production Economics. 137. p. 1–10.
Lei, D., Guo, X., 2014. An effective neighborhood search
for scheduling in dual-resource constrained interval
job shop with environmental objective. International
Journal of Production Economics.
Huang, R.-H., Yang, C.-L., Cheng, W.-C., 2013. Flexible
job shop scheduling with due window - a two-
pheromone ant colony approach. International Journal
of Production Economics. 141. p. 685–697.
Borba, L., Ritt, M., 2014. A heuristic and a branch-and-
bound algorithm for the Assembly Line Worker
Assignment and Balancing Problem. Computers &
Operations Research. 45. p. 87–96.
Mutlu, O., Polat, O., Supciller, A.A., 2013. An iterative
genetic algorithm for the assembly line worker
assignment and balancing problem of type-II.
Computers & Operations Research. 40. p. 418–426.
Levi, Y., 2011. Theory, practice and results of the
application of integrated management in machinery
production. MES – Theory and Practice. 3.
Zhang, R., Song, S., Wu, C., 2013. A hybrid artificial bee
colony algorithm for the job shop scheduling problem.
International Journal of Production Economics. 141.
p. 167–178.
Reingold, E., Nievergelt, J., Deo, N., 1980. Combinatorial
algorithms. Theory and practice, Mir. Moscow.
Conway, R.W., Maxwell, W.L., Miller, L.W., 1975.
Theory of scheduling, Science. Moscow.
Spears, W., 2000. Evolutionary algorithms: the role of
mutation and recombination, Springer. Heidelberg.
Kennedy, J., Eberhart, R., 1995. Particle Swarm
Optimization. Proceedings of IEEE International
Conference on Neural Networks. 4. p. 1942-1948.
Mullen, R.J., Monekosso, D., Barman, S., Remagnino, P.,
2009. A review of ant algorithms. Expert Systems with
Applications. 36. p. 9608–9617.
Fister, I., Fister Jr., I., Yang, X.-S., Brest, J., 2013. A
comprehensive review of firefly algorithms. Swarm
and Evolutionary Computation. 13. p. 34–46.
Kobzar, A.I., 2006. Applied mathematical statistics. For
engineers and scientists, Fizmatlit. Moscow.
Wong, B.K., Lai, V.S., 2011. A survey of the application
of fuzzy set theory in production and operations
management: 1998–2009. International Journal of
Production Economics. 129. p. 157–168.
Haykin, S., 2006. Neural networks: a comprehensive
foundation, Williams. Moscow, 2
nd
edition.
Graupe, D., 2007. Principles of artificial neural networks,
World Scientific. Singapore, 2
nd
edition.
ICEIS2015-17thInternationalConferenceonEnterpriseInformationSystems
564