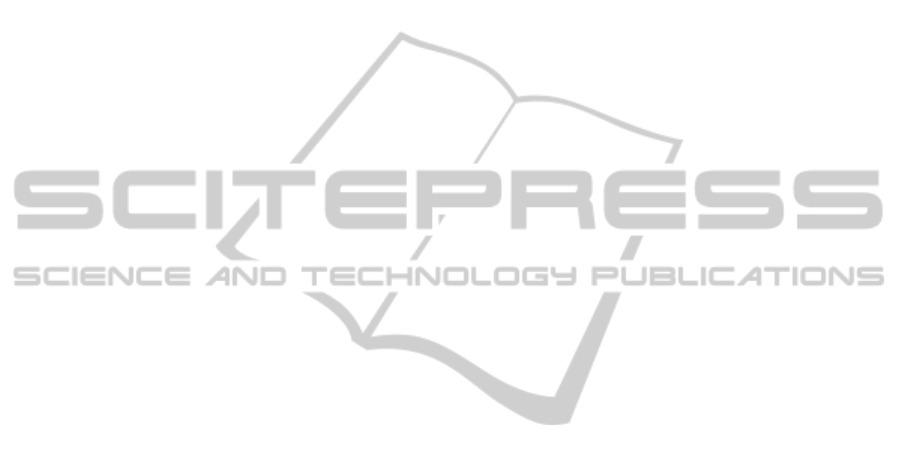
10.1145/2047196.2047270 (Accessed June 11, 2014).
Izadi, S., Newcombe, R.A., et al., 2011. KinectFusion:
real-time dynamic 3D surface reconstruction and in-
teraction. In ACM SIGGRAPH 2011 Talks. SIG-
GRAPH ’11. New York, NY, USA: ACM, pp. 23:1–
23:1. Available at: http://doi.acm.org/10.1145/
2037826.2037857 (Accessed October 10, 2013).
Kainz, B. et al., 2012. OmniKinect: real-time dense volu-
metric data acquisition and applications. In Proceed-
ings of the 18th ACM symposium on Virtual reality
software and technology. VRST ’12. New York, NY,
USA: ACM, pp. 25–32. Available at:
http://doi.acm.org/10.1145/2407336.2407342 (Ac-
cessed October 10, 2013).
Khoshelham, K., 2011. Accuracy Analysis of Kinect
Depth Data. ISPRS Journal of Photogrammetry and
Remote Sensing, (XXXVIII - 5/W12), p.6.
Kückelhaus, M. et al., 2013. Low-cost sensor technology -
A DHL perspective on implications and use cases for
the logistics industry M. Wegner, ed. Available at:
http://www.dhl.com/content/dam/downloads/g0/about
_us/innovation/CSI_Studie_Low_Sensor.PDF.
Litomisky, K. & Bhanu, B., 2013. Removing Moving
Objects from Point Cloud Scenes. In X. Jiang et al.,
eds. Advances in Depth Image Analysis and Applica-
tions. Lecture Notes in Computer Science. Springer
Berlin Heidelberg, pp. 50–58. Available at:
http://link.springer.com/chapter/10.1007/978-3-642-
40303-3_6 (Accessed June 25, 2014).
Metzger, A. et al., 2014. Comparing and Combining Pre-
dictive Business Process Monitoring Techniques.
IEEE Transactions on Systems, Man, and Cybernetics:
Systems, Early Access Online.
Microsoft, 2014. Kinect for Windows. Available at:
https://www.microsoft.com/en-us/kinectforwindows/.
Microsoft Developer Network, 2014. Kinect Fusion.
Available at: http://msdn.microsoft.com/en-
us/library/dn188670.aspx.
Microsoft Developer Network, 2013. Kinect SDK with
Kinect Fusion. Available at: http://blogs.msdn.com/b/
kinectforwindows/archive/2013/03/18/the-latest-
kinect-for-windows-sdk-is-here.aspx.
Newcombe, R.A. et al., 2011. KinectFusion: Real-time
dense surface mapping and tracking. In 2011 10th
IEEE International Symposium on Mixed and Aug-
mented Reality (ISMAR). 2011 10th IEEE Internation-
al Symposium on Mixed and Augmented Reality (IS-
MAR). pp. 127–136.
Prechelt, L., 2001. Kontrollierte Experimente in der Soft-
waretechnik: Potenzial und Methodik, Springer-Verlag
GmbH.
Rasmussen, C. et al., 2013. Towards functional labeling of
utility vehicle point clouds for humanoid driving. In
2013 IEEE International Conference on Technologies
for Practical Robot Applications (TePRA). 2013 IEEE
International Conference on Technologies for Practical
Robot Applications (TePRA). pp. 1–6.
Roth, H. & Vona, M., 2012. Moving Volume KinectFu-
sion. In British Machine Vision Association, pp.
112.1–112.11. Available at: http://www.bmva.org/
bmvc/2012/BMVC/paper112/index.html (Accessed
June 23, 2014).
Smisek, J., Jancosek, M. & Pajdla, T., 2011. 3D with
Kinect. In 2011 IEEE International Conference on
Computer Vision Workshops (ICCV Workshops). 2011
IEEE International Conference on Computer Vision
Workshops (ICCV Workshops). pp. 1154–1160.
Whelan, T. et al., 2012. Kintinuous: Spatially Extended
KinectFusion. Available at: http://dspace.mit.edu/
handle/1721.1/71756 (Accessed June 23, 2014).
Xingyan Li et al., 2012. Using Kinect for monitoring
warehouse order picking operations. In Proceedings of
Australasian Conference on Robotics and Automation.
Australasian Conference on Robotics and Automation.
Victoria University of Wellington, New Zealand.
Xu, D. et al., 2012. Kinect-Based Easy 3D Object Recon-
struction. In W. Lin et al., eds. Advances in Multime-
dia Information Processing – PCM 2012. Lecture
Notes in Computer Science. Springer Berlin Heidel-
berg, pp. 476–483. Available at:
http://link.springer.com/chapter/10.1007/978-3-642 -
34778-8_44 (Accessed October 10, 2013).
Zeng, M. et al., 2012. A Memory-Efficient KinectFusion
Using Octree. In S.-M. Hu & R. R. Martin, eds. Com-
putational Visual Media. Lecture Notes in Computer
Science. Springer Berlin Heidelberg, pp. 234–241.
Available at: http://link.springer.com/chapter/
10.1007/978-3-642-34263-9_30 (Accessed October
10, 2013).
Zhou, Q.-Y. & Koltun, V., 2013. Dense scene reconstruc-
tion with points of interest. ACM Trans. Graph., 32(4),
pp.112:1–112:8.
ENASE2015-10thInternationalConferenceonEvaluationofNovelSoftwareApproachestoSoftwareEngineering
330