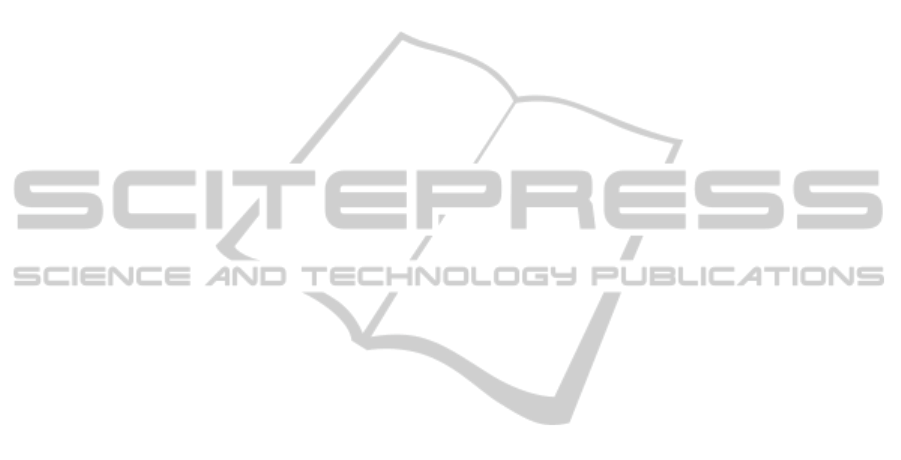
our approach with the exact solution obtained by ap-
plying an exhaustive algorithm that comprehensively
enumerates all the solutions finding the one that pro-
duces the minimal cost. We also perform a large set
of experiments evaluating the impact of the different
parameters of our SA approach to the accuracy of the
solution and the efficiency of the algorithm in terms
of execution time, with the aim of tuning the optimal
values of such parameters for future execution of the
same algorithm.
2 RELATED WORK
In this paper, we present an efficient and general
method for solving routine maintenance scheduling
problems based on SA metaheuristic. Several works
in literature propose the use of SA for the solution
of scheduling problems in the context of the main-
tenance of specific installations, especially power
plants. In (J.T. Saraiva et al., 2011), authors address
the problem of the periodic maintenance of electric
generators by using SA. They aim at scheduling sys-
tem maintenance operations along a planning horizon
assuming that the time interval between maintenance
actions for the same generator is fixed. In our ap-
proach, we do not take into consideration the time in-
terval between maintenance actions but we deal with
the scheduling of interventions that are supposed to
be conducted in a certain working day accordingly to
a predetermined business policy. As in (J.T. Saraiva
et al., 2011), (Keshav P. Dahal and Nopasit Chakpi-
tak, 2006) deals with the maintenance of generators
in a power plant by using a hybrid approach based
on a combination of genetic algorithms and SA. In
(Ibrahim El-Amin et al., 1999), the tabu search meta-
heuristic is applied to the maintenance of generators
in a power station with the aim of reducing the cost
associated with the management of the maintenance
operations and to increase the time interval between
two maintenance operations for the same generator.
In our case a pure SA approach is exploited mainly
focusing on the overall cost of performing a set of ge-
ographically distributed maintenance operations dur-
ing a working day taking into account transportation
and overtime costs.
More generally, the SA metaheuristic and its vari-
ations are often used for the solution of optimiza-
tion problems in several application fields spanning
from ICT to biomedicine. In (Chun-Cheng Lin et al.,
2014), SA, combined with additional momentum
terms in order to improve cooling rate, is exploited to
solve the problem of router node placement with ser-
vice priority constraint to improve the performance of
a wireless mesh network. In (Allen G. Brown et al.,
2014), the SA algorithm is adopted for creating ma-
neuver plans for the guidance of a satellite cluster. In
a gene expression data matrix, a bicluster is a subma-
trix of genes and condition. The problem of detecting
the most significant bicluster has been shows to be
NP-Complete. In (Kenneth Bryan et al., 2006), the
authors present a biclustering technique based on SA
to efficiently discover the more significant biclusters.
In this paper, we use SA to solve a maintenance
operation scheduling problem. During problem for-
malization we do not take into consideration any spe-
cific application context. However, we show its ap-
plication to a real industrial use case dealing with the
maintenance of energy plants. We are interested in
routine maintenance operations, i.e., maintenance op-
erations that are not related to an actual failure of the
considered system but are scheduled in advance. We
start from the assumptions that a set of maintenance
operations are scheduled to be conducted in a specific
day and our goal is to optimize the maintenance team
routes and maximize the number of interventions that
are actually performed. Contrary to maintenance op-
erations upon failures, such routine operations can be
postponed if it is not possible to guarantee that all
the operations that are supposed to be conducted in
a day will be actually fulfilled. However, our algo-
rithm is also able to deal with maintenance operations
that need to be executed with a higher priority.
3 REFERENCE SCENARIO
We take into consideration a company that needs to
perform maintenance operations in a set of geograph-
ically distributed locations. We only deal with routine
maintenance interventions, i.e., interventions that are
scheduled in advance. However, our approach also
takes into account that some higher priority interven-
tions could be necessary, representing failures and/or
specific situations that need immediate attention. We
focus on the set of maintenance operations that need
to be performed in a single day by a limited set of
maintenance resources. The maintenance resources
are represented by a number of teams, each composed
of a set of company employees and one vehicle. The
teams leave from the company principle headquarters
in the morning, follow a specific route established in
advance, perform all the maintenance interventions
that they have been assigned to, and return to their
starting point. This kind of problems falls under the
class of scheduling problems.
The problem we need to solve is to assign the
maintenance operations that are supposed to be con-
ICEIS2015-17thInternationalConferenceonEnterpriseInformationSystems
536