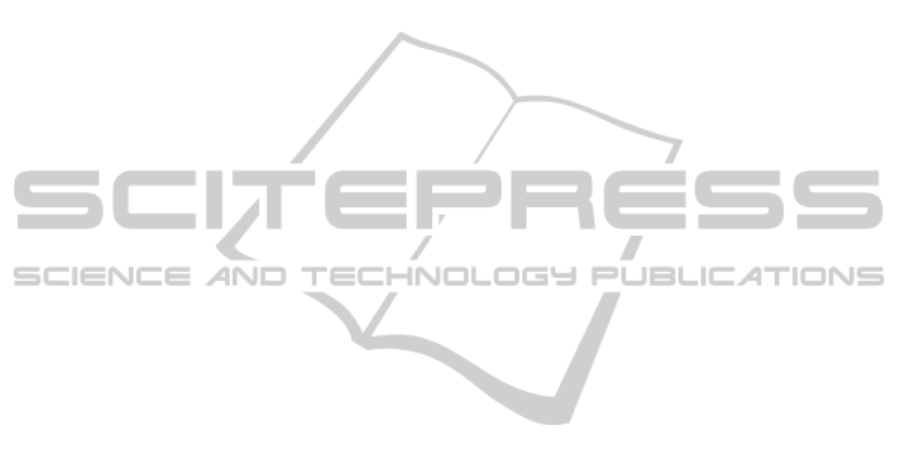
The above sequences can be applied in multiple
situations. The first one could be illustrated with a
simple situation taken from a manufacturing shop
floor environment, i.e., “after an accident/incident,
a what-if simulation of the manufacturing
environment can be done in order to understand
how the situation has been generated; verify if it has
been well managed and better organize shop floor
workplace and machineries configuration for the
future”. We could illustrate the second with a
warning in a production line. For instance “an over
threshold temperature of some components can be
acceptable allowing the system to continue working
(so remaining a warning without becoming an error)
if the system is used with some constraints like, for
example keeping a lower speed during execution.
The constraints will be determined during what-if
simulations and fed back to the system by
augmentation process”.
6 CONCLUDING REMARKS
The paper analysed the needs behind industry’s
digital transformation and how it can be capitalized
by implementing the sensing and liquid enterprise
concepts proposed by the FInES 2025 roadmap. The
paper presented the status quo of the modelling and
design of the OSMOSE liquid-sensing enterprise
vision, as well as the realisation on the osmosis
process and connected events and services.
The general modelling approach towards LSE
osmosis processes realisation has been provided and
MDSEA has been proposed. Due to the proximity of
some of the inner construct behind manufacturing
servitization design and LSE design, the model
driven approach could be adapted to facilitate the
transition between the traditional enterprise and the
future LSE. The realisation of the activities, events
handling, monitoring, recognition of osmosis, and
the reaction by osmosis processes, is currently
modelled at the MDSEA TIM level. Model
transformations are applied to semi-automatically
derive technology specific models and accommodate
the specific needs of every enterprise and reach an
actual software service that supports the LSE
osmosis.
Implementing the OSMOSE digital
transformation will provide companies the digital
capabilities to capitalize on the FI and IoT,
improving customer experience, operational process,
business models. Next steps target the osmosis
processes deployment into real pilots and further
study on how to integration CEP middleware with
the generated services is needed. Also governance
models need to be studied for a proper realization of
the LSE at the BSM level. Based on the feedback
received, the final version of the modelling approach
will be produced.
ACKNOWLEDGEMENTS
Authors would like to acknowledge the European
funded Projects MSEE (FP7 284860) and OSMOSE
(FP7 610905) that supported the development of
various ideas, concepts and use case presented.
REFERENCES
Agostinho, C., Bazoun, H., Zacharewicz, G., Ducq, Y.,
Boye, H. & Jardim-Goncalves, R. (2014) Information
Models and Transformation Principles applied to
Servitization of Manufacturing and Service Systems
Design. In: ModelsWard 2014.
Arsanjani, A. (2004) Service-oriented modeling and
architecture. IBM developer works, pp.1–15.
Arthur, W.B. (2011) The Second Economy. McKinsey
Quarterly. Available from: <www.mckinsey.com/
insights/strategy/the_second_economy>.
Baines, T.S., Lightfoot, H.W., Benedettini, O. & Kay,
J.M. (2009) The servitization of manufacturing: A
review of literature and reflection on future challenges.
Journal of Manufacturing Technology Management,
20 (5), pp.547–567.
Bazoun, H., Bouanan, Y., Zacharewicz, G., Ducq, Y. &
Boye, H. (2014) Business process simulation:
transformation of BPMN 2.0 to DEVS models (WIP).
In: DEVS ’14.
Chandy, K.M., Charpentier, M. & Capponi, A. (2007)
Towards a theory of events. In:DEBS ’07. NY,USA.
Chen, D., Doumeingts, G. & Vernadat, F. (2008)
Architectures for enterprise integration and
interoperability: Past, present and future. Computers in
Industry, 59 (7), pp.647–659.
Chesbrough, H. & Spohrer, J. (2006) A research manifesto
for services science. Communications of the ACM, 49
(7), p.35.
Doumeingts, G., Lieu, C., Chen, D., Ducq, Y., Alix, T.,
Zacharewicz, G., Bourrières, J.P., Vallespir, B.,
Jardim-Goncalves, R., Agostinho, C., Silva, E.M.,
Hirsch, M., Heller, M. & Friesen, A. (2012) MSEE
Deliverable D11.1: Service concepts, models and
method at CIM-PIM-PSM level. MSEE IP Project
(FP7 FoF-ICT 284860).
Ducq, Y., Agostinho, C., Chen, D., Zacharewicz, G. &
Jardim-Goncalves, R. (2014) Generic Methodology
for Service Engineering based on Service Modelling
and Model Transformation State of the art in model
driven approaches and model transformation. In: S.
MODELSWARD2015-3rdInternationalConferenceonModel-DrivenEngineeringandSoftwareDevelopment
616