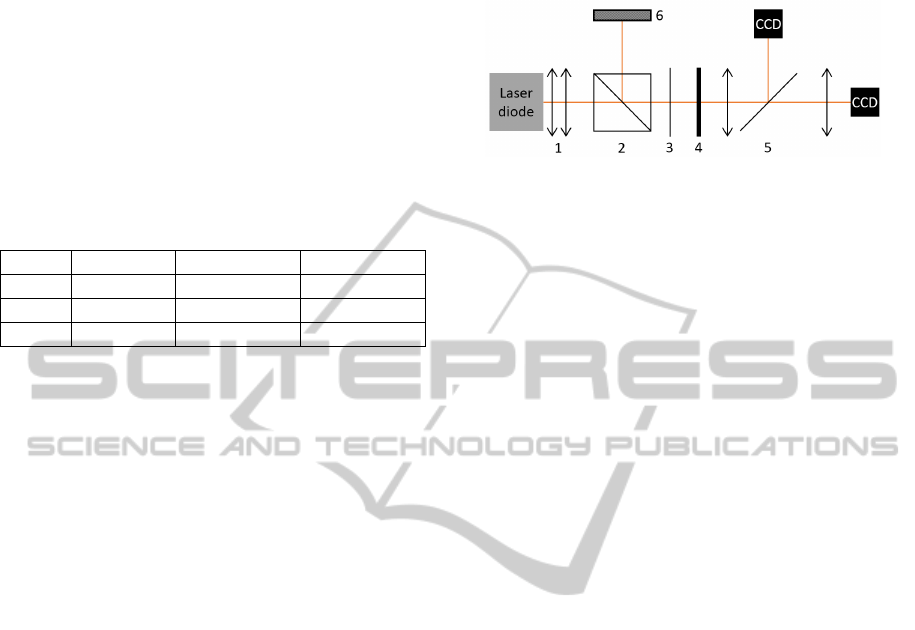
4.1 Laser Diodes
The used laser diodes are commercially available
components. They are mounted p-side down on a
passively cooled cooper heat sink. All laser diodes
used in experiments are checked in advance. This
includes visual inspection of front facet, recording of
optical power to current and voltage (PIV)
characteristics as well as spectral measurements and
near and far field intensity distributions. The
different types are listed in Table 1.
Table 1: Batches of test laser diodes.
Batch Material Wavelength Emitter No.
A AlGaAs 808 nm 19
B InGaAs 980 nm 10
C InGaAs 1010 nm 10
Laser diodes of batch A based on semiconductor
material containing aluminum and are well known
for susceptible behavior against optical feedback.
Laser diodes with InGaAs semiconductor are more
robust. Two versions with different wavelengths are
tested (batch C and D).
4.2 Detection of Failure Threshold
The threshold of device failure has to be identified to
derive design limits. Optical and electrical behavior
is observed to gather indicators connected to defined
feedback intensities.
4.2.1 Test Setup
The setup has to be suitable to measure and control
the amount of optical feedback reflected towards the
laser diode. The optical system has to be comparable
to commonly used designs for laser systems.
In Figure 1 the basic layout of the test system is
illustrated. The radiation of the laser diode is
collimated by cylindrical lenses in fast- and slow-
axis direction. An array of biconvex lenses rotates
the beam of each emitter geometrically by 90
degrees to achieve a more symmetric beam
parameter product. This component is part of the so
called beam transformation system (BTS). Note, that
the nomenclature of slow- and fast axis direction are
now inverted. The collimated beam is transmitted
through a polarization beam splitter and a quarter
wave plate. After reflection at a mirror the beam
passes the polarization optics again. Depending on
the angle of the wave plate, a part of the beam is
reflected at the beam splitter and hits on a power
measurement head. The remaining radiation is
transmitted towards the laser diode and focused via
the collimation lenses back onto the emitter.
Figure 1: Measurement setup with variable feedback
intensity and beam diagnostics. 1) collimation optics 2)
polarization beam splitter 3) wave plate 4) feedback mirror
5) beam splitter 6) power measurement head.
Closely behind the BTS two slit blades are
mounted to limit the transmitted radiation to a
defined number of emitters. This allows determining
the influence of optical feedback on a single or
multiple emitters.
The electrical properties of the laser diode are
monitored using a calibrated resistor together with a
voltmeter. Photodiodes are used to measure the
optical intensity. They are referenced to a
commercial power measurement head. An optical
imaging system is used to observe both, the near-
field intensity distribution of the emitter facet and
the far-field intensity distribution. A spectrometer
takes the spectrum of the laser beam.
This measurement setup is automated as the
quarter wave plate rotation is motorized and the
measured data are collected by data loggers and
software acquisition.
4.2.2 Procedure
The optical feedback beam is adjusted by
manipulating the angle of the reflection mirror. The
electrical and optical behavior of laser diodes with
optical feedback is used to find the optimal
alignment. Details to this behavior are given in
chapter 5.1. Several steps are necessary to optimize
the feedback injected into the laser emitter. First, the
laser diode is operated without the feedback mirror
and the centroid of the near-field intensity
distribution is marked. After adding the feedback
mirror the laser diode is operated below laser
threshold. The mirror angle is varied along slow axis
direction until the signal on the camera reaches its
maximum. This step uses the threshold reduction
effect due to optical feedback. In fast axis direction
the mirror is tilted until the intensity distribution
reaches the before marked position. Now the
threshold reduction current value can be determined.
Due to temperature expansion a slight
PHOTOPTICS2015-DoctoralConsortium
48