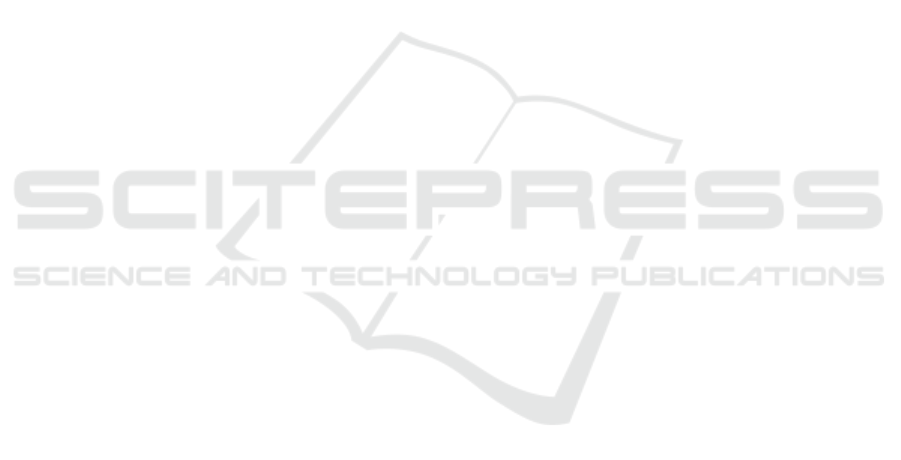
Analysis and Modeling of a Platform with Cantilever Beam using
SMA Actuator
Experimental Tests based on Computer Supported Education
Leandro Maciel Rodrigues
1
, Thamiles Rodrigues de Melo¹, Jaidilson Jó da Silva
2
, Angelo Perkusich
2
and José Sérgio da Rocha Neto
2
1
Post-Graduate in Electrical Engineering - PPgEE – COPELE, Campina Grande-PB, Brazil
2
Electrical Engineering Department (DEE), Federal University of Campina Grande, Aprígio Veloso Street, 882, Campina
Grande-PB, Brazil
Keywords: Modeling, Platform with Cantilever Beam, Shape Memory Alloy, Computer Supported Education.
Abstract: This paper presents a test platform with cantilever beam that uses a SMA (Shape Memory Alloy) as actuator
and strain gauges as sensors to study of the beam deformation. From the data acquired by means of heating
and cooling processes, the engineering students can observe the hysteresis behavior of the SMA wire.
Besides, the study of this platform provide to the students can put in practice their knowledge about data
acquisition, system identification, modeling and programming based on computer supported education.
1 INTRODUCTION
Mechanical systems, such as industrial machinery,
civil construction and transport vehicles are often
subject to internal and external excitations, which
result in undesirable vibrations, disturbing operators
and in some cases, putting at risk the structural
integrity of the system. This phenomenon has
mobilized a significant number of researchers and
there are numerous specialized publications in this
area (Li et al, 2014).
The vibration control of flexible structures has
been the subject of studies by many researchers.
According to these studies, the integrated use of
sensors, actuators and controllers would enable a
system to respond in a controlled manner to external
excitations, looking for the effects that would lead
the response amplitude levels to deviate from
acceptable levels (Schmidt, 2014).
Shape Memory Alloys (SMA) have been
considered as one of the most interesting smart
material systems, and they have great potential for
applications in modern active structures, mainly as
electrical or thermal actuators. Previously, strained
SMA actuators recover their original shape when
heated above a critical temperature. In the case of
SMA actuators type wire under uniaxial tensile
mechanical load, this shape recovery corresponds to
a contraction, and the actuator provides useful
external mechanical work (Nascimento et al, 2008).
Due to this phenomenon, the SMA can be used
as sensors and/or actuators in aerospace, oil and
automotive industries, in orthodontic, orthopedic and
robotic applications, or vibration and shape control.
When used as thermomechanical actuators, in which
heating is performed by Joule effect resulting from
the application of a certain intensity of current, SMA
become an attractive alternative due to its large
deformation and good recovery in systems where
great strengths, large deformation and low
frequencies are required (Lima et al, 2010), (Suzuki
and Kagawa, 2010).
Modeling is the process of obtaining equations or
graphs to represent, as closely as possible the
characteristics or behavior of a real system. The
importance of modeling real systems is evidence
when the results can be used to provide a better
understanding of the system (Ljung, 1999).
System identification is an alternative procedure
that aims to build a model to explain, at least in part
and approximately, the relationship of cause and
effect present in a database without the need for
prior knowledge of the physics of the process
(Ljung, 1999).
In this context, this work presents an
experimental methodology for engineering students
perform the modeling of a test platform with
238
Rodrigues L., Rodrigues de Melo T., Jó da Silva J., Perkusich A. and da Rocha Neto J..
Analysis and Modeling of a Platform with Cantilever Beam using SMA Actuator - Experimental Tests based on Computer Supported Education.
DOI: 10.5220/0005443902380243
In Proceedings of the 7th International Conference on Computer Supported Education (CSEDU-2015), pages 238-243
ISBN: 978-989-758-108-3
Copyright
c
2015 SCITEPRESS (Science and Technology Publications, Lda.)