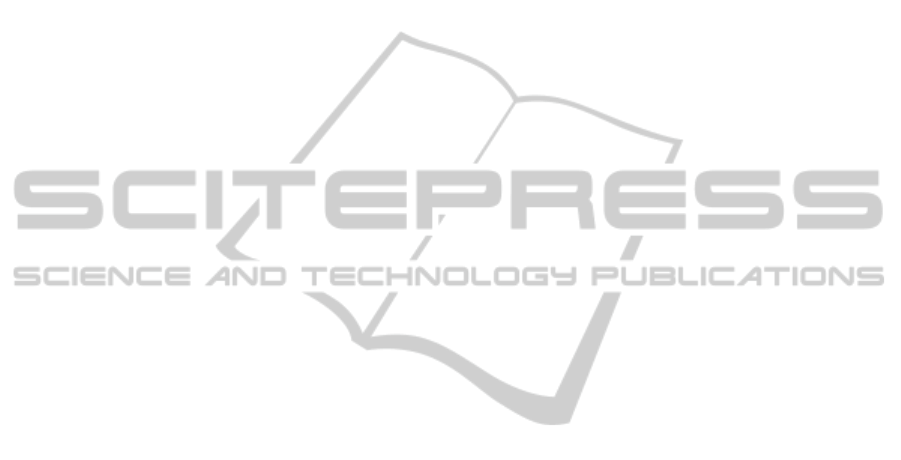
“Customer wants to mix liquid”. While placing the
sales order and the order items it is verified if
necessary ingredients are in stock. If not, they are
ordered from a supplier through a purchase system.
Afterwards a CPPS-Service for mixing liquids as a
Service is chosen by the customer or by the
employee (if customer doesn’t have the skills or
permissions). Depending on the chosen CPPS-
Service the business process on the one hand is
transferred to a business partner (if its own
organization cannot accept the sales order) and on
the other hand further processed in its own
organization. If the sales order is transferred to a
business partner this is registered and will lead to a
brokerage for the organization.
The further process steps inits own organization
are the scheduling for the manufacturing, the final
saving of sales order with an acknowledgment via
email and the start of the manufacturing process
when possible or desired. The two filling tanks are
first filled with the chosen ingredients of the order
item in the manufacturing process. The next step is
to mix these ingredients in the mixing tank and to
send notification to the customer when finished. In
the third step the mix liquid gets pumped to the final
holding tank. The last step is to fill the mixed liquid
out of the holding tank in chosen volumes per filling
(bottles etc.) of the order item and to send another
email to the customer when completed. After the
manufacturing process is finish the mixed liquid is
prepared for shipping to the customer.
5 CONCLUSIONS
Organizations are confronted with a rapidly
changing environment today in which relationship
management is more important than ever. By using
xRM concepts and xRM platforms an approach is
given to handle the increasing complexity. In future,
production services will also be able to
automatically allocate their sales orders among their
related industrial production units.
We predict that industrial production units will
independently configure themselves according to the
relations in the xRM. As an example the liquid
mixing service we have shown could have a third
filling tank added on the xRM platform. This would
create a task in the Smart Factory that ends up by
adding such a tank to the industrial production unit
and connecting it to the other modules. Vice versa,
adding a new tank cloud also automatically creates
the relationship in xRM.
Regardless of the data flow direction, xRM
platforms and their relationship networks will
become more and more important in the future.
ACKNOWLEDGEMENTS
The authors would like to thank the research
program of Karl Steinbuch of the MFG Innovation
Agency for ICT and Media for the financial support
of the research project “Ma-x-RM – Management
concept of Anything Relationship Management”.
REFERENCES
acatech, 2013. Recommendations for implementing the
strategic initiative INDUSTRIE 4.0. URL http://
www.forschungsunion.de/pdf/industrie_4_0_final_rep
ort.pdf, (accessed 10/10/2014).
Bradley, J., Barbier, J., Handle, D., 2013. Embracing the
Internet of Everything To Capture Your Share of $14.4
Trillion. URL: http://www.cisco.com/web/about/ac79/
docs/innov/IoE_Economy.pdf, (accessed 12/05/2014).
Britsch, J., Schacht, S., Mädche, A., 2012. Anything
Relationship Management. In: Business & Information
Systems Engineering : BISE (4:2), pp. 85-87.
Evans, D., 2011. The Internet of Things. How the Next
Evolution of the Internet Is Changing Everything,
Cisco. URL: https://www.cisco.com /web/about/ac79/
docs/innov/IoT_IBSG_0411F INA L.pdf (accessed:
09/03/2014).
Günter, B., Helm, S., 2006. Kundenwert. Grundlagen –
Innovative Konzepte – Praktische Umsetzungen.
Wiesbaden: Gabler Verlag.
Günthner, W., Hompel, M. (2010): Internet der Dinge in
der Intralogistik. Berlin, Heidelberg: Springer-Verlag
(VDI-Buch).
Knoblauch, J. P.; Bulander, R., 2014. Literature Review
and an Analysis of the State of the Market of Anything
Relationship Management (xRM) – xRM as an
Extension of Customer Relationship Management. In:
Proceedings of 11th International Conference on E-
Business and Telecommunications (ICE-B),
INSTICC, Wien, Austria, 28–30 August, 2014, pp.
236–244.
Martinez, C., 2012. Objective ICT-2013.1.4 - A reliable,
smart and secure Inter- net of Things for Smart Cities.
URL: http://www.oko-ist.cz/calls/ncp-infoday_12-06-
19/Obj_1_4.pdf (accessed: 10/12/2014).
Mertic, J., 2009. The Definitive Guide to SugarCRM -
Better Business Applications. USA: Apress.
Tiwana, A., Konsynski, B., Bush, A. A. 2010. Platform
evolution: coevolution of platform architecture,
governance, and environmental dynamics. Information
Systems Research 21 (4), pp. 675–687.
CLOSER2015-5thInternationalConferenceonCloudComputingandServicesScience
134