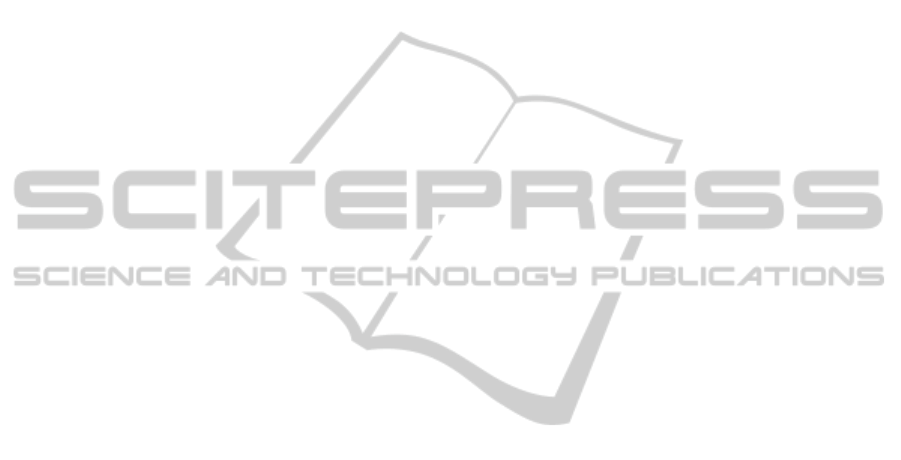
7 CONCLUSION AND FUTURE
WORK
In this paper we tried to model and solve the rout-
ing through an energy harvesting network, by formu-
lating multi-commodity flow problems. The multi-
commodity flow model can be used, along with its
slight variations, as a centralized routing scheme,
where the sink/central controller of the network de-
cides how the flow of data is going to be routed inside
the network, after getting all the information about
the residual energy at each of the nodes of the net-
work. We additionally proposed a distributed sea-
sonally aware scheme based on the concurrent multi-
commodity flow problem, which can run individually
at each node. All the techniques proposed, assume a
static network, where links between nodes are known
in advance.
For the future we would like to modify the multi-
commodity flow formulation so that it tries to op-
timize the residual energy in the nodes for use in
the next cycle, but with the added knowledge that it
distinguishes where this residual energy would bring
more benefit (i.e., at nodes adjacent to the sink). We
are currently working on prediction techniques for the
data, and in using adaptive duty cycling and energy-
neutral operation, from previous research works (Vig-
orito et al., 2007; Kansal et al., 2007), to achieve per-
petual operation of the nodes. Our primary goal now
is to implement a completely self–contained thermo-
electric harvesting node for in-wall use, using low
power microcontroller, and implementing these rout-
ing schemes with more realistic parameters (like the
inclusion of energy leakage etc.). Lastly we would
like to improve the seasonally aware routing scheme,
e.g., possibly by using machine learning techniques
and time series prediction models, to decide on the
split of flows and the amount of data sent, based on the
immediate neighborhood of the node (one hop away).
REFERENCES
Kansal, A., Hsu, J., Zahedi, S., and Srivastava, M. B.
(2007). Power management in energy harvesting sen-
sor networks. ACM Transactions on Embedded Com-
puting Systems (TECS), 6(4):32.
Kollias, A. and Nikolaidis, I. (2014). In-wall thermoelec-
tric harvesting for wireless sensor networks. In Pro-
ceedings of the 3rd International Conference on Smart
Grids and Green IT Systems, pages 213–221.
Li, W., Delicato, F. C., and Zomaya, A. Y. (2013).
Adaptive energy-efficient scheduling for hierarchical
wireless sensor networks. ACM Trans. Sen. Netw.,
9(3):33:133:34.
Li, X., Gul, M., Sharmin, T., Nikolaidis, I., and Al-Hussein,
M. (2014). A framework to monitor the integrated
multi-source space heating systems to improve the de-
sign of the control system. Energy and Buildings,
72(0):398 – 410.
Mara
ˇ
sevi
´
c, J., Stein, C., and Zussman, G. (2014). Max-min
fair rate allocation and routing in energy harvesting
networks: Algorithmic analysis. In Proceedings of the
15th ACM international symposium on Mobile ad hoc
networking and computing, pages 367–376. ACM.
Rizzon, L., Rossi, M., Passerone, R., and Brunelli, D.
(2013). Wireless sensor networks for environmental
monitoring powered by microprocessors heat dissipa-
tion. In Proceedings of the 1st International Work-
shop on Energy Neutral Sensing Systems, ENSSys
’13, page 8:18:6, New York, NY, USA. ACM.
Sadagopan, N. and Krishnamachari, B. (2005). Maximiz-
ing data extraction in energy-limited sensor networks.
International Journal of Distributed Sensor Networks,
1(1):123–147.
Sharma, V., Mukherji, U., Joseph, V., and Gupta, S.
(2010). Optimal energy management policies for en-
ergy harvesting sensor nodes. Wireless Communica-
tions, IEEE Transactions on, 9(4):1326–1336.
Sharmin, T., Gl, M., Li, X., Ganev, V., Nikolaidis, I.,
and Al-Hussein, M. (2014). Monitoring building en-
ergy consumption, thermal performance, and indoor
air quality in a cold climate region. Sustainable Cities
and Society, 13(0):57 – 68.
silabs.com (2014). Si106x-8x ultra-low power mcu with
integrated high-performance sub-1 ghz transceiver.
http://www.silabs.com/Support%20Documents/
TechnicalDocs/Si106x-8x.pdf. [Online; accessed July
2014].
Singh, S., Woo, M., and Raghavendra, C. S. (1998). Power-
aware routing in mobile ad hoc networks. In Proceed-
ings of the 4th annual ACM/IEEE international con-
ference on Mobile computing and networking, pages
181–190. ACM.
Vigorito, C. M., Ganesan, D., and Barto, A. G. (2007).
Adaptive control of duty cycling in energy-harvesting
wireless sensor networks. In Sensor, Mesh and Ad Hoc
Communications and Networks, 2007. SECON’07.
4th Annual IEEE Communications Society Confer-
ence on, pages 21–30. IEEE.
Yerva, L., Campbell, B., Bansal, A., Schmid, T., and Dutta,
P. (2012). Grafting energy-harvesting leaves onto the
sensornet tree. In Proceedings of the 11th interna-
tional conference on Information Processing in Sen-
sor Networks, pages 197–208. ACM.
SMARTGREENS2015-4thInternationalConferenceonSmartCitiesandGreenICTSystems
184