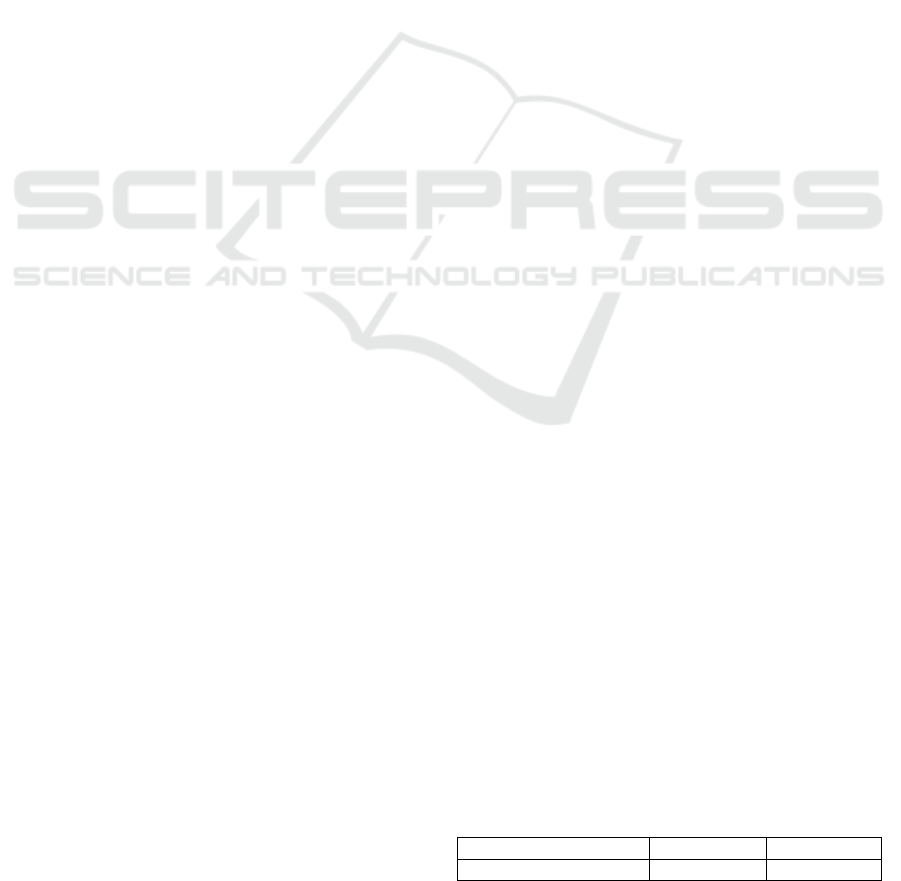
Fault Detection Architecture for Proprioceptive Sensors based on a
Multi Model Approach and Fuzzy Logic Decisions
Nicolas Pous
1
, Dominique Gruyer
2
and Denis Gingras
1
1
LIV (Laboratory of Intelligent Vehicles), in the Electrical and
Computer Engineering Department of Sherbrooke University, Sherbrooke, Qc J1K 2R1, Canada
2
IFSTTAR- IM - LIVIC, 14 route de la minière, bat. 824, 78000 Versailles-Satory, France
Keywords: Failure Detection, Intelligent Vehicle, Localization, Data Fusion.
Abstract: In this paper a new fault detection architecture will be presented. Inspired by multi-model data fusion
algorithms and fuzzy logic decisions, it consists in the comparison between the estimation of a dynamic mode
using each sensor independently. This method is used to deal with important non-linearity and strong
interaction with the environment usually encountered in the domain of the intelligent vehicles localization.
The concept of analytic redundancy is also used to ignore model uncertainties.
1 INTRODUCTION
More and more, our society is evolving to be partially
automatized. In this context, the automotive industry
is contributing by focusing on autonomous vehicles.
As a step between this technology and the previous
one, vehicular companies are developing a large
series of tools helping drivers and improving both
safety and comfort. These tools, when used to
improve driving safety, are generally named ADAS
(Advance Driver Assistance System) (Andreas
Riener, 2009). ADAS are generally composed of a
large amount of tools permitting, for example, to
reduce stopping distance, or improve the car position
determination. In that case precisely, a large set of
exteroceptive and proprioceptive sensors are used to
obtain a better knowledge of the vehicle environment
and attitude, in order to reduce the localization
uncertainties via data fusion algorithms. Some of
them are using only proprioceptive sensors (Cai Bai-
gen et al., 2009), others are using both (Kim, S.-B et
al., 2011 and Adrien Bak et al., 2012).
Communication and map matching can also be used
to reinforce the precision of the measurement (Rohani
et al., 2013 and Rohani et al., 2014).
In both cases, a faulty data source can lead to a
catastrophic error in the position determination.
That’s why, in order to properly improve safety, we
need to detect faults and identify the associated
sources before using faulty data in the fusion
algorithm. One of the most used detection method is
based on the comparison between the normal
behavior model and the recording of the real behavior
from the sensors. This method supposed that the
system behavior is perfectly known and can be
modeled (Patton, R. J. et al., 1989).
But, the important non-linearity of our system (The
vehicle) behavior and the strong impact of
environmental perturbation will improve the
complexity of our task. Others methods based on
analytical redundancy are also used to avoid the
model issues, as described in (Sun and Cannon,
1998), where a Kalman filter is used to obtain
estimations of a same metric in order to compare the
values obtained from different sensors.
In this paper an alternative approach based on the
determination of the dynamic comportment of the
vehicle using analytical redundancy is developed in
order to treat with the non-linearity of the system. The
nominal comportment was divided in 4 sub-systems
defined by the direction changes and longitudinal
accelerations as describe in table 1.
Table 1: Dynamic modes definition.
Straight line H1 H3
Speed change H2 H4
Based on the sensors information, we will use fuzzy
logic and calculate the weight corresponding to the
membership degree of each dynamic mode in every
time, and use these values from each sensor to
determine the presence of a faulty data source.
25
Pous N., Gruyer D. and Gingras D..
Fault Detection Architecture for Proprioceptive Sensors based on a Multi Model Approach and Fuzzy Logic Decisions.
DOI: 10.5220/0005459700250032
In Proceedings of the 1st International Conference on Vehicle Technology and Intelligent Transport Systems (VEHITS-2015), pages 25-32
ISBN: 978-989-758-109-0
Copyright
c
2015 SCITEPRESS (Science and Technology Publications, Lda.)