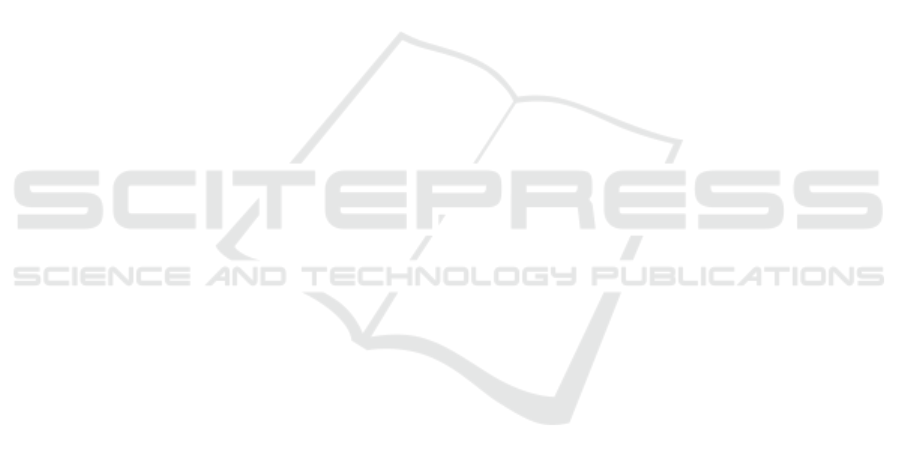
A Model Predictive Sliding Mode Control with Integral Action for
Slip Suppression of Electric Vehicles
Tohru Kawabe
Faculty of Engineering, Information and Systems, University of Tsukuba, Tsukuba 305-8573, Japan
Keywords:
Electric Vehicle, Slip Ratio, Robustness, Sliding Mode Control, Model Predictive Control.
Abstract:
This paper proposes a new SMC (Sliding Mode Control) method with MPC (Model Predictive Control) al-
gorithm for the slip suppression of EVs (Electric Vehicles). This method introducing the integral term with
standard SMC gain, where the integral gain is optimized for each control period by solving an optimization
problem based on the MPC algorithm to improve the acceleration performance and the energy consumption
of EVs. Numerical simulation results are also included to demonstrate the effectiveness of the method.
1 INTRODUCTION
Over the past decades, the automobile population has
been increasing rapidly in the developing countries,
such as BRICs (Brazil, Russia, India and China) (Dar-
gay et al., 2007). With the wide spread of automobiles
all over the world, especially internal-combustion en-
gine vehicles (ICEVs), the environment and energy
problems: air pollution, global warming, oil resource
exhaustion and so on, are going severely (Mamalis
et al., 2013). As a countermeasure to these prob-
lems, the development of next-generation vehicles
have been focused. EVs run on electricity only and
they are zero emission and eco-friendly. So EVs have
attracted great interests as a powerful solution against
the problems mentioned above (Brown et al., 2010;
Hirota et al., 2011; Tseng et al., 2013).
EVs are propelled by electric motors, using elec-
trical energy stored in batteries or another energy stor-
age devices. Electric motors have several advantages
over ICEs (Internal-Combustion Engines):
• The input/output response is faster than for gaso-
line/diesel engines.
• The torque generated in the wheels can be de-
tected relatively accurately
• Vehicles can be made smaller by using multiple
motors placed closer to the wheels.
The travel distance per charge for EV has been in-
creased through battery improvements and using re-
generation brakes, and attention has been focused on
improving motor performance. The above-mentioned
facts are viewed as relatively easy ways to improve
maneuverability and stability of EVs.
It’s, therefore, important to research and develop-
ment to achieve high-performance EV traction con-
trol. Several methods have been proposed for the
traction control (Fujii and Fujimoto, 2007) by us-
ing slip ratio of EVs, such as the method based
on MFC (Model Following Control) in (Hori, 2000)
We have been proposed MP-PID (Model Predictive
Proportional-Integral-Derivative) method in (Kawabe
et al., 2011) and MP-2DOF-PID method in (Kawabe,
2014).
These methods show good performances under
the nominal conditions where the situations, for ex-
ample, mass of vehicle, road condition, and so on,
are not changed. To meet the high performance even
variation happened in such conditions, it is signifi-
cant to construct the robust control systems against
the changing of situation. About this point, SMC per-
forms good robustness against the uncertainties and
nonlinearities of the systems.
However, for slip suppression with the conven-
tional SMC (Slotine and Li, 1991; Eker and Aki-
nal, 2008) , the control performance will get degrada-
tion due to the chattering which always occurs when
switching the control inputs due to the structure of
SMC. To overcome such disadvantages, the SMC
method introducing the integral action with gain to
design the sliding surface (SMC-I) has been proposed
in (Li and Kawabe, 2013), where the integral gain
is derived by trial and error. In order to get better
control performance and save more energy for slip
suppression of EVs with changing the mass of vehi-
151
Kawabe T..
A Model Predictive Sliding Mode Control with Integral Action for Slip Suppression of Electric Vehicles.
DOI: 10.5220/0005500401510158
In Proceedings of the 12th International Conference on Informatics in Control, Automation and Robotics (ICINCO-2015), pages 151-158
ISBN: 978-989-758-123-6
Copyright
c
2015 SCITEPRESS (Science and Technology Publications, Lda.)