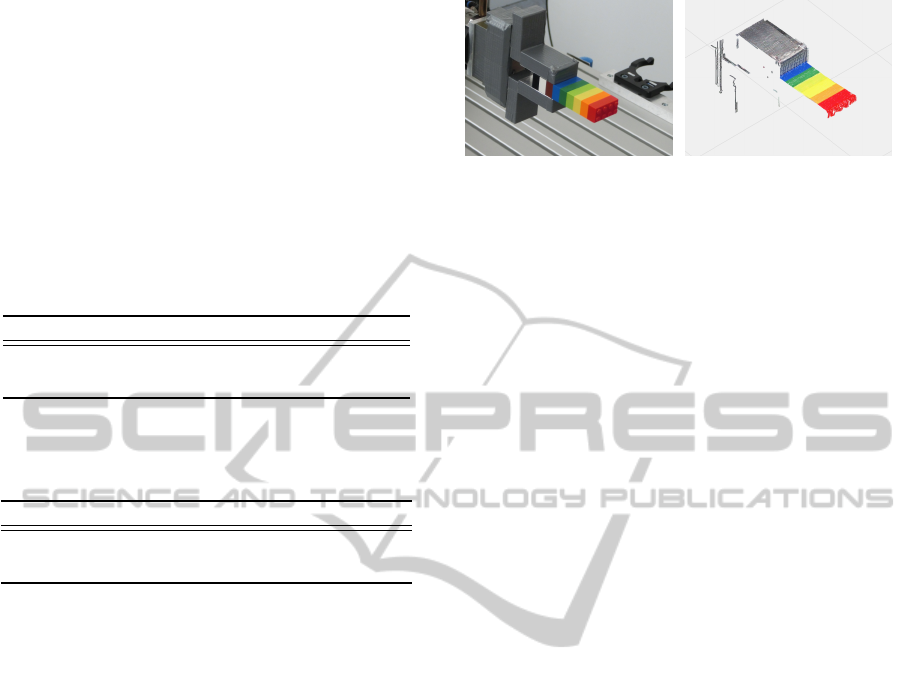
have been performed. The first set-up is shown in Fig-
ure 5 and in the second set-up the camera is mounted
as close as possible to the profile sensor. Thereby, ei-
ther two, five or ten object positions scattered inside
of the reference areas were used. However, an in-
creased number of reference points has no significant
influence on the results. Thus, a number of N = 4 ref-
erence points is sufficient. The resulting mean values
and the standard deviation values for each parameter
are shown in Table 1 and 2.
Table 1: Parameter estimation for first experimental
set-up.
t (mm) σ (mm) r (deg) σ (deg) Error (pixel) σ (pixel)
72.3995 0.8716 34.4061 0.1101
80.1886 0.3726 -22.9854 0.2741 0.9349 0.1891
20.5744 0.4808 -3.4034 0.1325
Table 2: Parameter estimation for second experimen-
tal set-up.
t (mm) σ (mm) r (deg) σ (deg) Error (pixel) σ (pixel)
1.9726 0.0445 -9.2074 0.0310
-32.7163 0.1503 -5.9926 0.0370 0.8696 0.0721
-18.5722 0.3498 -89.2548 0.0621
The realized approach achieves stable solutions
and consequently a good repeatability. The validation
shows low standard deviation values for the transfor-
mations (σ < 1mm, σ < 0.3
◦
). A good absolute accu-
racy is also achieved with average pixel errors below
the resolution of the camera (1 pixel). This error oc-
curs partially by rounding errors that can hardly be
avoided.
The calibrated sensors are used for workpiece
scanning with two robot arms (cf. Section 2.1). Fig-
ure 9 shows a partial reconstruction of some Lego
bricks held up by a gripper. Due to the contained color
information, it can be clearly distinguished between
the individual bricks and the gripper.
5 CONCLUSIONS
In this paper, a color extension for a 2D laser profile
sensor by getting the color information from a cam-
era is presented. For this purpose, a sensor fusion be-
tween the two sensors has been realized. Therefore,
a flexible calibration routine has been created. Indefi-
nite planar calibration objects are usable with this ap-
proach regardless of their color. The accuracy of the
approach is confirmed through experiments. A pixel
error close to the resolution of the camera has been
achieved.
(a) Scene (b) Point cloud
Figure 9: Example for a colored reconstruction.
So far, the coloring needs approximately 4 ms per
profile point. Future work will be focused on the time
optimization of the process. In addition, an improve-
ment of the reference point distribution, by splitting
the profile sensor measurement range in sections and
a partial restriction on one reference point per section,
is prospected.
REFERENCES
Borangiu, T. and Dumitrache, A. (2010). Robot arms with
3d vision capabilities. In Advances in Robot Manipu-
lator, Vukovar, Croatia. InTech.
Cobzas, D., Zhang, H., and Jagersand, M. (2002). A
comparative analysis of geometric and image-based
volumetric and intensity data registration algorithms.
In Proceedings of the International Conference on
Robotics and Automation, volume 3, Washington, DC,
USA. IEEE.
G. Li, L. D., Pan, L., and Henghai, F. (2009). The cali-
bration algorithm of a 3d color measurement system
based on the line feature.
Garcia-Alegre, M. C., Martin, D., Guinea, D. M., and
Guinea, D. (2011). Real-time fusion of visual images
and laser data images for safe navigation in outdoor
environments. In Sensor Fusion - Foundation and Ap-
plications, Vukovar, Croatia. InTech.
Klimentjew, D., Hendrich, N., and Zhang, J. (2010). Multi
sensor fusion of camera and 3d laser range finder for
object recognition. In Proceedings of the Conference
on Multisensor Fusion and Integration for Intelligent
Systems, Salt Lake City, UT, USA. IEEE.
Larsson, S. and Kjellander, J. (2006). Motion control and
data capturing for laser scanning with an industrial
robot. In Robotics and Autonomous Systems, vol-
ume 54, Amsterdam, Netherlands. Elsevier B.V.
Li, J., Chen, M., Jin, X., Xuebi, C., Yu, D., Z.Dai, Ou, Z.,
and Tang, Q. (2011). Calibration of a multiple axes 3-
d laser scanning system consisting of robot, portable
laser scanner and turntable. In Optik - International
Journal for Light and Electron Optics, volume 122,
Amsterdam, Netherlands. Elsevier B.V.
Mei, C. and Rives, P. (2006). Calibration between a cen-
tral catadioptric camera and a laser range finder for
robotic applications. In Proceedings of the Interna-
tional Conference on Robotics and Automation, Or-
lando, FL, USA. IEEE.
ICINCO2015-12thInternationalConferenceonInformaticsinControl,AutomationandRobotics
164