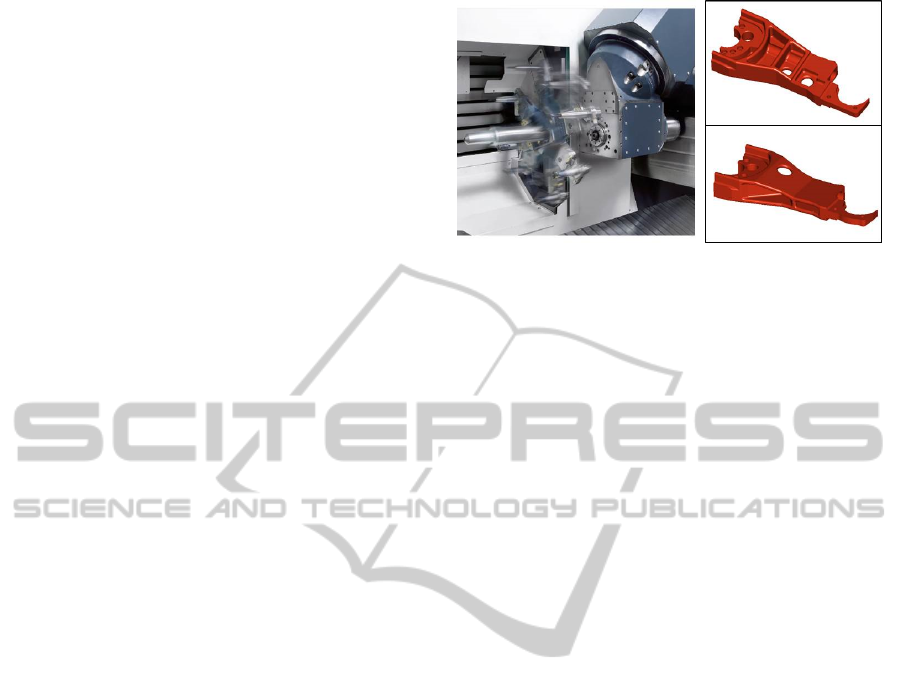
costs (including staff for analysis and design,
software, hardware, equipment costs) were assumed.
This can be compared with a material cost reduction
of € 47 per grinding machine. Surprisingly, the
energy savings due to reduced mass moment of
inertia is calculated as less than € 1, despite taking
10 years of operation into account. One reason for
that is, that the inertia of the drive itself is a multiple
of the inertia of the optimised tool magazine.
Nevertheless, this measure makes sense
economically from a quantity of twelve units, even if
the payback time due to lack of relevance for chip-
to-chip time clearly occurs later, compared to double
gripper arm of the tool changer. It is still
indisputable, based on the planned sales, that this
optimisation is the right decision from an
entrepreneurial point of view (Schietinger, 2014).
8 DOUBLE GRIPPER ARM OF A
TOOL CHANGER FOR A
MACHINE CENTRE
The double gripper arm in Figure 6 provides the
automated exchange of cutting tools between a tool
magazine and spindle within a machining centre, via
rapid linear and rotary movements. The machine by
Gebr. Heller Maschinenfabrik GmbH (HELLER
MCH 280C) can handle very heavy tools of up to 35
kg during a tool change and reaches a chip-to-chip
time of approximately 6.8 seconds.
The aim was to investigate how to further reduce
the chip-to-chip time, but above all to increase the
reliability of the tool change, so that jamming of
tools in the spindle or in the tool supply position is
ruled out under all operating conditions.
Therefore, a topology optimisation of the
geometry has been applied with cyclic symmetry (2
x 180°), so that only the half models of the double
gripper arm are shown. 3D models were considered,
since in addition to the already known load cases of
gravitational force and rotational movement, there
are also significant extraction forces from the tool
interface of the clamping system. These forces apply
in axial direction of the tool and are therefore out of
plane.
As a result of the topology optimisation and
redesign, the component on the bottom right of
Figure 6 shows increased stiffness-to-mass ratio of
21% for typical operating loads compared to the
original component (top right). Additionally, there
was a 19% increase in fatigue resistance, thus
increasing the reliability of the tool change.
Figure 6: Double gripper arm: Function and half models of
the original / optimised component.
9 CONCLUSIONS
Rotational motion components in machine tools
often occur in automation solutions for tools and
work piece flow. Systematic topology optimisation
is a way to improve their technical and economic
characteristics. However, they have to be justified as
economical business decisions in advance. A means
for this is the consideration of the amortisation of
topology optimisations. This can occur at different
unit numbers for various components due to the
influence of cost types. Experience has shown that
the optimisation of components for reduced primary
processing times, secondary processing times, and
set-up times often turns out to be commercially
successful, even in small quantities.
REFERENCES
Klein, B., 2013. Leichtbau-Konstruktionen. Springer
Vieweg-Verlag Wiesbaden.
Brandenberger, M., Kehl, G., 2004. Coupled Simulation
using FEM, MBS and Control Simulation Tools using
the Example of a Machine Tool. In: Proceedings of the
NAFEMS Seminar Mechatronics in Structural
Analysis, Wiesbaden.
Keller, K., Kehl, G., 2006. Coupled FE Analysis of
Structure and Control of High Dynamic Machine
Tools considering the Machining Centre HELLER
MCH 250 as an Example. In: Proceedings of the
PERMAS Users Conference, Strasbourg.
Schumacher, A., 2005. Optimierung mechanischer
Strukturen – Grundlagen und industrielle
Anwendungen. Springer-Verlag Berlin Heidelberg.
Schumacher, A., Ortmann, C., 2011. Topology
Optimization – Research State of the Art. Proceeding
of the Automotive CAE Grand Challenge 2011,
Hanau.
TopologyOptimisationofRotatingAutomationComponentsforMachineTools-Methodology,CostEffectivenessand
Examples
445