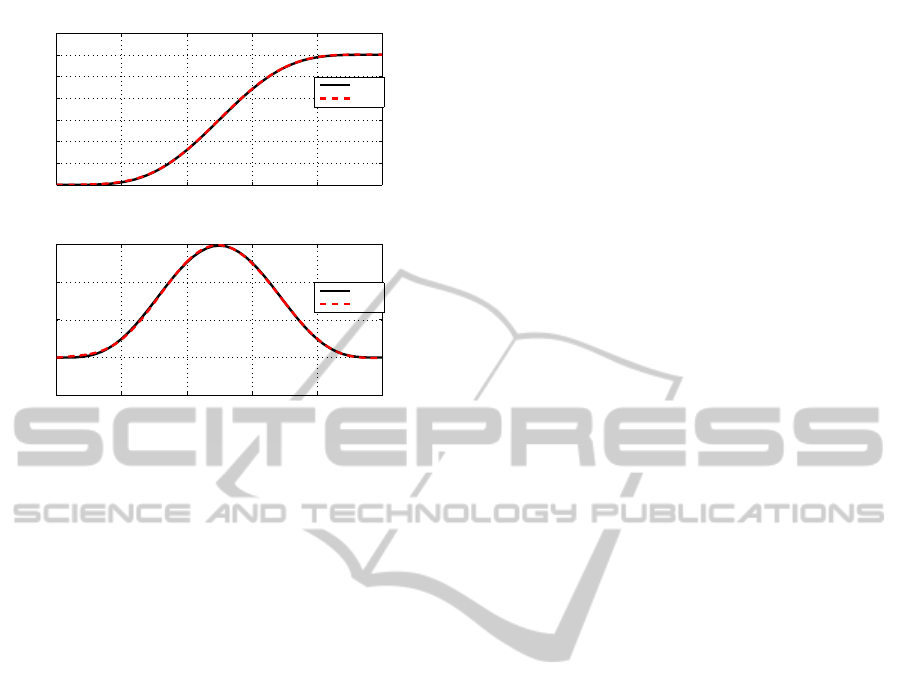
0 0.2 0.4 0.6 0.8 1
0
0.01
0.02
0.03
0.04
0.05
0.06
0.07
Time [s]
Radians
y
ref
actual
0 0.2 0.4 0.6 0.8 1
−0.05
0
0.05
0.1
0.15
Time [s]
Rads/s
˙y
ref
actual
Figure 10: Trajectories driven by flatness based feedfor-
ward control.
6 CONCLUSION
The feedforward control for the single link flexible
joint robot arm under the influence of gravity and fric-
tional effects is solved using differential flatness the-
ory. The control was accomplished for point to point
position movements in finite time. The technique
does not require any solution of differential equations
despite the highly nonlinear dynamics of the robot.
The proposed control has great potential for carrying
out fast and precise point to point movements with-
out any oscillations for the flexible robot arm. The
proposed approach can be extended to the case of
multi-link robot control where elasticity is considered
at each joint and the effects of gravity taken into ac-
count. This will be studied in future works.
REFERENCES
Anene, E. (2007). Flat control of a synchronous machine.
Unpublished Thesis.
Bauer, D., Schaper, U., Schneider, K., and Sawodny, O.
(2014). Observer design and flatness-based feedfor-
ward control with model predictive trajectory plan-
ning of a crane rotator. In American Control Confer-
ence (ACC), 2014, pages 4020–4025. IEEE.
Cambera, J. C., Chocoteco, J. A., and Feliu, V.
(2014). Feedback linearizing controller for a flexi-
ble single-link arm under gravity and joint friction.
In ROBOT2013 First Iberian Robotics Conference,
pages 169–184. Springer.
De Vries, E., Fehn, A., and Rixen, D. (2010). Flatness-
based model inverse for feed-forward braking control.
Vehicle System Dynamics, 48(S1):353–372.
Dwivedy, S. and Eberhard, P. (2006). Dynamic analysis of
flexible manipulators, a literature review. Mechanism
and Machine Theory, 41(7):749–777.
Fliess, M., Levine, J., Martin, P., Ollivier, F., and Rouchon,
P. (1997). Controlling nonlinear systems by flatness.
Systems and Control in the Twenty-first Century, page
137154.
Fliess, M., Levine, J., Martin, P., and Rouchon, P. (1999). A
lie-backlund approach to equivalence and flatness of
nonlinear systems. Automatic Control, IEEE Transac-
tions on, 44(5):922–937.
Hagenmeyer, V. and Delaleau, E. (2003). Exact feedfor-
ward linearization based on differential flatness. In-
ternational Journal of Control, 76(6):537–556.
Ider, S. and zgren, M. (2000). Trajectory tracking control
of flexible-joint robots. Computers and Structures,
76(6):757–763.
Jiang, Z. and Higaki, S. (2011). Control of flexible joint
robot manipulators using a combined controller with
neural network and linear regulator. Proceedings of
the Institution of Mechanical Engineers, Part I: Jour-
nal of Systems and Control Engineering, 225(6):798–
806.
Kandroodi, M., Mansouri, M., Shoorehdeli, M., and Tesh-
nehlab, M. (2012). Control of flexible joint manipu-
lator via reduced rule-based fuzzy control with exper-
imental validation. International Scholarly Research
Network ISRN Artificial Intelligence.
Kharitonov, A. and Sawodny, O. (2006). Flatness-based
feedforward control for parabolic distributed param-
eter systems with distributed control. International
Journal of Control, 79(07):677–687.
Kotman, P., Bitzer, M., and Kugi, A. (2010). Flatness-based
feedforward control of a two-stage turbocharged
diesel air system with egr. In Control Applica-
tions (CCA), 2010 IEEE International Conference on,
pages 979–984. IEEE.
Levine, J. (2006). On necessary and sufficient conditions
for differential flatness. Arxiv preprint math/0605405.
Levine, J. (2009). Analysis and control of nonlinear sys-
tems: A flatness-based approach. Springer.
Markus, E., Agee, J., and Jimoh, A. (2013). Differentially
flat trajectory control of a 6dof industrial robot manip-
ulator. In International Association for Science and
Technology (IASTED)Control and Application confer-
ence, pages 215–221. Iasted.
Markus, E., Agee, J., Jimoh, A., and Tlale, N. (2012a).
Nonlinear control of a single-link flexible joint ma-
nipulator using differential flatness. In Robotics and
Mechatronics Conference (ROBMECH). IEEE.
Markus, E., Agee, J., Jimoh, A., Tlale, N., and Zafer, B.
(2012b). Flatness based control of a 2 dof single
link flexible joint manipulator. In 2nd International
Conferenceon Simulation and Modeling Methodolo-
gies, Technologies and Applications, pages 437–442.
SciTePress.
FlatnessbasedFeed-forwardControlofaFlexibleRobotArmunderGravityandJointFriction
179