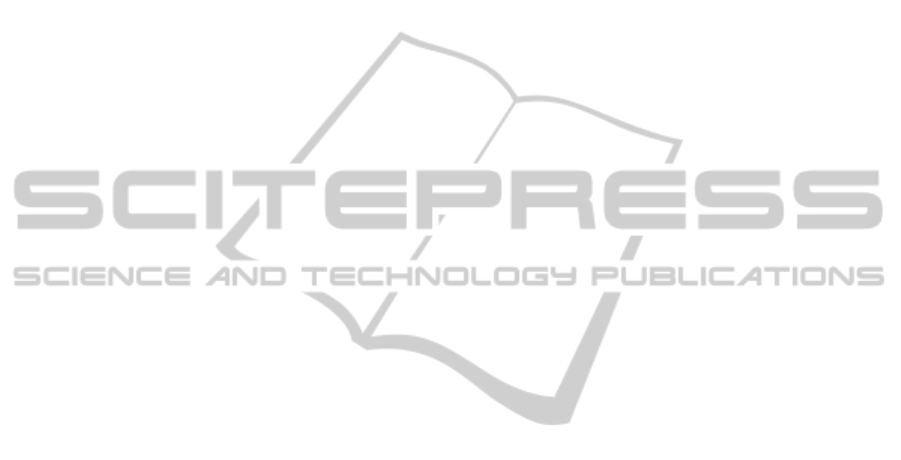
complex eigenvalue, the damping coefficient ζ
i
and
the natural frequency ω
n
i
of the i−th mode.
Furthermore, this choice for the viscous damping
has also the following implications: it does not affect
the mode shapes that are the eigenvectors (ψ
i
∈ C
n
)
of the matrix M
−1
K; the mode shapes are real and or-
thonormal; each mode shape is described by a stand-
ing wave that contains fixed stationary node points.
In contrast, if the matrix D is not representative of a
proportional damping, the mode shape are complex
valued and results in modes, which are described as
complex modes, having different characteristics; each
mode shape is described by a travelling wave and ap-
pears to contain a moving node point on the struc-
ture; in such a case, the mode shape from the un-
damped case does not diagonalise the damping matrix
D. Since in the typical case of experimental modal
analysis the available data are Frequency Response
Functions (FRFs), also the relations between the gray-
box model and the FRFs data are useful. In particu-
lar, applying the Fourier transform, the frequency re-
sponse matrix corresponding to the model (5)–(6), is
symmetric and has the form
G( jω) = UΦ( jω)U
T
(8)
with Φ( jω) = diag{φ
1
( jω),. .. , φ
n
( jω)} and
φ
l
( jω) = jω/(ω
2
n
l
− ω
2
+ j2ζ
l
ω
n
l
ω), l = 1,. .., n
and thus for an applied force at a spatial position k
(as input) and a velocity measurement at a spatial
position h (as output), the FRF g
hk
( jω) in physical
coordinates is
g
hk
( jω) =
n
∑
l=1
φ
l
( jω)ψ
h
l
ψ
k
l
(9)
where ψ
h
l
is the h-th column of the matrix U of the
mode shape corresponding to the l-th mode.
3 MODAL PARAMETERS
ESTIMATION
The objective of experimental modal analysis (Ewins,
1984) is to derive natural frequencies and damping
coefficients as well as mode shapes. In the proposed
approach, the unknown parameters to identify are ex-
plicitly present in the gray-box model reported in
Eqs. (5)–(6) and used in the identification procedure.
Note that if the number of excitation inputs is differ-
ent from the number of measured outputs, the selec-
tion matrix in Eq. (5) is different from the one in the
Eq. (6). In particular, if the number of inputs is equal
to m and the number of outputs is p (p > m is the typi-
cal case of experimental modal analysis) the gray-box
model can be rewritten as
˙x =
0 I
−Ω −Λ
x+
0
B
2
u (10)
y =
0 C
2
x (11)
where Λ,Ω ∈ R
n×n
, B
2
∈ R
n×m
and C
2
∈ R
p×n
have
to be estimated. With this choice, the rows of B
2
represent spatial samples of the mode shapes corre-
sponding to excitation points, while the columns of
C
2
represent spatial samples of the mode shapes cor-
responding to measurement points.
All the parameters to be identified for the
model (10)–(11) can be estimated by using the pro-
cedure detailed by the same authors in (Cavallo et al.,
2007). The only choices that the user has to do, as dis-
cussed in the introduction, are: to select the frequency
range in which to perform the identification and to fix
the number of modes to identify.
The selection of the working frequency range
[ f
1
, f
2
]Hz, in which to extract the modes of interest,
has to take into account that the real system is infi-
nite dimensional. In fact, for flexible structures the
FRFs in a given frequency range depend not only on
the modes with natural frequencies within the con-
sidered range but also on the lower and higher fre-
quency modes. This means that near the extremes
of the range the experimental data are not sufficient
for an accurate identification of modal parameters and
thus the FRFs should be measured on a working fre-
quency range [ f
′
1
, f
′
2
]Hz wider than the interesting one
[ f
′
1
, f
′
2
] ⊃ [ f
1
, f
2
]. Fixed the frequency range, denote
with G
i
∈ C
p×m
, i = 1, .. .,M the experimentalmea-
sured samples of the frequency response matrix in the
frequency range [ f
′
1
, f
′
2
]Hz (not necessarily uniformly
spaced). The choice of M depends on the modal
density of the flexible structure and obviously on the
width of the frequency range of interest. The num-
ber of the modes to be identified (n) can be fixed on
the basis of a classical indicator used in experimental
modal analysis (Ewins, 1984), i.e.
H(ω
i
) =
p
∑
h=1
m
∑
k=1
|g
hk
( jω
i
)|, i = 1,. .., M (12)
by counting (approximately and lightly overestimat-
ing) its number of peaks by simple inspection.
By following the procedure in (Cavallo et al.,
2007), in a first step, the M measured samples of the
FRFs are used to construct the matrices detailed in
the cited paper, from which, via a subspace identifica-
tion technique, the eigenvalues of the dynamic matrix
A are estimated. At the end of this step, the n fixed
modes are completely estimated in terms of natural
frequencies and damping ratios. The second stage
consists in determining an estimate of B
2
and C
2
. In
ExperimentalModalAnalysisbasedonaGray-boxModelofFlexibleStructures
441