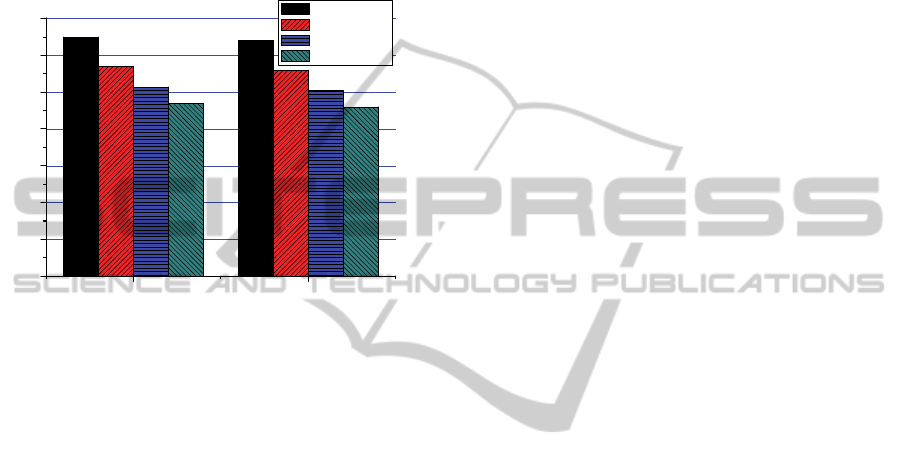
peak pressure under different experimental
conditions. As is shown in the Fig, the water hammer
peak pressure in experiment 1 is the highest, and it
reduces in experiment 2, 3 and 4 in turn, the water
hammer peak pressure in experiment 4 is the lowest.
There is no significant different between the
simulation calculation data and real experimental
data under different experiment. The data
consistency is good.
12
0.0
0.5
1.0
1.5
2.0
2.5
3.0
3.5
Real Experiment
Pressure (MPa)
Simulation Calculation
Experiment 1
Experiment 2
Experiment 3
Experiment 4
Figure 6: Comparison of water hammer peak pressure
under different experimental conditions.
As is shown in Fig.6, contrasting experiment 2 and
experiment 1, the water hammer peak pressure
reduces from 3.25MPa to 2.85Mpa, and it is reduced
by 12.3% compared with the data in experiment 1.
Contrasting experiment 3 and experiment 1, the water
hammer peak pressure reduces from 3.25MPa to
2.57Mpa, and it is reduced by 20.9% compared with
the data in experiment 1. Contrasting experiment 4
and experiment 1, the water hammer peak pressure
reduces from 3.25MPa to 2.35Mpa, and it is reduced
by 27.7% compared with the data in experiment 1.
From the experimental results we can know that it
can effectively reduce the water hammer effect of
the filling pipeline by adopting the schemes
proposed in this paper.
Through data analysis for the simulation
calculation data and real experimental data, it
provides theoretical basis and data support for
reducing water hammer effect of the filling system
and optimizing filling process.
5 CONCLUSIONS
The rocket filling system is an important part of the
spaceflight launch site, the filling pipeline is one of
the key components in the filling system. Accurately
grasp it’s work state in the rocket propellant filling
process is very important for the filling accuracy and
the security and reliability of the system.
This paper analyzes the water hammer effect of
the rocket propellant filling pipeline during the
filling process of the spaceflight launch site, and
studies the influence of filling process on water
hammer. It researches the pressure change law of
filling pipeline when water hammer occurs. In order
to reduce the water hammer effect of the filling
pipeline, improved scheme in the aspects of filling
control process is put forward as follows: change the
closed sequential of the related valve, reduce the
speed of the filling pump, and augment the opening
of the electric control valve. Meanwhile, simulation
calculation and real experiment are carried through
in allusion to the proposed scheme, and carries
through data analysis for the simulation and
experimental results. The experimental results show
that the proposed scheme can effectively reduce the
water hammer effect of the pipeline during the filling
process, reduce the error of filling quantity caused by
water hammer, improve the rocket propellant filling
accuracy and enhance the security and reliability of
the system.
The water hammer effect of the rocket propellant
filling pipeline during the filling process is analyzed
in this paper only in the aspects of filling control
process. In order to further eliminate the water
hammer effect, the research direction in the future is
to improve process design for the filling system.
REFERENCES
Xiang Youhuan, Shi Jinfeng, Li Liqun. Accuracy Analysis
on Measuring Model of Rocket Propellant Filling
Based on Weight Measurement[C]. 2014 IEEE
International Conference on Signal Processing
Communications and Computing (ICSPCC 2014).
August 5-8,2014:760-765.
Yang Zhi-qiang, Zhang Hong-jian, Huang Yong-mei.
Research on data value simulation of fluid field
characteristic of vortex flowmeter [J]. Process
Automation Instrumentation. 2004, 25(5):10-13.
Yan Zheng, Peng Xiao-hui, Cheng Yu-qiang, Wu Jian-jun.
Research of water hammer and its suppression
methods for spacecraft propulsion system. Journal of
Aerospace Power. Sep.2012, Vol.27 No.9:2028-2034.
Lin Jingsong, Wang Pingyang, Gao hong. Numerical
Simulation of Water Hammer in Shutting Liquid
Rocket Engine [J]. Aerospace Shanghai. No.3
2008:53-57.
Nie Wansheng, Dai Haide, Xia Peng. Transient
Characteristics during shutdown operation of liquid
feed line for attitude control propulsion system [J].
SIMULTECH2015-5thInternationalConferenceonSimulationandModelingMethodologies,Technologiesand
Applications
342