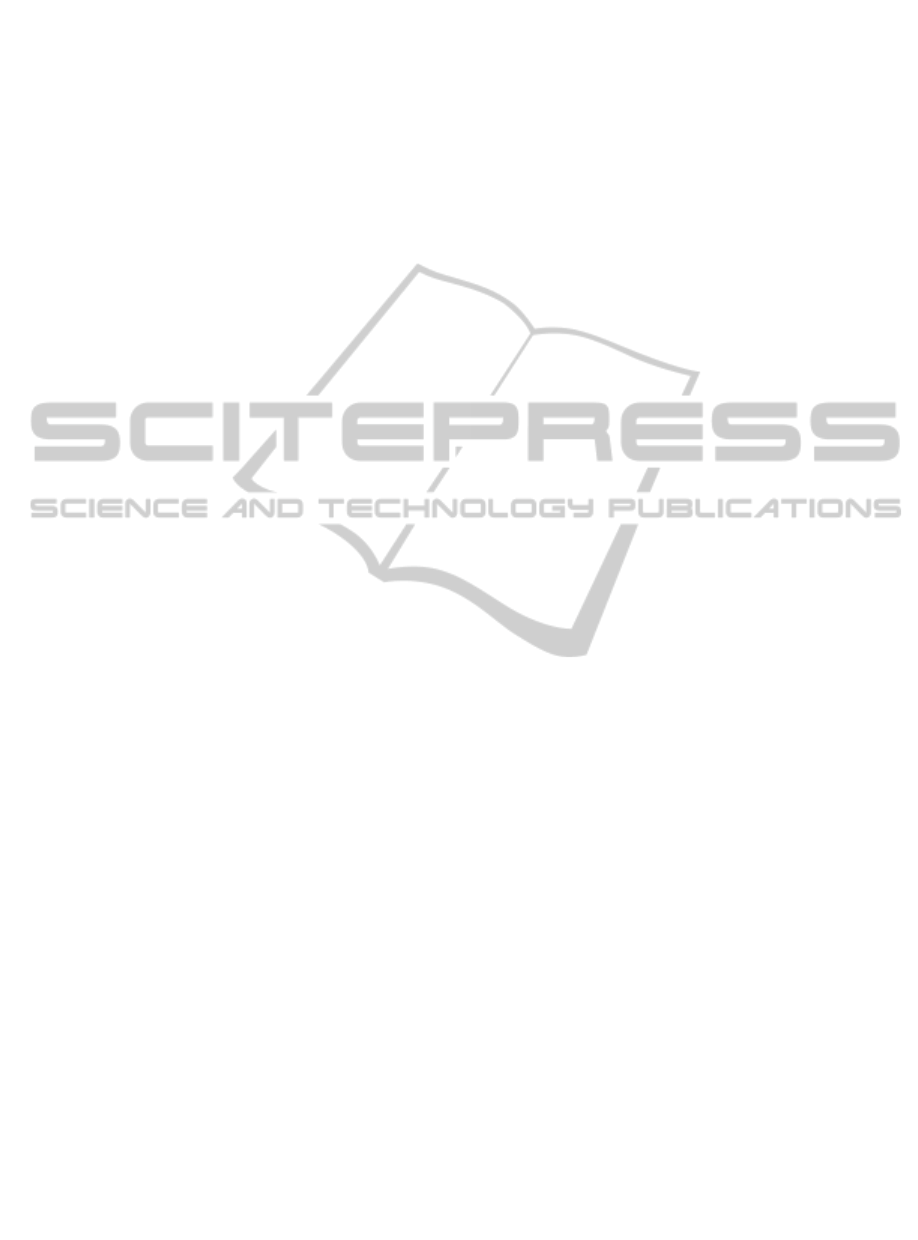
4 CONCLUSIONS
In this study, first of all, equilibrium-controlled
actuator, antagonistic-controlled actuator, structure-
controlled actuator, mechanically-controlled actuator
and controllable transmission ratio type actuator
designs are presented in detail. Then, all equations
have been derived for the design of an antagonistic,
pre-tension and controllable transmission ratio type
actuator designs. In the following section, these
designs are compared in terms of energy
consumption and power requirement at an optimal
walking speed for ankle joint. According to the
simulation results, as controllable transmission ratio
type actuator requires less power and consumes less
energy, it is more feasible than the antagonistic and
pre-tension type designs for the joints of exoskeleton
robots, orthoses, protheses and humanoid robots,
which are supplied by the batteries.
ACKNOWLEDGEMENTS
The authors would like thank to TUBITAK (The
Scientific and Technological Research Council of
Turkey) for the financial support with a research
project titled as “Design and control of a biomimetic
exoskeleton robot”.
REFERENCES
Alexander R., 2010. Three uses of springs in legged
locomotion. Int. J. Robot. Res. (Special Issue on
Legged Locomotion), vol. 9, no. 2, pp. 53–61.
Bovi G., Rabuffetti M., Mazzoleni P. and Ferrarin M.,
2010. A multiple-task gait analysis approach:
kinematic, kinetic and EMG reference data for healthy
young and adult subjects, Gait and Posture, vol: 33
pp.6-13.
Holgate M. A., Hitt J. K., Bellman R. D., Sugar T. G. and
Hollander K.W., 2008. The SPARK (Spring Ankle
with Regenerative kinetics) project: Choosing a DC
motor based actuation method. 2nd IEEE RAS &
EMBS International Conference on Biomedical
Robotics and Biomechatronics, pp.163-168.
Hollander K. W., Ilg R., Sugar T. G. and Herring D.,
2006. An efficient robotic tendon for gait assistance. J.
Biomech. Eng.,vol. 128, no. 5 pp. 788-91.
Jafari A., Tsagarakis N., Vanderborght B. and Caldwell
D., 2010. A novel actuator with adjustable stiffness
(AwAS). IEEE/RSJ International Conference on
Intelligent Robots and Systems, pp.4201–4206.
Jafari A., Tsagarakis N. and Caldwell D. G., 2011. AwAS-
II: A new actuator with adjustable stiffness based on
the novel principle of adaptable pivot point and
variable lever ratio. IEEE International Conference on
Robotics and Automation, pp. 4638–4643.
Migliore S. A., Brown E. A., and DeWeerth S. P., 2005,
Biologically inspired joint stiffness control. IEEE Int.
Conf. Robotics and Automation, pp.4519–4524.
Pratt G. A., and Williamson M. M., 1995, Series elastic
actuators,’’ in Proc. IEEE Int. Workshop on Intelligent
Robots and Systems. Pittsburg, USA, pp.399–406.
Van Ham R., Vanderborght B., Van Damme M., Verrelst
B. and Lefeber D., 2007. MACCEPA, the
mechanically adjustable compliance and controllable
equilibrium position actuator: Design and
implementation in a biped robot. Robot. Autonom.
Syst., vol. 55, no. 10, pp. 761–768.
Vanderborght B., Albu-Schaeffer A., Bicchi A., Burdet E.,
Cald-well D., Carloni R., Catalano M., Ganesh G.,
Garabini M., Grioli G., Haddadin S., Jafari A.,
Laffranchi M., Lefeber D., Petit F., Stramigioli S.,
Grebenstein A., Tsagarakis N., Van Damme M., Van
Ham R., Visser L. And Wolf S., 2012. Variable
impedance actuators: Moving the robots of tomorrow.
IEEE/RSJ International Conference on Intelligent
Robots and Systems, pp. 5454-5455.
ComparisonofControllableTransmissionRatioTypeVariableStiffnessActuatorwithAntagonisticandPre-tensionType
ActuatorsfortheJointsExoskeletonRobots
195