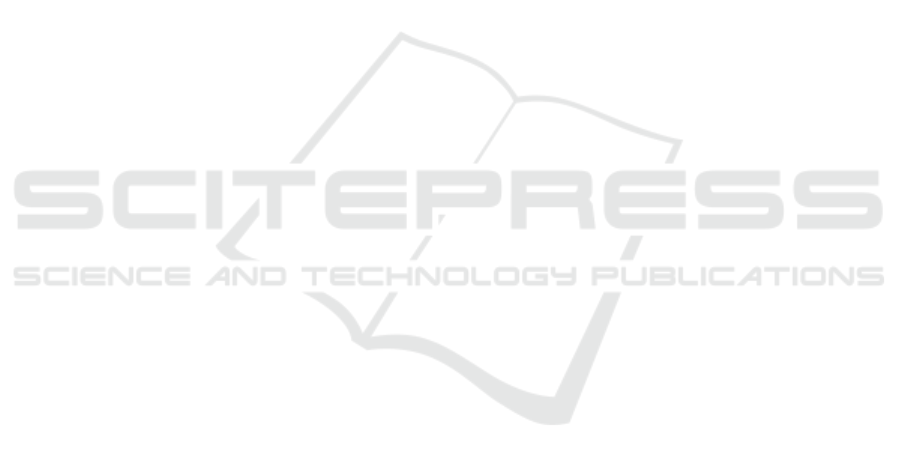
Discrete Sliding Mode Control for a VCM Positioning System
Kuo-Ming Chang
1
, Huang-Sheng Kung
1
and Yung-Tien Liu
2
1
Dept. of Mechanical Engineering, National Kaohsiung University of Applied Sciences, Chien-Kunng Rd.,
Kaohsiung, Taiwan
2
Dept. of Mechanical and Automation Engineering, National Kaohsiung First University of Science and Technology,
Kaohsiung, Taiwan
Keywords: Discrete Sliding Mode Control, Voice-Coil Motor (VCM), Proportional-Integral Observer, Precision
Positioning.
Abstract: In this paper, a discrete control system is implemented for a positioning device using a voice-coil motor
(VCM). The VCM positioning system is configured with a proportional-Integrator observer (PIO) and
discrete sliding mode controller (DSMC). Since the PIO could estimate system unmeasurable parameters for
compensation, the implemented control system subject to uncertainty might feature high robustness.
Through experimental examinations of step response for a sliding stage under dry friction and with a mass
of 728 g, the position error of 7.3 m was obtained for a step command of 3 mm. The percentage of position
error is 0.25%. Compared with that obtained by using the PID controller is 0.57%, the superiority of the
implemented control system is demonstrated.
1 INTRODUCTION
Positioning system is one of the fundamental
technologies that supports the development of
precision machinery such as machine tool. Recently,
due to significant progress in precision industry, the
needs for miniaturized devices are increasingly
presented. In positioning system, the direct drive that
can transmit power without gear reducer might
feature compact size. This is very attractive in
miniaturization. Therefore, the direct drives using
linear actuators such as piezoelectric actuator, piezo-
magneto actuator, ultrasonic motor, linear motor,
voice-coil motor (VCM), and static electric actuator,
etc., are well found in industry.
In this paper, the control performance of the
positioning system using the VCM is studied. The
actuation of VCM is based on the principle of
electromagnetic effect. Due to its simple structure,
compact size, and high precision, popular
applcations can be well found in hard disc drive and
automatic image foucusing device. However, these
applications are with constraint conditions of small
laod and almost friction-free motion. It is well
known that the friction force behaves remarkable
nonlinearity in microscopic motion. Therefore, the
positioning device under dry friction is very diffcult
to obtian high precision positioning. To cope with
the nonlinear system, controller desgin with
excellent robustness is very essential. In this study,
the control scheme of the discrete sliding mode
controller (DSMC) coupled with proportional-
integrator observer (PIO) is proposed for the VCM
positioning system under dry friction. The proposed
DSMC coupled with PIO is aimed at improving
robustness of the positioning system and providing
compensating function for external disturbances.
Relating to the controller design, a PIO was
verified as effective in estimating system state and
disturbance (Hsu, 2007). Regarding the DSMC, two
approximation laws of exponential and variable rate
were examined. Due to the drawbacks of current
approximation laws, two new approximation laws
being capable of reducing control chattering
phenomenon of switching surface were proposed.
Based on numerical simulations, a more stable
system locating at the origin was verified (Yan,
2006). Moreover, an adaptive DSMC coupled with
new exponential approximation law was proposed.
This system was shown as stable at the origin and
successfully applied to a DC motor driving system
capable of tracing a reference signal (Lizhong, 2007).
Different to the control algorithm, the switching
control of delay time was focused for examining the
465
Chang K., Kung H. and Liu Y..
Discrete Sliding Mode Control for a VCM Positioning System.
DOI: 10.5220/0005511204650472
In Proceedings of the 12th International Conference on Informatics in Control, Automation and Robotics (ICINCO-2015), pages 465-472
ISBN: 978-989-758-122-9
Copyright
c
2015 SCITEPRESS (Science and Technology Publications, Lda.)